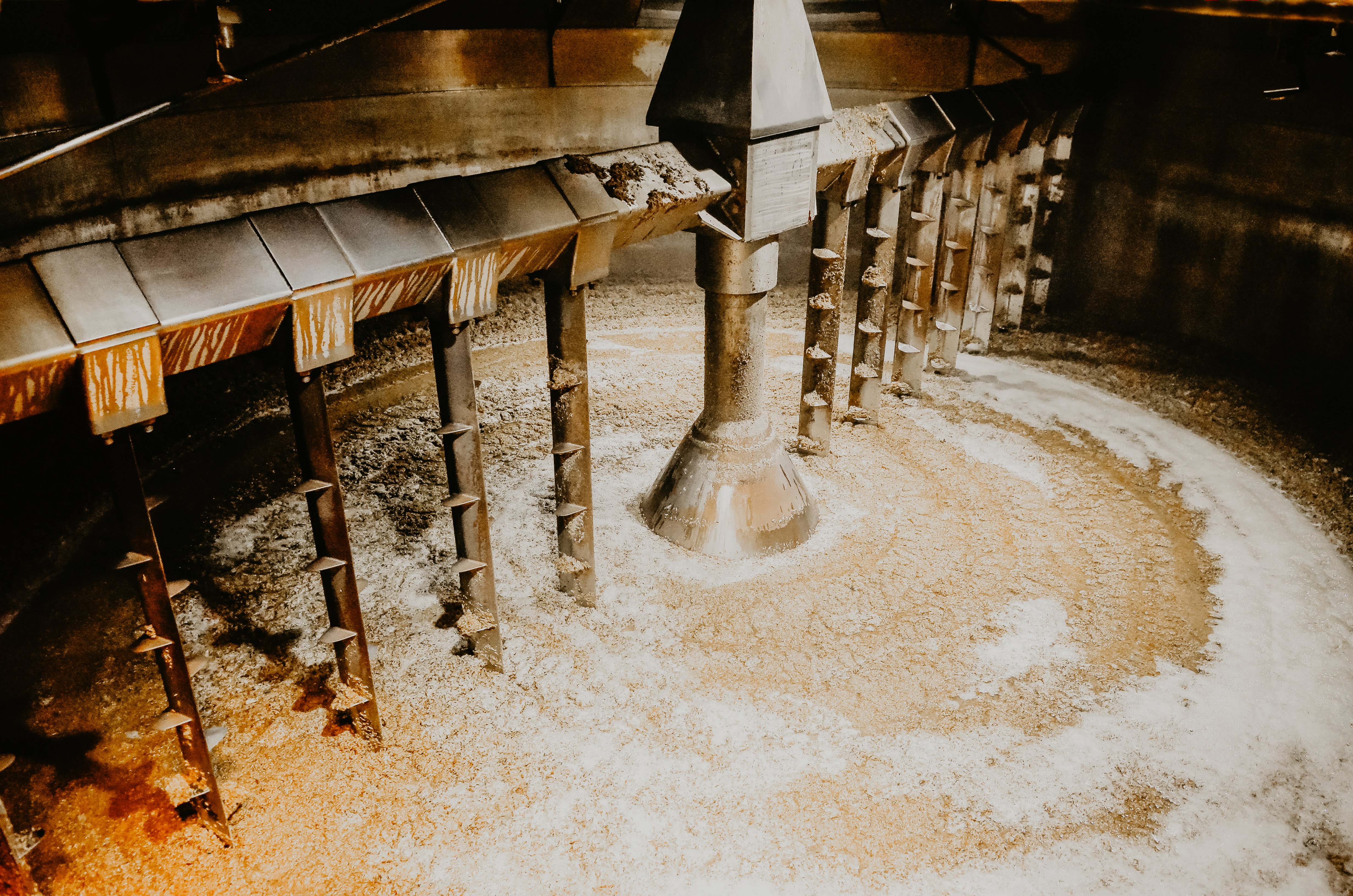
Food & Beverage
Within the food industry, absolute hygiene is essential. Food compliant sensors could be the key ingredients to meet the requirements for the secure measuring of bulk solids and liquids. There are process conditions like moving surfaces, CIP or changing DK values and viscosity.
-
-
Level Measurement Technology for the Food & Beverage Industry
-
Stable filling processes in food production – with Vibranivo® as a demand-level switch
-
Reliable Point Level Detection for Coffee Filling
-
Robust in nitric acid, reliable in the CIP cleaning process
-
Explosion protection in grain storage: Level measurement & monitoring
-
Capacitive level sensor meets highest EHEDG hygiene standards
-
Rotary paddle level switch for reliable production process in peanut butter production
-
EHEDG certification for rotary paddle level switch
-
Vibration probe provides reliable monitoring of limit level in tea production
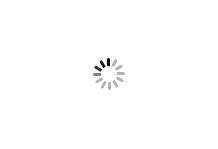
Categories
Application Stories
Application Stories
[73]
Case Studies Medium
Case Studies Measuring Task
Product Highlights
Product Highlights
[16]
Level Measurement Explained
Level Measurement Explained
[11]
How-to
How-to
[15]
UWT Behind The Scenes
Recent Posts
Tags
meet us
discover
projects
products live
overfill protection
inside uwt
silo/tank management
dry run protection
food compliant
min/max detector
chemical resistance
ex approvals
caking material
contact-free
ehedg
abrasive material
manual
high temperature
instructions
mechanical load
pps/pvdf
liquids
universal voltage
coax
active shield
sil
whg
hygiene
io-link
high pressure
podcast
webinar
master class
visualization
boiler approval
foam
uwt cares
remote
high sensitivity
pfa/ceramic
Archive