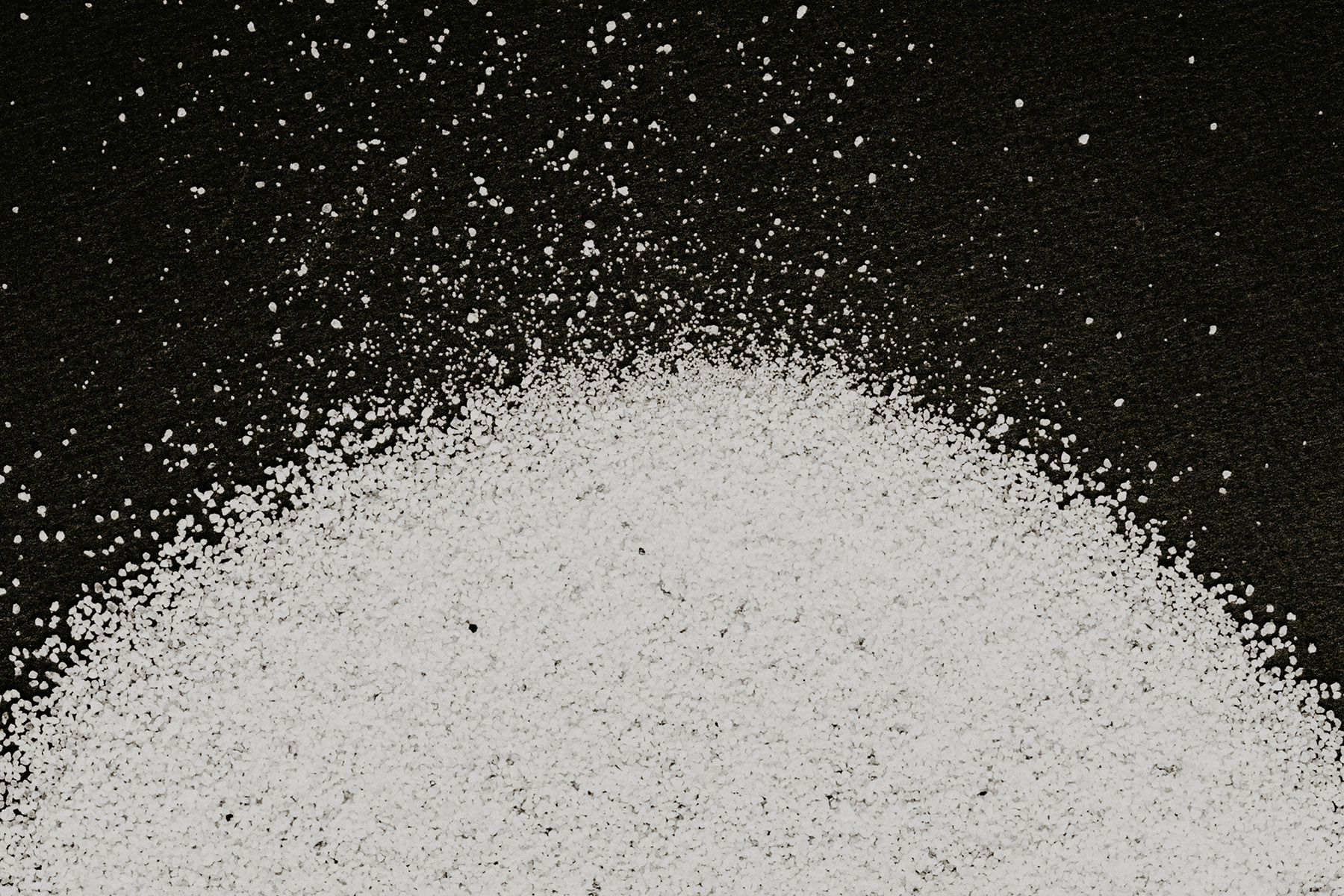
Different project planning options for plant operators with vibrating rod or vibrating fork
When projecting the equipment with measurement technology for plants around the globe, technicians and engineers have noticed that in recent years there has been a noticeable increase in demand for more compact limit switches that have a very high level of compatibility worldwide. There is a demand for measuring solutions that are characterised by common technical features and can be used in very many applications without much configuration effort. Compact, robust single-bars are preferred, for example for small containers in material-processing operations. One design that has become established on international markets has very small connection threads and works according to the vibration principle.
