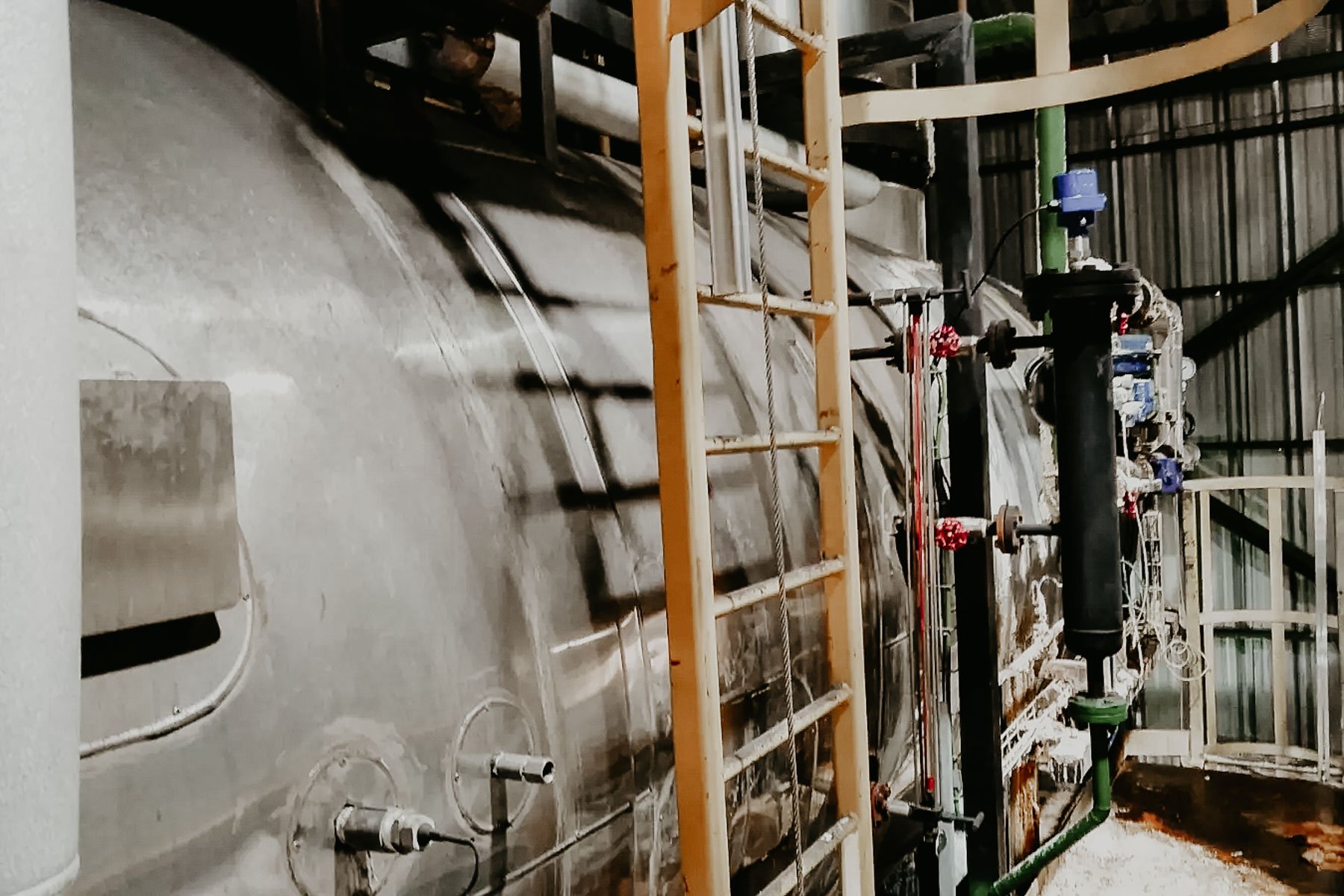
Innovative solutions for the animal feed industry for level measurement with guided wave radar in boilers
When equipping a Chilean plant for animal feed production with compatible level measurement technology, the focus was on high measurement reliability and flexible installation options. Modern guided radar technology was installed within several boilers, which is intended to ensure a continuous production process, unaffected by changing process conditions. Unwanted downtimes could thus be reliably prevented. The installed UWT devices with special high-quality booms offered the operator suitable and economical solutions.
When does the feed company choose guided wave radar?
The production of high-quality animal feed and pet food is an important economic growth sector in South America. In addition to livestock feed, this area also includes pet and sports animal feed. The variety of end products is correspondingly large. Errors that occur in the processing plant during conveying, storage, mixing or granulating can rarely be compensated for or rectified in the next processing step. There, the fill level sensor is an indispensable element of the technical equipment for recording and monitoring the material level, for overfill protection, requirement notification and for emptying protection. With the large variety of different measuring principles and sensor types, choosing the right measuring instrument is not always easy.
