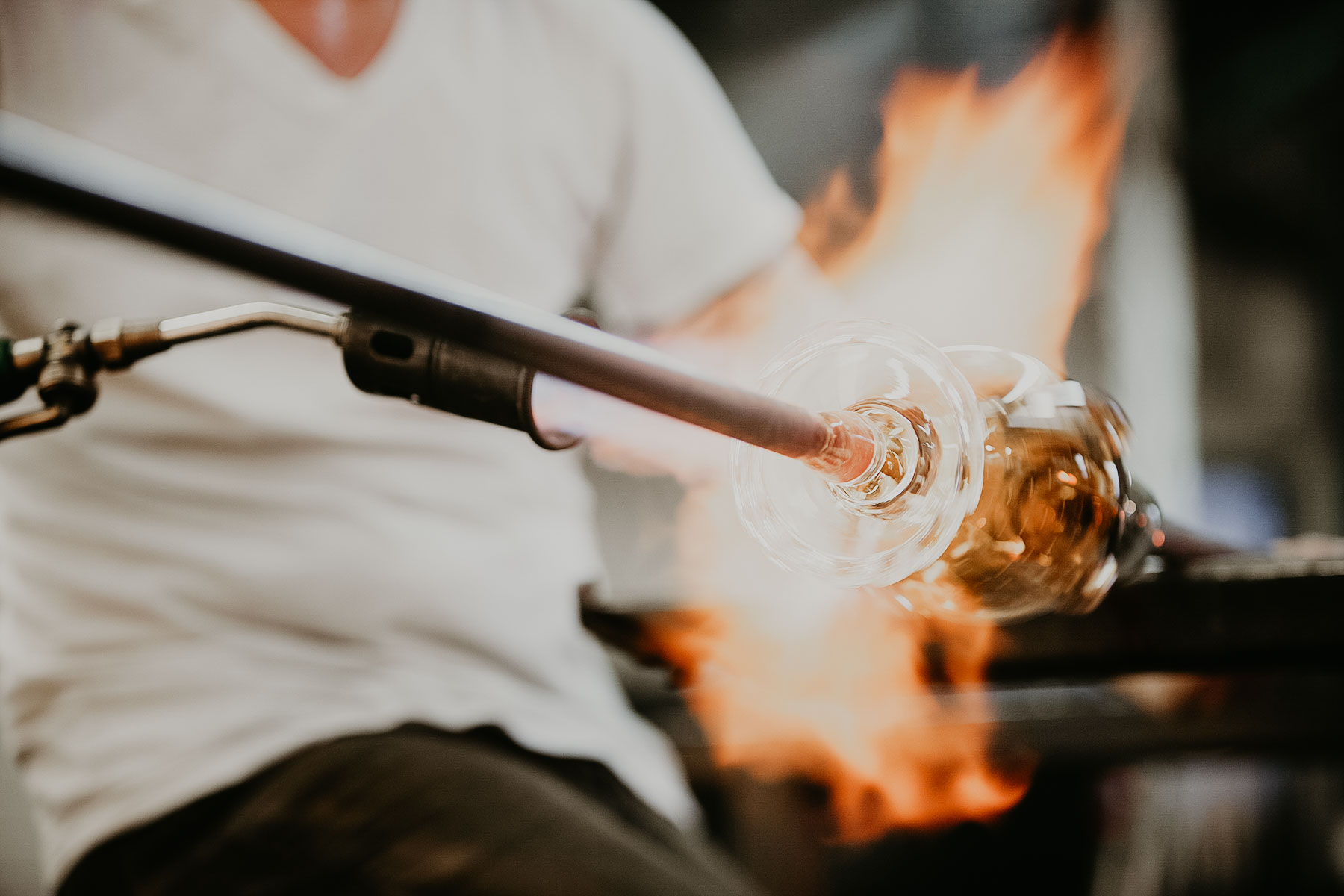
Stay cool! Level measurement at hot temperatures
One of the world's largest manufacturers of glass and ceramics optimized the storage processes with suitable level measurement technology in one of the plants in Seville, Spain. The challenge was to find a dust-resistant measuring technology that would measure reliably under very high ambient temperatures. A suitable solution for continuous level measurement was configured with the non-contact radar sensor from UWT. The highlight was the integrated air purge connection, which enabled regular, cyclical cleaning and cooling of the lens antenna.
