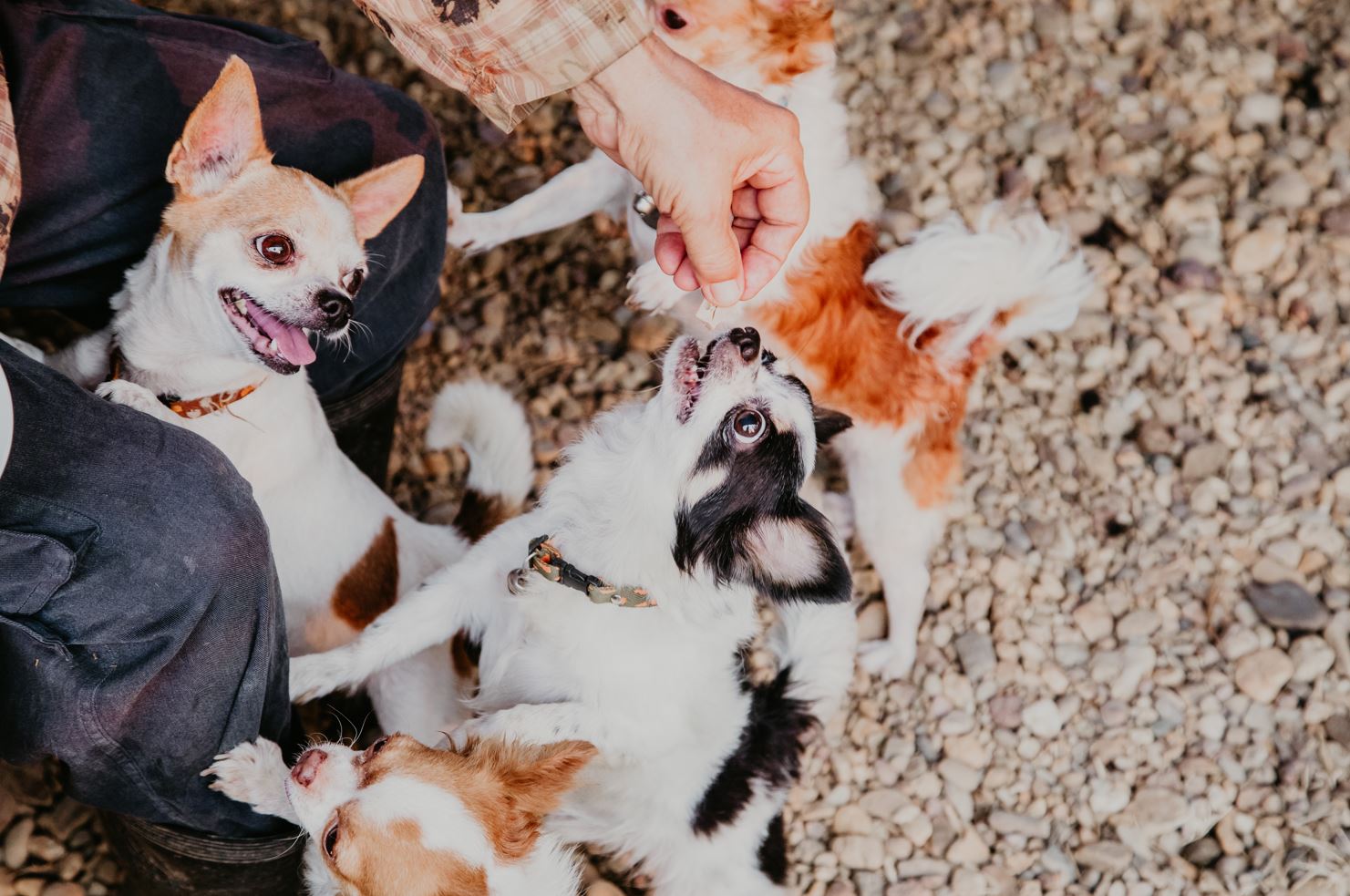
Animal Feed
The process and storage environments within the feed industry often have factors such as moisture, vapor and fat to consider which cause the materials to have caking tendencies. Devices with special coatings and technologies provide the operator with appropriate and economical solutions.
-
-
Level measurement with guided wave radar in the boiler
-
Free-radiating radar measurement in animal feed production
-
Media detection in raw materials
-
From classic to innovative - the right thing for everyone
-
Overfill protection in fish oil
-
Efficient silo management for smooth process flow
-
Different processes within bulk material handling for animal feed production
Categories
Application Stories
Application Stories
[73]
Case Studies Medium
Case Studies Measuring Task
Product Highlights
Product Highlights
[16]
Level Measurement Explained
Level Measurement Explained
[11]
How-to
How-to
[15]
UWT Behind The Scenes
Recent Posts
Tags
meet us
discover
projects
products live
overfill protection
inside uwt
silo/tank management
dry run protection
food compliant
min/max detector
chemical resistance
ex approvals
caking material
ehedg
contact-free
high temperature
manual
instructions
abrasive material
mechanical load
pps/pvdf
universal voltage
liquids
coax
active shield
sil
hygiene
whg
io-link
high pressure
master class
webinar
podcast
visualization
foam
uwt cares
boiler approval
remote
pfa/ceramic
touchpanel
Archive