In the continuous measurement, the TDR solutions were expanded to supplement the plumbing system and non-contact radar technology. Depending on the process conditions and the medium to be measured, the appropriate sensor technology can be configured for systems from an extensive repertoire. TDR sensors (Time Domain Reflectometry) or GWR (Guided Wave Radar) or guided radar sensors are extremely versatile, which is why they can be found in a wide variety of applications and industries. In addition to the technology-related advantages of guided radar, the user-friendliness of the sensors is another reason for their widespread use.
Reliable level measurement for special installation situations
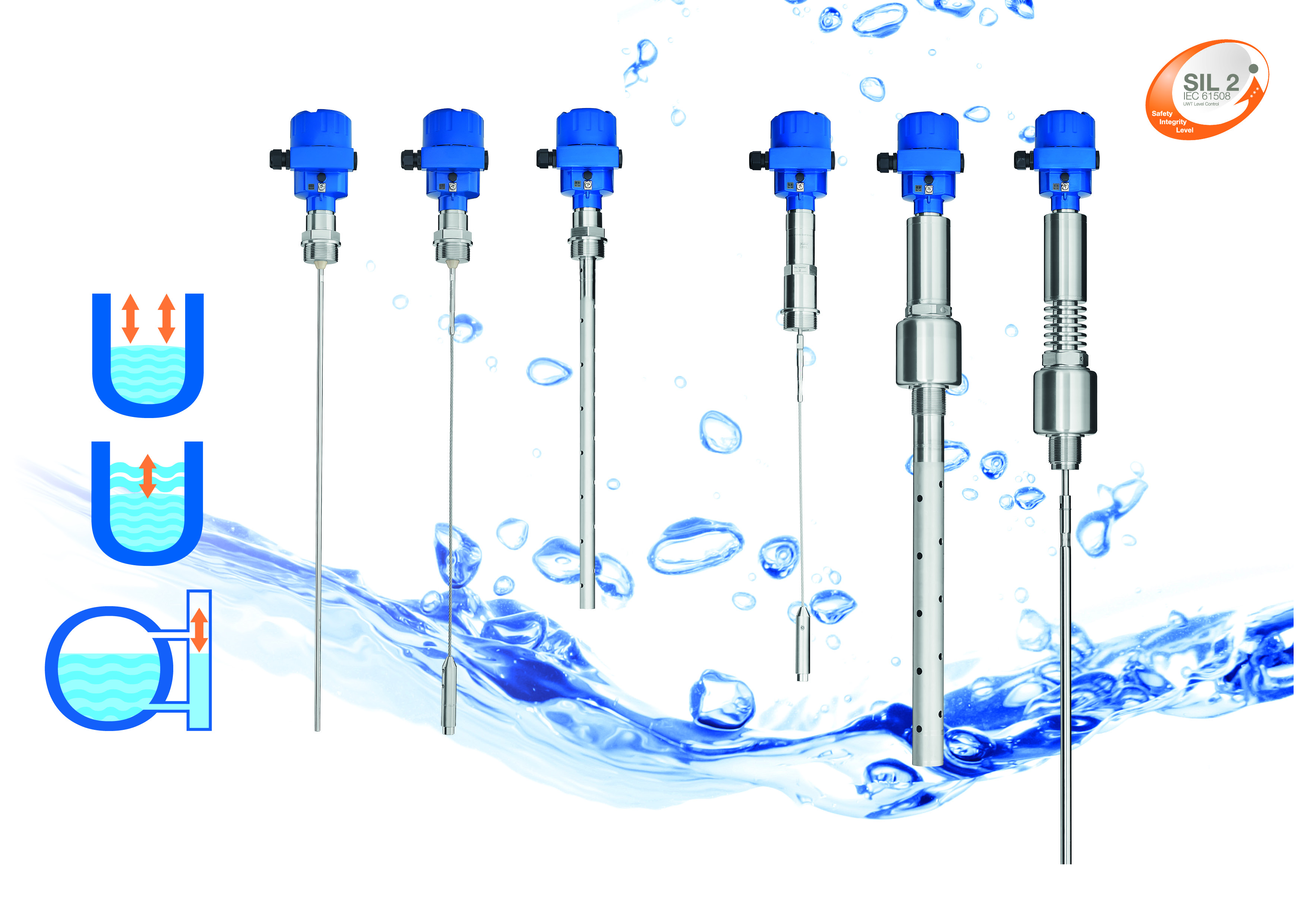
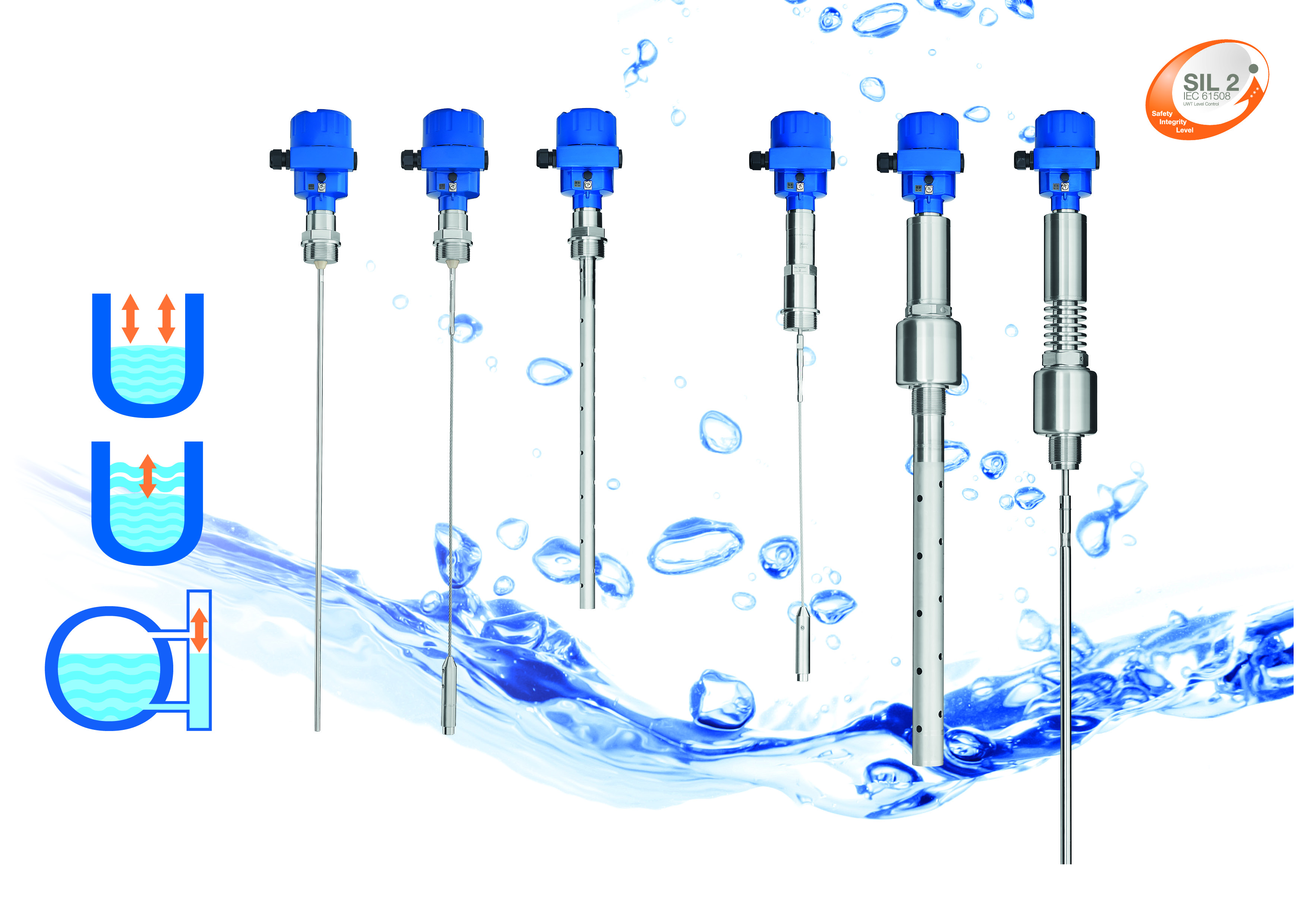
The process environment of a feed processing plant in southern Chile is characterized by factors such as humidity, high temperatures and atmospheric steam. The plant operator was specifically looking for a suitable solution with regard to sensors for measuring the contents of its lye cooking plants. Installation should be in a 500mm bypass of a 2m diameter cylindrical tank. It was crucial to keep the temperature at around 100 ºC. Together with the local UWT partner VESET y Cia. Ltda. After some tests in the system, the NivoGuide® 8000
radar sensor with guided wave was implemented on site for content reporting. This measures the level of liquids or oils of any kind.
In addition to the level measurement of the total level, the TDR sensor can also be used to reliably and precisely record a separating layer that forms between two liquids. Thanks to the robust sensor design and the variety of versions, the radar sensors are suitable for use in large storage silos and tanks as well as in small process vessels or bypass pipes. High-frequency microwave pulses are coupled to a cable or rod and guided along the probe. The emitted impulse is reflected by the product surface. The time difference between the transmitted and reflected pulse is converted into a fill level.
The Chilean animal feed manufacturer has already installed the guided radar in some of its storage processes for different raw materials. The radar sensor was again used for the implementation of the NivoGuide® 8000 devices within the boiler of his lye cooking systems due to its design and the precise measurement method. Since these are small tanks with intense vapor, the precision of the built-in sensors is of crucial importance. The 2-wire NivoGuide® sensor was configured with a 500 mm rod probe that can be used at temperatures of up to 150 ºC. The accuracy of the measurement technology is ± 2 mm! It has a very fast response time due to radar technology and is insensitive to steam.