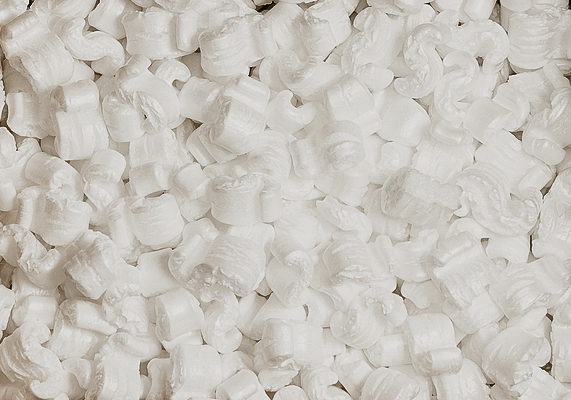
Sensor combination for efficient level control in the EPS industry
A distinguished expanded polystyrene (EPS) manufacturer was facing unique challenges with their level instrumentation due to the specific characteristics of these materials. The very low bulk densities of these products, combined with their particular storage conditions, made it difficult for traditional level sensors to accurately detect and measure levels. To address this issue, UWT provided a unique and effective solution by installing two different level sensors: a rotating paddle from the
and a .
Integration of rotary paddle level switch and vibrating fork with vibrasil 90 for precise monitoring in EPS and material silos
