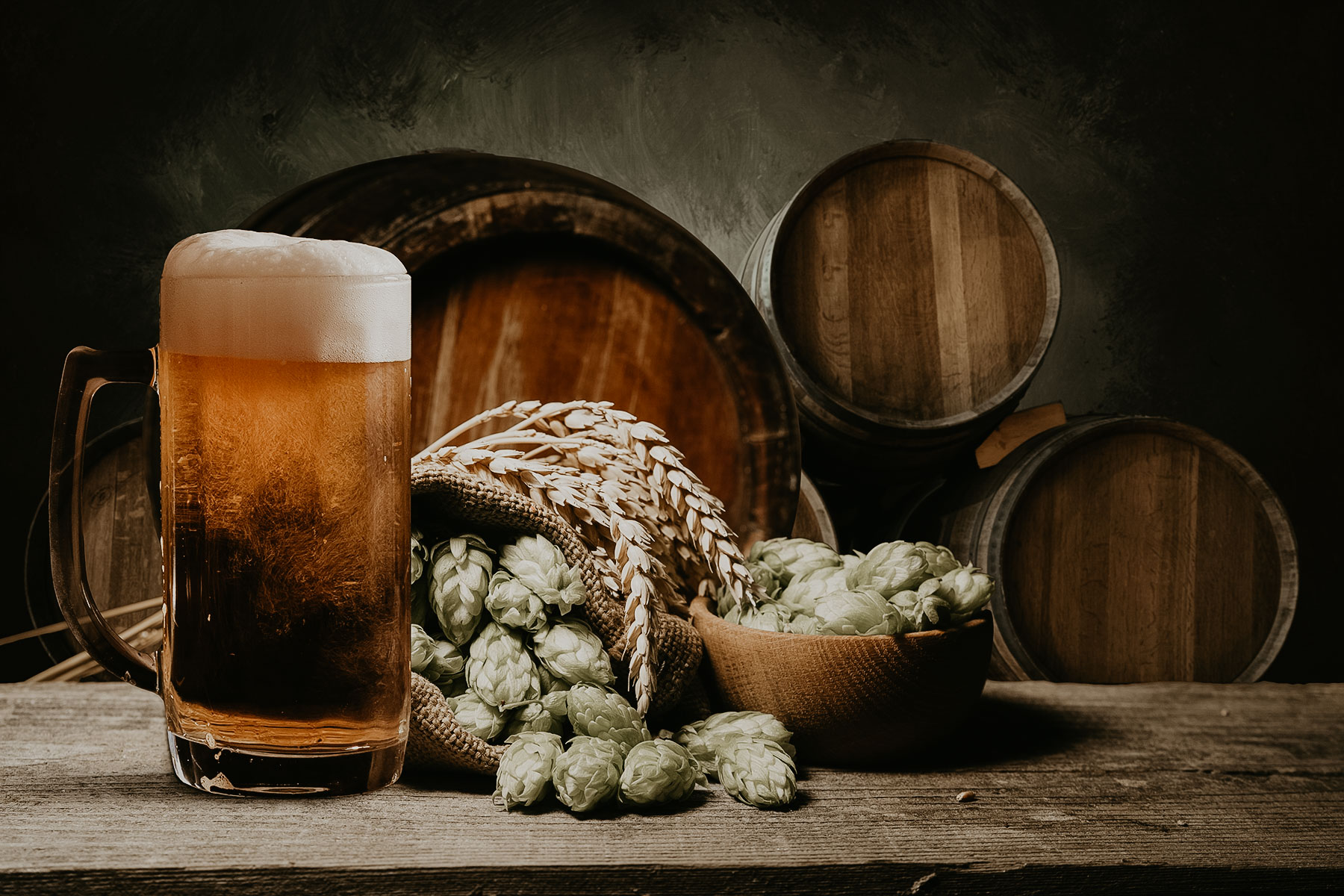
Compensation active du taux & Conformité alimentaire & Aptitude au NEP
Dans l'industrie alimentaire, l'hygiène absolue est d'une importance capitale et la technique de mesure à installer doit répondre à des exigences élevées en termes de design, de fonctionnalité et de fiabilité. Dans l'industrie des boissons en particulier, ces exigences peuvent être très spécifiques. Un fabricant de bière péruvien recherchait des solutions appropriées pour la sécurité anti-débordement ainsi que la protection contre la marche à vide de ses cuves de processus contenant différentes matières premières solides et liquides, nécessaires aux différents processus de production. Pour l'équipement de l'ajout de malt, une étude de projet avec la technologie RF innovante était nécessaire. Des détecteurs de niveau capacitifs d'UWT ont été installés. Ils ont été conçus pour des températures élevées et des applications avec des matériaux à forte adhérence, comme le liquide visqueux du mélange de malt.