What comes very close to this is the vibrating fork or vibrating fork. The solution spectrum of the comprehensive fork series is wide and it has been successfully integrated into a large number of application projects over the years. Based on the situation, UWT GmbH expanded its product family with a new vibrating fork. This is the perfect complement to the fork models and also offers plant operators worldwide the desired flexibility due to its design. A measuring technology that fits in practically anywhere and at any time without major configuration effort.
Different project planning options for plant operators
To date, many applications have been solved before UWT with the Vibranivo® vibration fork with its multitude of series. The fork works via piezo elements that are excited to vibrate at their mechanical resonance frequency. If the product covers the probe, the resulting damping of the vibration is registered electronically and output as a switching signal. If the probe is uncovered by a drop in level, the fork starts vibrating again and the signal is switched back.
Due to its high sensitivity from 5 g/l, the fork preferably measures light media such as wood dust, polystyrene, plastic powder, flour, milk powder, salt, lime or silicic acid as well as pasty materials. Thus, a wide range of applications can be found in plant processes of different industries. Within the vibration fork family there are five series, each of which can be adapted to customer-specific application requirements:
The Vibranivo® VN 1000 models are predestined, among other things, for interface measurement, such as sand sediments in seawater or sludge in liquid. The most recent installation was used to measure sludge levels in a lamella separator. The polluted water came from an iron foundry. The sludge level measurement was to control a pump that pumped the sludge to a press. Due to the specially developed electronics of this series with an adjustable sensitivity, the probe could be set to the desired switching point, which made the use in this application possible in the first place.
Across industries, the VN 2000 fork series has proven itself many times over. Interesting places of application were, for example, grain plants, textile production, mixing plants for building materials, waste-to-energy plants or in the petrochemical sector. For a plastic processing packaging manufacturer, the Vibranivo® 2000 provided a suitable solution for monitoring the level of plastic powder in the extrusion lines. The unusually light material created a very dusty process environment. Consequently, a completely dust-tight installation of the measuring sensor was indispensable. The encapsulated electronics of the VN sensor and its robust construction with stainless steel vibrating legs were also helpful.
During the final loading of different powdery materials, the plant operator also needed a solution for level detection. Materials that remain behind when the trucks are filled and are collected in separate small containers were to be detected. Since the fork row can be installed vertically, horizontally or at an angle, the sensor could be optimally aligned for reliable detection for each container according to its ergonomic conditions. With the compact boom length starting at 235 mm, the use in smaller process containers could also be realized without any problems.
Measurement technology for safety and economy
The VN 5000/6000 series are the counterpart to the forks of the VN 1000/2000 series. The difference is the design with a flameproof housing as well as the construction for applications with the requirement for increased safety.
The forks of the
series are preferably used in systems where, in addition to technical aspects, price considerations must also be taken into account. For example, the VN 4000 model is often found as a level detector in intermediate containers when a silo system is completely equipped with measuring technology. Its special feature within the vibration forks is that it provides a version with a remote housing (remote version). This allows flexible installation of the housing independent of the distance to the boom. For example, the housing can be mounted at a safe distance from the measuring point for applications in very dusty or hot process environments. In addition, the delivery without extension tube reduces freight costs for the system operator.
Solutions for particularly light materials
In addition, there are special versions of the Vibrasil® vibration fork probe for very light and pneumatically conveyed bulk materials. Because of the high sensitivity and fast switching response, reliable detection is also possible for materials with a bulk density of less than 5g/l. For example, silicic acid is such an extremely light medium. It is often used for further processing in silicone, electrical components or for paper coating. One project showed another area of application for UWT measurement technology in silicic acid. A manufacturer of insulation solutions stored silicic acid in smaller silos for further processing for heat and cold insulation panels. In this silo, the fill level was to be continuously monitored, the full and empty signals were to be given and a probe was to be used in the pipe branch for discharge monitoring. The problem was that this application was very dust-intensive and the bulk density of silica is very low, especially in a fluidised state. Especially during filling, the fluidised silica had an extremely low density. Therefore, it was decided to install the Vibrasil® fork probes. They switch almost without delay and are able to detect even the very light surface of the silica during the filling process.
The Vibrasil® 70 was used in the discharge branch, which detected the material flow with the help of a boom with an aluminium paddle. Vibrating fork probes of the Vibrasil® 90 models were installed as full and empty detectors. These could be mounted easily from the outside in a 1½" socket and switched reliably and quickly with an integrated polished vibrating probe.