The Challenge: Particular material properties and storage conditions
In an expanded polystyrene (EPS) production plant, two major challenges needed to be addressed for effective and reliable operation. Firstly, EPS has a very low bulk density, causing the material to settle and compress at the bottom of the silos. This compression can create a denser and more compacted layer, which facilitates the operation of certain types of level sensors. However, as the level of the material rises, the density and compression decrease, so sensors with high contact sensitivity are needed. Secondly, EPS products are processed and stored in fabric silos. This flexibility complicates the installation of traditional level sensors, as the weight of these devices can make them unstable and cause sagging, leading to measurement errors.
The Solution: Integrating rotary paddle and vibrating fork technologies
To address these challenges, UWT Level Controls implemented a unique and effective solution by installing two types of level sensors: one with a rotating paddle and the other with a vibrating fork.
For low-level detection, the Rotonivo® 4001 sensor was selected for its capability to operate effectively in conditions with lower bulk densities. The sensor's rotating paddle can reliably detect material presence at lower levels of the silo, where material density and compression provide adequate resistance. Additionally, its plastic housing and special rubber paddle make it a very lightweight sensor, perfect for mounting at low levels and reducing sag in cloth bins.
For high-level detection, the Vibranivo® 6020 was installed to ensure accurate and reliable level detection at the top of the silo, where the material density is even lower. Enhanced with a Vibrasil 90, this sensor can detect EPS grinds with a bulk density of less than 1 lb/ft³ (~16 g/l). The vibrating fork technology offers faster response times and tip sensitivity, optimizing production efficiency by providing quick responses at high-level marks.
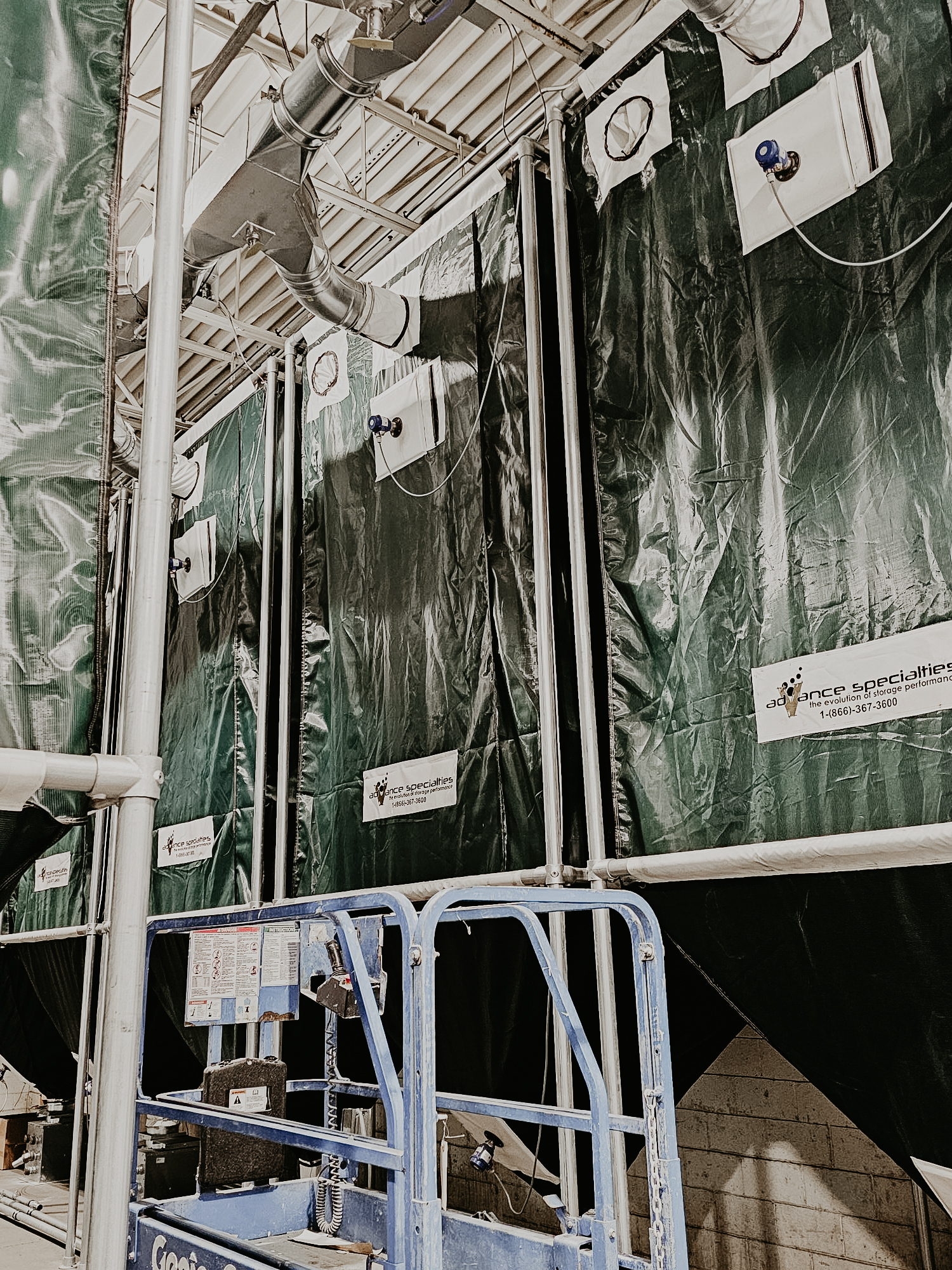
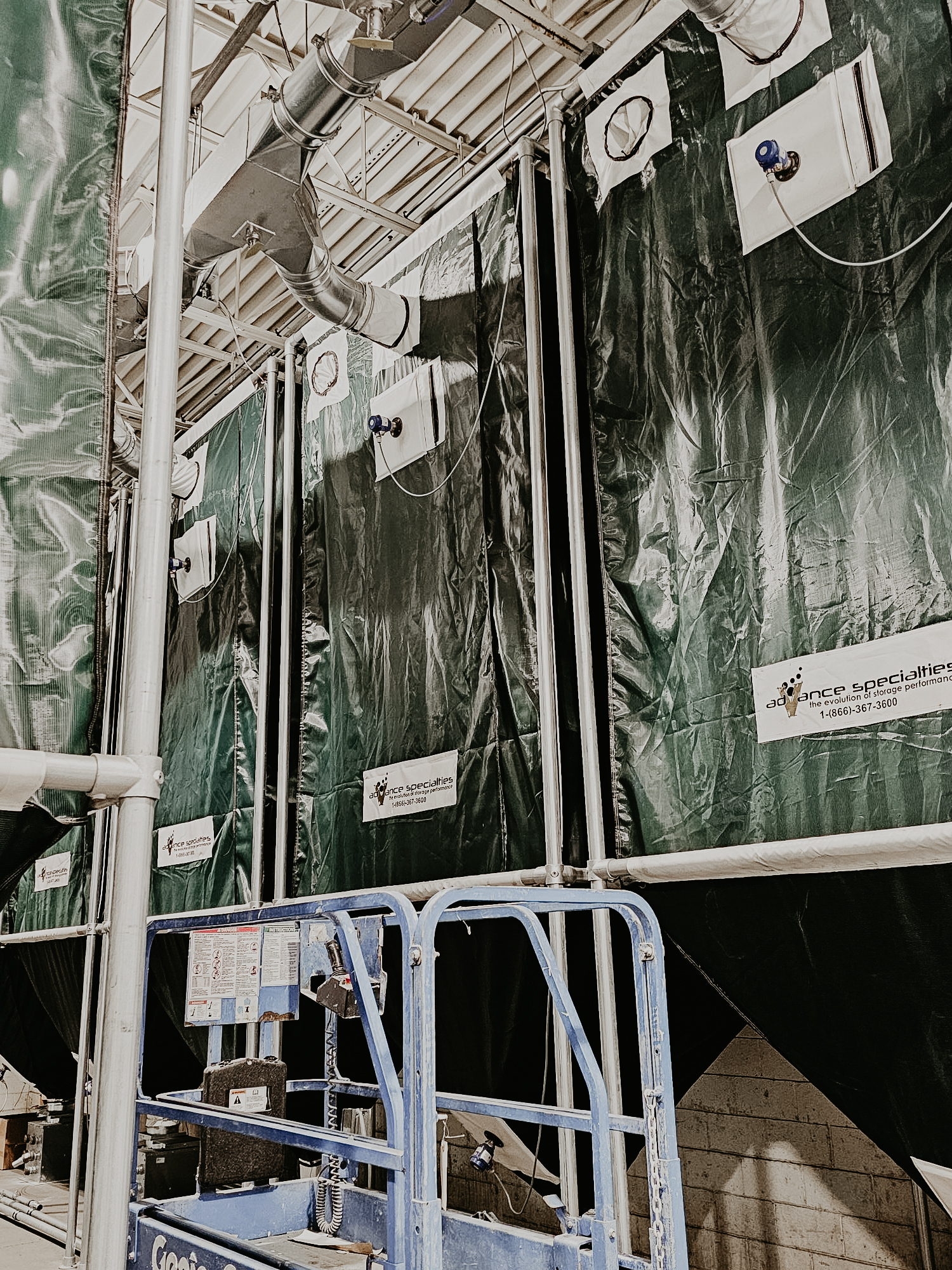
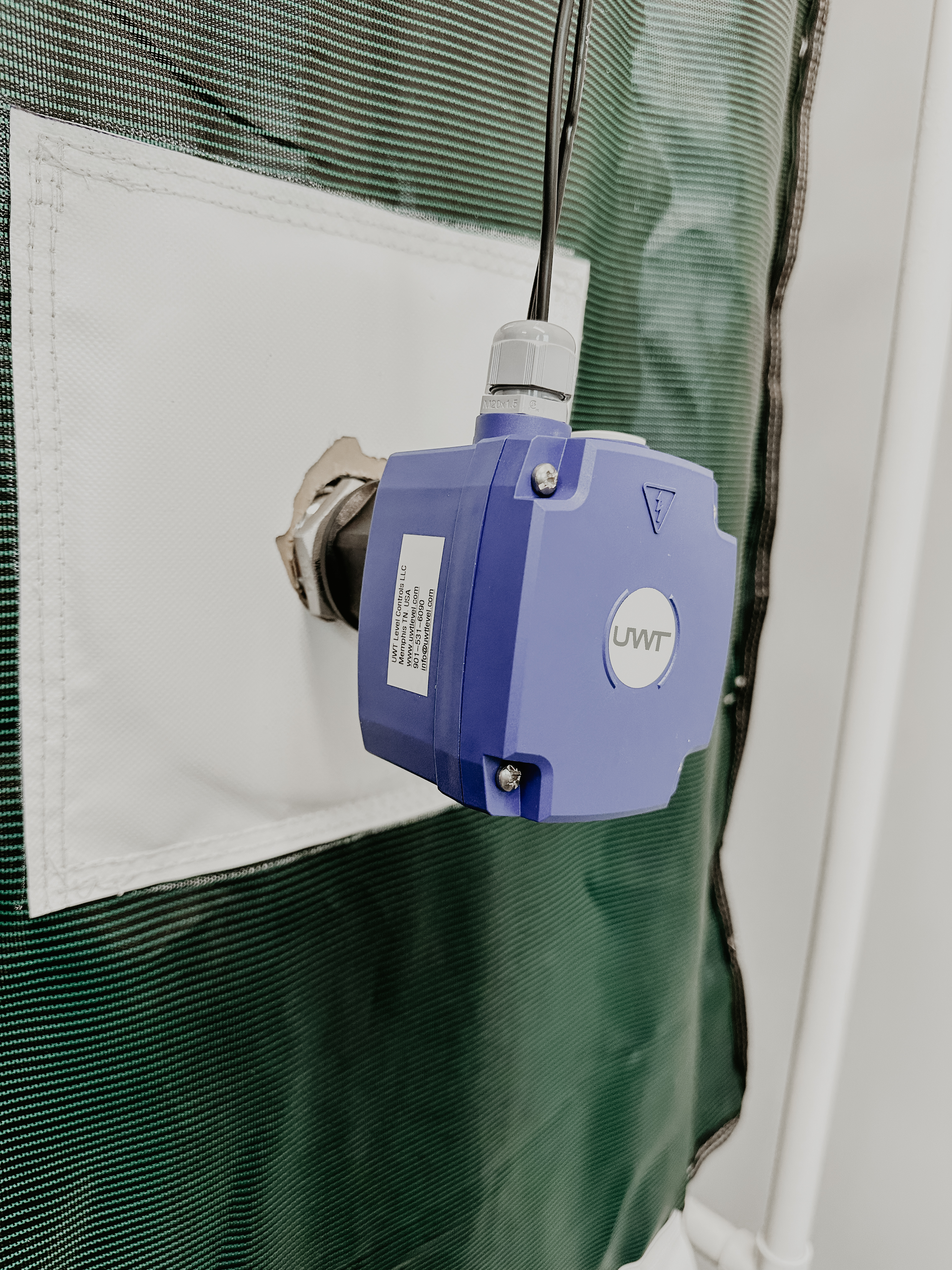