Le goût est meilleur quand on connaît ses limites
En 11.000 avant J.-C., l'agriculture et la culture des céréales voient le jour et l'histoire de la bière commence. Des découvertes archéologiques font état de la consommation de bière à Babylone et en Égypte. Différentes techniques de production se développent dans toute l'Europe et plus tard dans le monde entier. En 1824, la marine britannique produit un gallon (4,5 litres) de bière dans le cadre de l'alimentation quotidienne des marins et Pasteur commence ses études sur la fermentation du vin et de la bière. La longue tradition de l'art du brassage se retrouve aujourd'hui dans les plus de 22.000 brasseries du monde entier et la met souvent en pratique avec une technologie de pointe. L'un des principaux fabricants de lagers et d'ale sur le marché péruvien de la bière, avec plusieurs sites de production de bière décentralisés, notamment à Lima, Motupe et Pucallpa, était à la recherche d'une technologie de mesure flexible et sûre dans le cadre de la modernisation de ses installations. L'équipement des processus de macération pour la production de moût s'est avéré quelque peu délicat. La difficulté consistait à contrôler le dosage correct du malt pendant l'ajout dans l'eau pour la dissolution. En effet, les céréales sont devenues très collantes après avoir été mouillées, ce qui a provoqué de fausses alarmes sur tous les capteurs de test.
En collaboration avec le partenaire local d'UWT, SIERRA Servicios Industriales SAC, un détecteur de niveau correspondant a donc été configuré sur place avec le
en version tige, y compris la technologie « Active Shield ». Cette compensation active de l'approche, intégrée dans le principe de mesure capacitif du capteur RF, permet à la sonde de commuter de manière fiable sans être influencée par des accumulations de matériaux. Avec une électrode de protection supplémentaire, la sonde peut mesurer de manière fiable même en présence d'un dépôt fortement conducteur et ignore les dépôts et des adherences.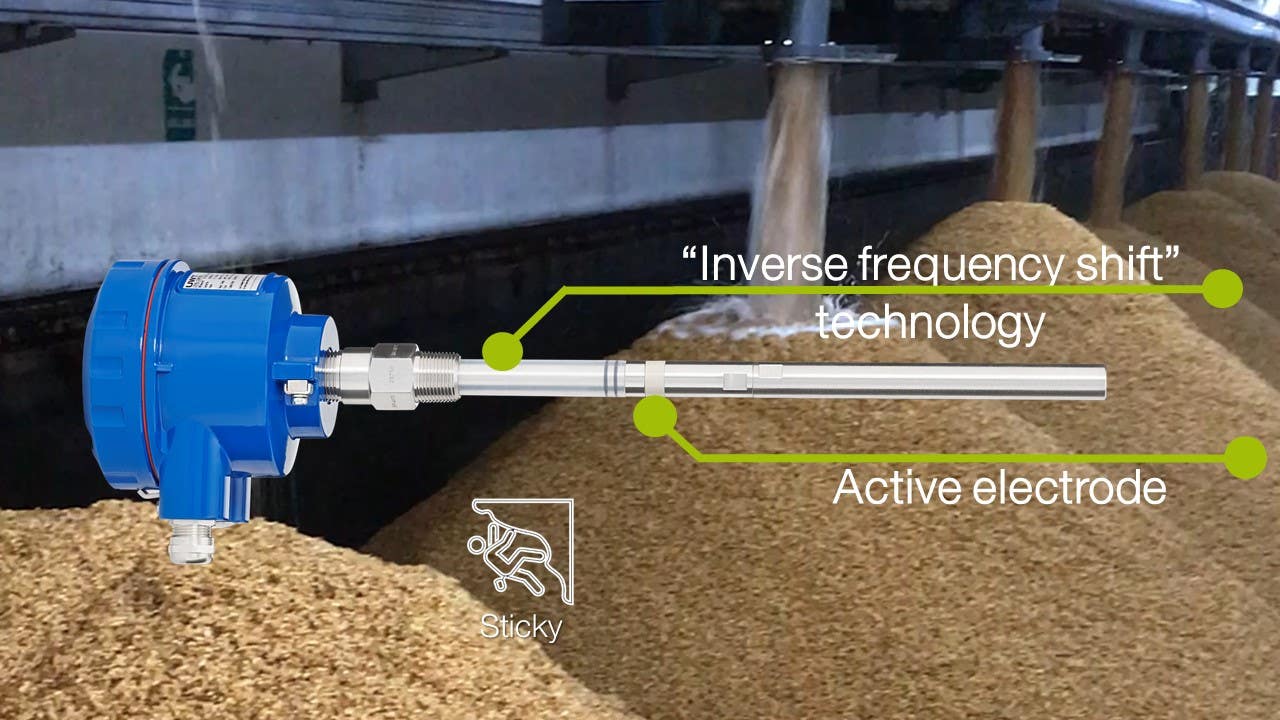
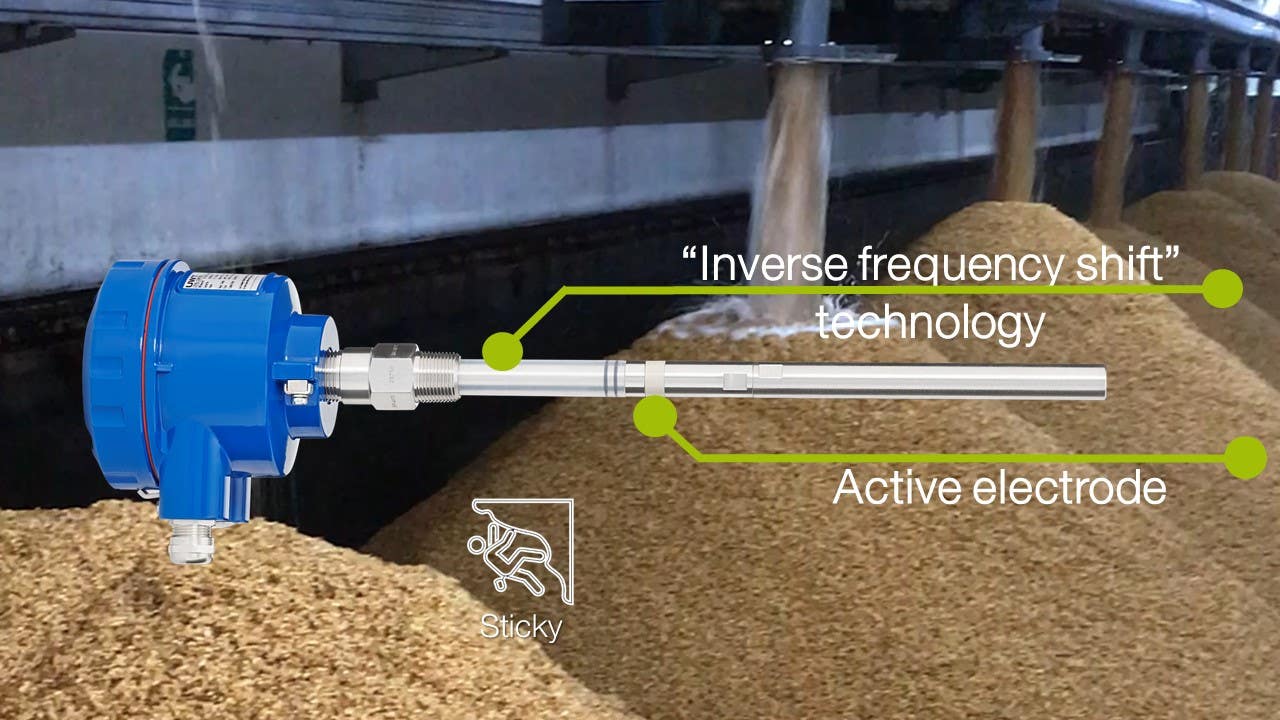