Vibrant measurement solutions support grain-processing processes
A large plant operator in the bakery industry located near Moscow was looking for several reliable measuring concepts for flour and grain silos. Since there are areas, especially in mills, where there are explosion hazards due to grain and flour dusts, certified component technology is indispensable there. In addition, the parts of the measuring sensors used that come into contact with the product must be food-compliant or EHEDG certified. After relevant research by the UWT engineers on site, suitable solutions could be provided with the vibration fork versions of the Vibranivo® collection.
The vibration fork was particularly well suited for the applications due to its wide range of individually designable models as well as its high durability. The certified design qualified it for use in dust explosion hazardous environments, as the Vibranivo® models are also available in intrinsically safe, dust explosion proof and flameproof versions. Due to the different versions as well as the modular design within the fork family, a number of different process applications of the grain plant including specific challenges in each case could be successfully handled with this measuring principle:
The vibrating fork VN 1020 from the Vibranivo® 1000 series with a short extension was used to implement an empty signal in flour pre-hoppers to loading telescopes. Special attention had to be paid to the strong static charge of the plastic containers during filling. To ensure trouble-free production and smooth loading of the flour types into the trucks, the fork was therefore designed with a more robust construction and specially protected electronics. In principle, the short design of the VN 1020 allows optimal use in containers with limited space, for example also in the loading telescope as a full detector or in downpipes as a backflow detector.
For the intermediate containers of the plant, which were filled with grain, the VN 4030 of the economical Vibranivo® 4000 series was used as a limit switch for reliable full detection. The vibrating fork was installed as a particularly robust model with a tube extension, so that it switched with high precision to stop the filling of the intermediate hopper in time. The model could be installed vertically with optional height adjustment. The sensor detected accurate fill levels even at high pressures of up to 16bar. In order to detect exact fill levels in the intermediate containers and mixing plants for flour, the plant operator also installed vibrating forks of the VN 4020 model as full and empty detectors. Since the application involved very small containers, a special requirement was the frequency of the required switching operations. By using the vibrating fork, horizontal, vertical and inclined installation was possible. This meant that even limited spaces were no problem and accordingly reliable and high-frequency limit switching could be realized.
A suitable complement to the vibrating fork - the compact vibrating rod
In a wide variety of process applications around the world, solutions have been in demand more frequently in the field of measurement technology in recent years, which can be implemented quickly and easily worldwide thanks to common device characteristics. The focus is on a high degree of compatibility for different vessel and process conditions, which results in more flexibility for users. Accordingly, UWT GmbH expanded its product family with the
vibrating rod, which is a single-rod probe with a very compact design. It has the same measuring principle as the vibrating fork. It vibrates piezoelectrically excited at a mechanical resonance frequency. If the probe is covered by the material, the resulting damping is registered electronically and a corresponding switching output is activated.
The vibrating probe is another uncomplicated solution for level detection among the vibration principles and thus the ideal complement to the vibrating fork Vibranivo®. These detectors from the vibration family can be used in various material processing operations.
The rod detector has small connection threads from 1" and is ideally suited as a full, demand or empty detector in silos and tanks with limited space. In particular, it can be used as a backflow detector in pipes and shafts. Due to the high surface quality of the probe, a wide range of applications can be implemented without any problems, even with materials that tend to stick.
Due to the 4-stage adjustable sensitivity, very light, powdery bulk materials from 20 g/l are reliably detected, even those with a tendency to bridge. At the same time, the robust construction enables measurement in coarse-grained granulates. Regardless of the industry, the device can be used to detect plastics, foodstuffs as well as building materials, chemical materials, etc. for process temperatures up to 150°C. In addition, MN 4000 models also represent very economically feasible solutions.
Clever new measuring technology that fits in everywhere
Even in its standard version, the new Mononivo® vibrating rod is highly compatible with the most common applications worldwide. It is robust, easy to put into operation without calibration and can already be configured precisely and without great effort to the application during sensor selection through the various device series. For example, the rod probe is available with different flanges as well as variable boom lengths with tube extensions.
By equipping the vibrating rod with the device attributes commonly used worldwide, it can be integrated particularly smoothly into the project planning concept for the measurement technology equipment of a plant. KIT solutions with application-related product design are easy to implement, which means individually quickly adaptable device designs and a high degree of flexibility for plant operators. All Mononivo® models have a modular design, which enables short delivery times.
By adding the popular vibrating rod to the solution portfolio, it will be possible to implement further smart project planning for level measurement technology in plants in the future.