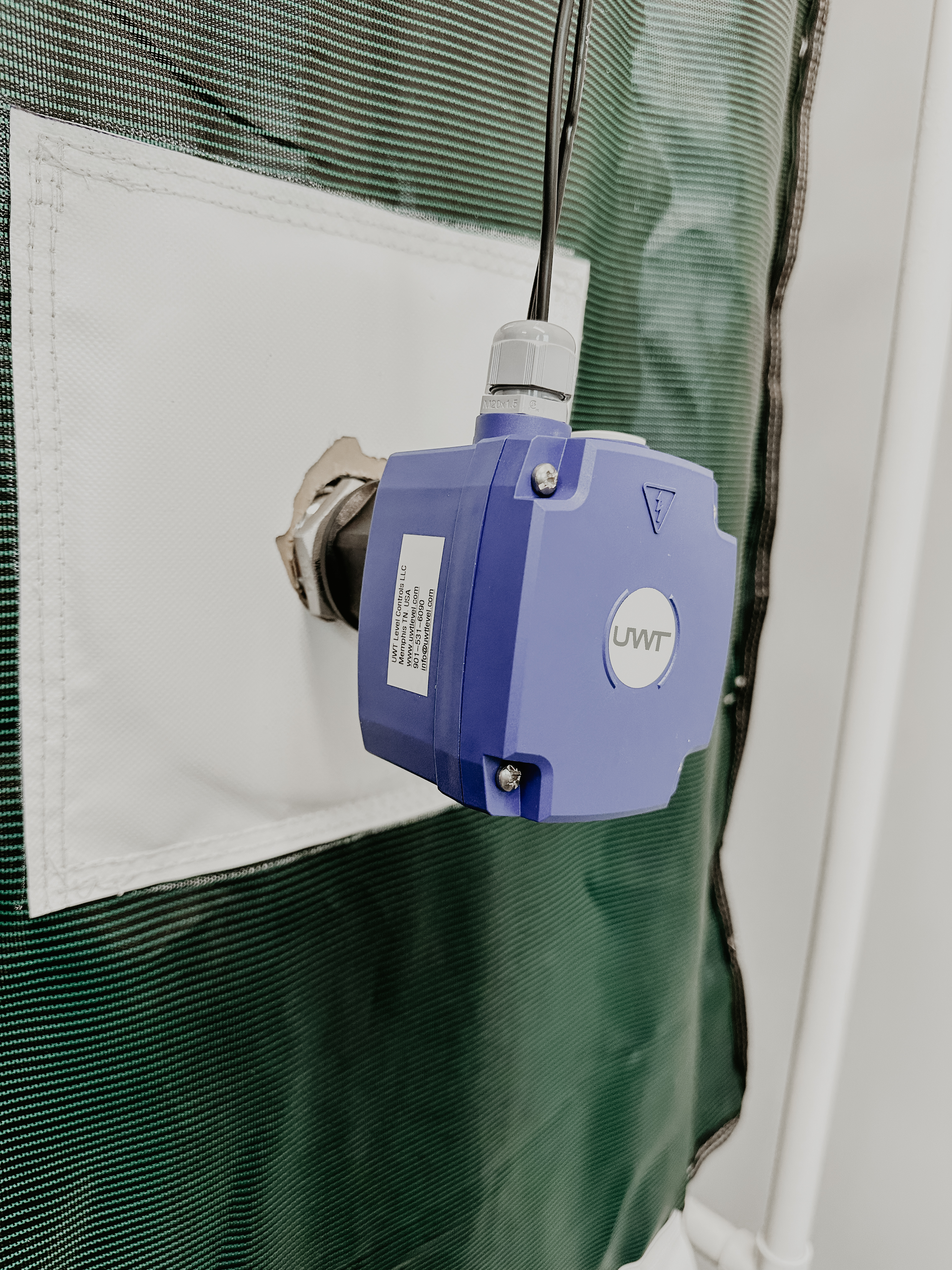
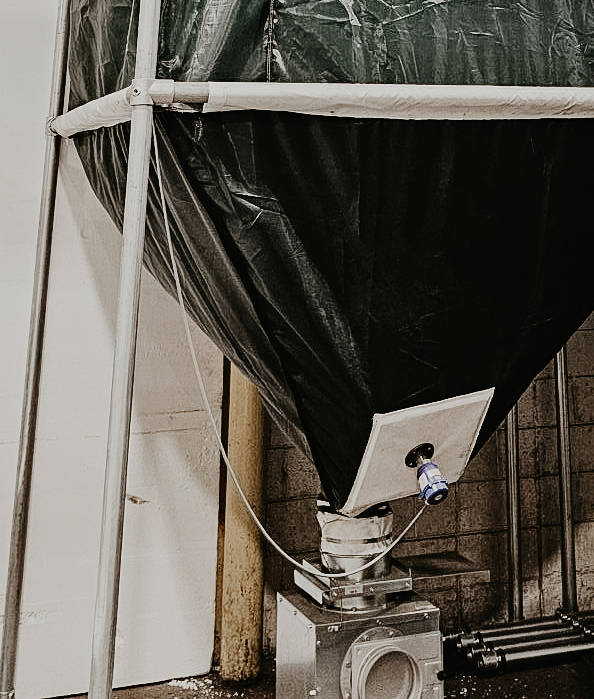
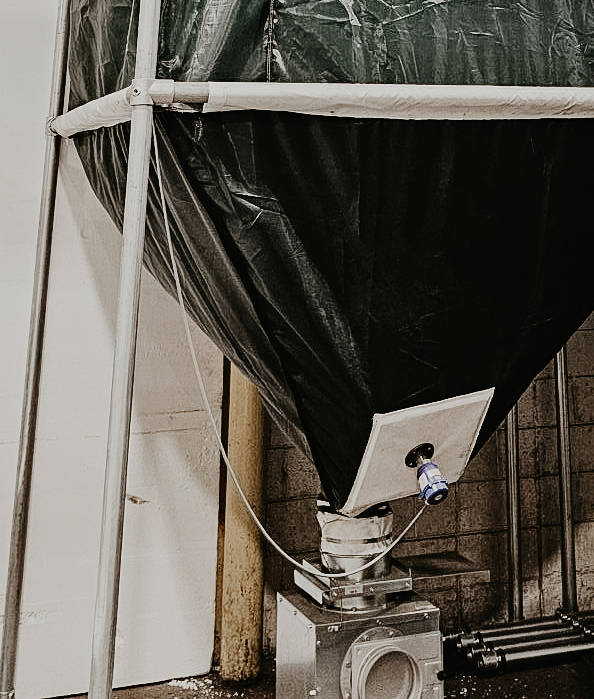
Tailored solutions for diverse applications
Through the integration of the Rotonivo® 4001 and Vibranivo® 6020 sensors, UWT has once again demonstrated its dedication to overcoming industry challenges. By addressing the unique characteristics of EPS materials and the complexities of fabric silo environments, UWT has provided a tailored solution that ensures precise monitoring and control of material levels in diverse operational conditions. This dual sensor approach not only enhances reliability and accuracy but also underscores UWT's commitment to advancing technology for effective industrial solutions.