En raison de l'utilisation d'hypochlorite de sodium, la température du processus peut atteindre 80°C (176°F) pendant les processus de nettoyage (NEP). Le bras de la sonde de 250 mm de long a donc été équipé d'acier inoxydable revêtu de PFA, de pièces d'isolation en PEEK ainsi que de joints en FKM. Idéal pour résister au processus de nettoyage agressif à haute température. Outre les homologations Ex standard, les séries RF 8000 sont certifiées selon Lloyd's Register et WHG. Il était également indispensable d'utiliser exclusivement des matériaux conformes aux normes alimentaires pour toutes les pièces de l'appareil de mesure qui entrent en contact avec le produit concerné. La valeur DK du liquide visqueux est d'environ 4,0 et l'atmosphère du processus à l'intérieur des cuves en acier inoxydable est très vaporeuse. Les détecteurs de niveau robustes ont été installés sur le côté des cuves de traitement pour signaler les besoins et réguler l'ajout de malt correspondant dans une plage de mesure de 10 mètres grâce à une détection rapide et précise du matériau.
Une petite variation de la capacité donne une variation relativement importante de la fréquence
Le fait que cette technique de mesure capacitive fonctionne avec la technologie pratique du « Frequency Shift » permet de déterminer le changement de fréquence au lieu de mesurer directement la capacité. Si le récipient est vide, la sonde n'est pas recouverte et la fréquence est élevée, alors que la capacité est faible. Maintenant, le récipient se remplit, la sonde est recouverte et donc la fréquence baisse et la capacité augmente. Ce qui est clair, c'est qu'une petite variation de la capacité entraîne une variation relativement importante de la fréquence. Comme la fréquence peut être évaluée, il est possible de détecter de petites modifications du niveau de remplissage. La précision de mesure est donc très élevée et le capteur peut être réglé de manière très sensible.
Comme les détecteurs de niveau capacitifs RFnivo® fonctionnent sans problème dans les produits en vrac, les granulés, les poudres ainsi que les liquides, les pâtes et les huiles très visqueuses, d'autres silos, réservoirs et cuves de processus de la brasserie ont été équipés de ces détecteurs de niveau pour la signalisation de plein, de besoin et de vide. Même dans les trémies, les tuyauteries et les tuyaux de descente, les différents modèles d'appareils pouvaient être utilisés de manière flexible. L'installation des détecteurs min / max résistants à la corrosion a permis d'optimiser rapidement et facilement le déroulement des processus des sites de production de bière en ce qui concerne la sécurité anti-débordement et la protection contre la marche à vide, et pas seulement pour le procédé d'ajout de malt.