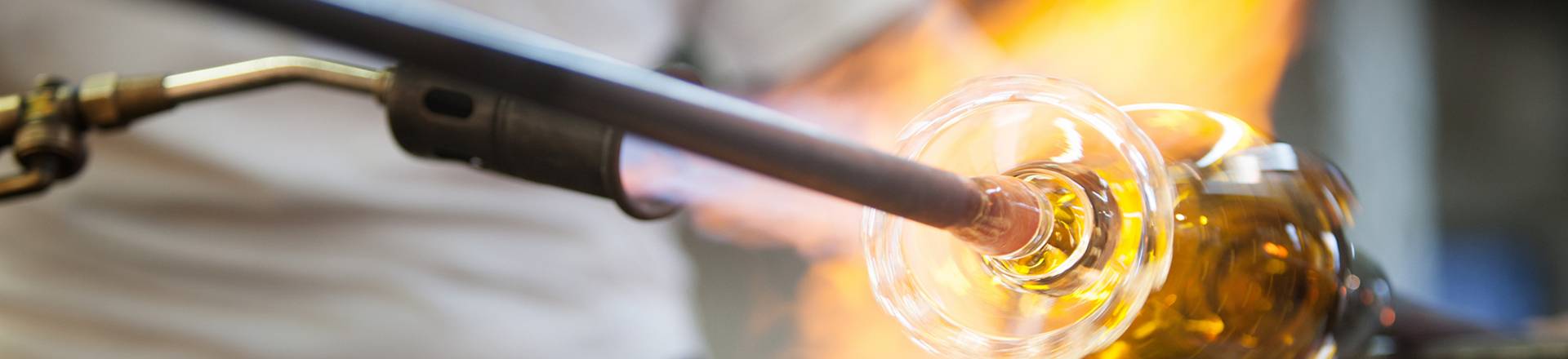
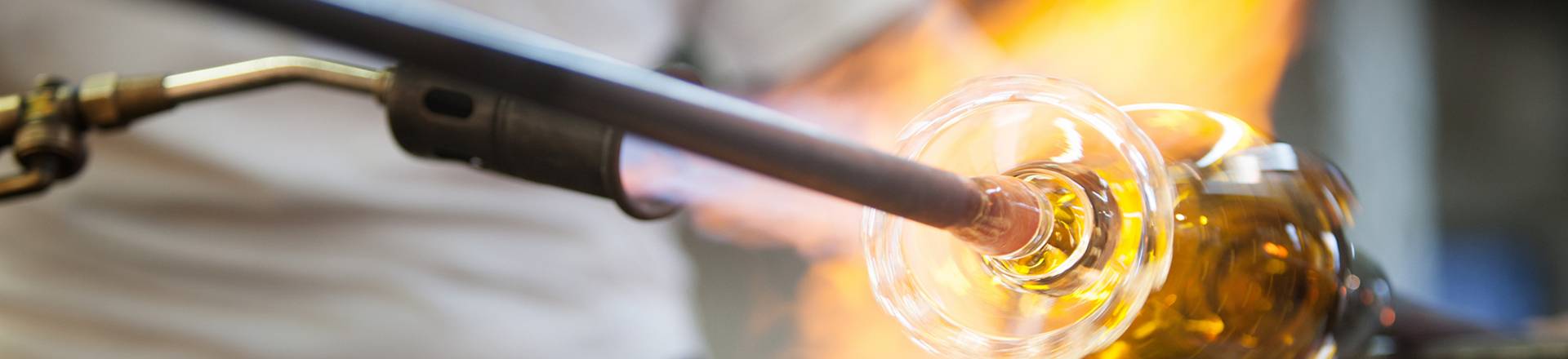
Accurate measurement results with resistant radar sensors
Depending on the end product, there are different mixing ratios of the respective components such as quartz sand, lime, dolomite, potash or feldspar in glass production. In order to support the processes as reliably as possible, an international manufacturer of glass and ceramics was looking for suitable sensors to measure the content of these ingredients. The 35 plants in Europe produce up to 5,000 different glass bottles, jars and containers and ship them to more than 50 countries. In particular, the level measurement for the different storage containers for the solids for the production of glass containers in a plant in Seville needed to be optimized. There, the raw materials are sometimes mixed with broken glass and recycled glass and combined with heat. The height of the concrete single-chamber silos in which the materials are stored is 15 meters. Among these are sand and caustic soda, which are particularly abrasive and aggressive for measuring technology. In the process and in the external environment, there is a high dust intensity combined with humidity and high ambient temperatures. These tend to be over 100 ºC (212 °F) at the installation site.
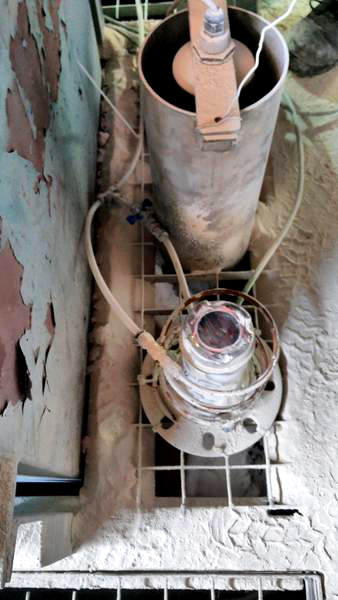
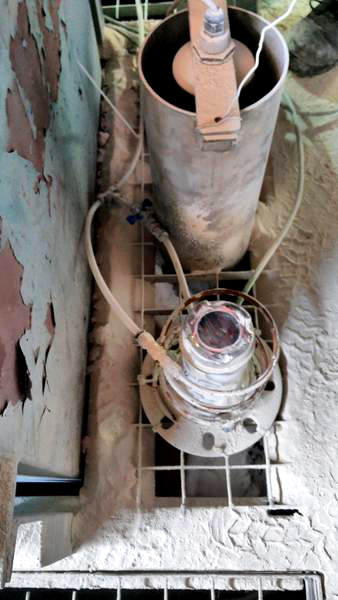
The solids, which tend to stick, have a dielectric constant of 3.0 to 4.0 and form cones of different steepness during the filling process. Together with the local partner Elion, S.A. the free-radiating UWT radar sensor was configured according to the high process temperatures and dusty process environments. This has already been used successfully under extreme application conditions in the building materials and food industries. The 78 GHz technology of the radar sensor with the narrow 4° beam angle produces a reliable level signal. Even during filling, the reflection of the material surface has a high echo reliability.
Crystal clear view with integrated
air-purging connection
Using the air intake integrated into the sensor was particularly crucial. This allows the lens to be kept clean of dust and adhesion, and the ambient temperature can be reduced to as low as 45 °C (104 °F) by blowing in cooler air. In this way, it is possible for the installed devices to measure the levels without any process disturbances and with continuously high performance.
The combination of high dust intensity, caking material and high process temperatures therefore had no influence whatsoever on the measurement results of the NivoRadar® sensor. Commissioning with the quick start wizard was easy and intuitive. The precise and robust radar sensor technology made this non-contact measuring principle the right choice for the plant operator in Seville.