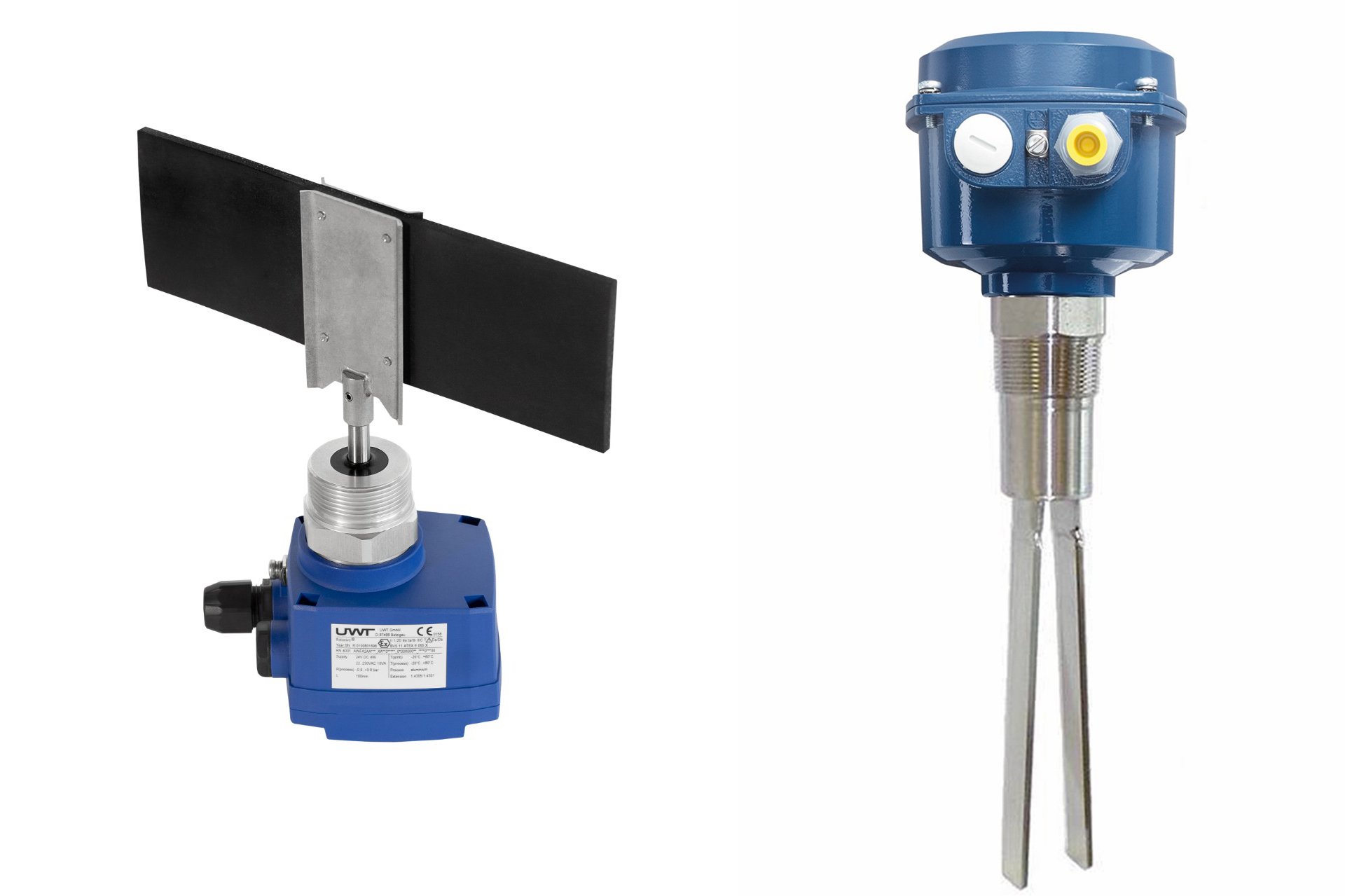
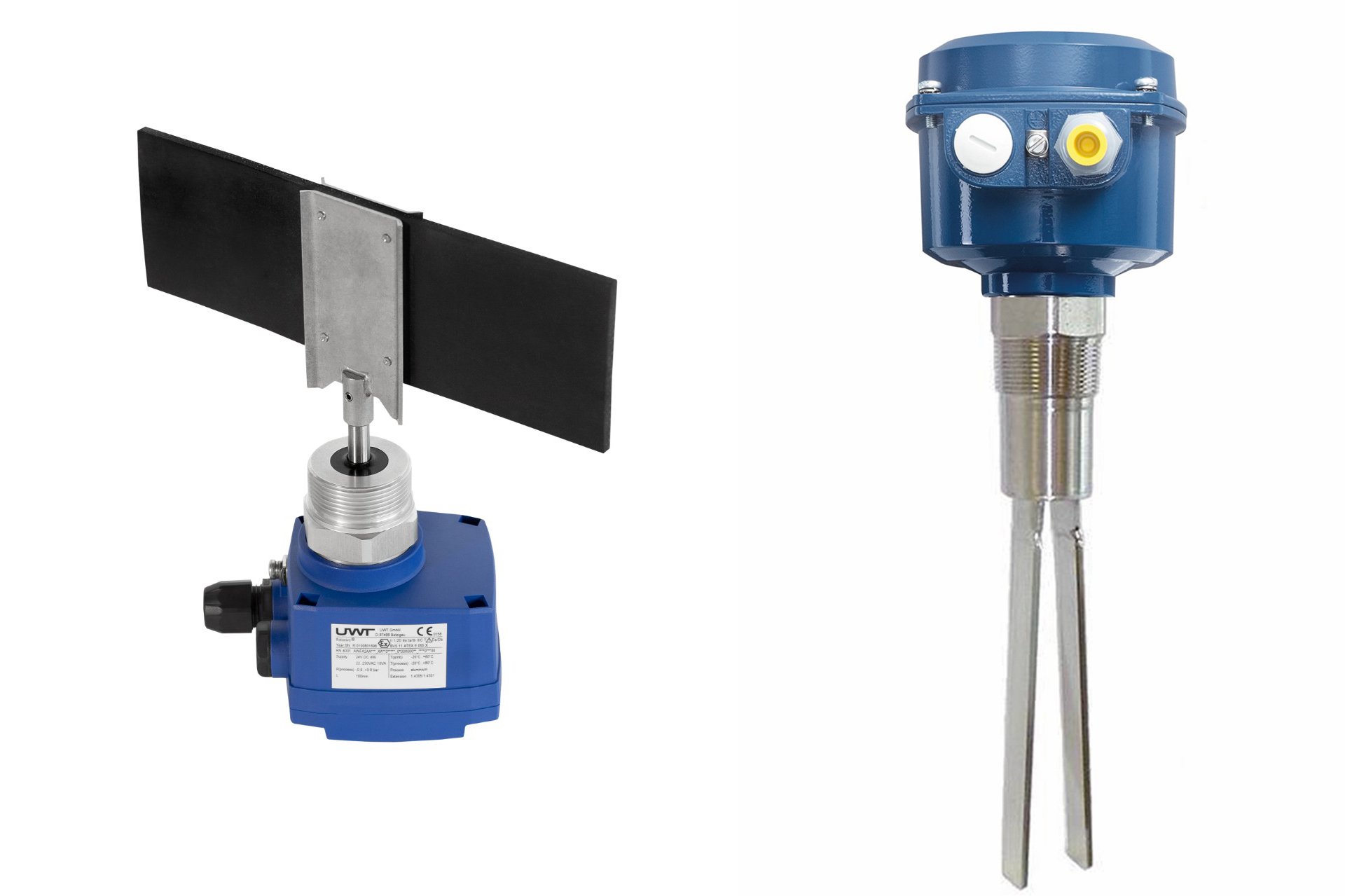
Rotonivo® 4001 and Vibranivo® 6020 with Vibrasil 90