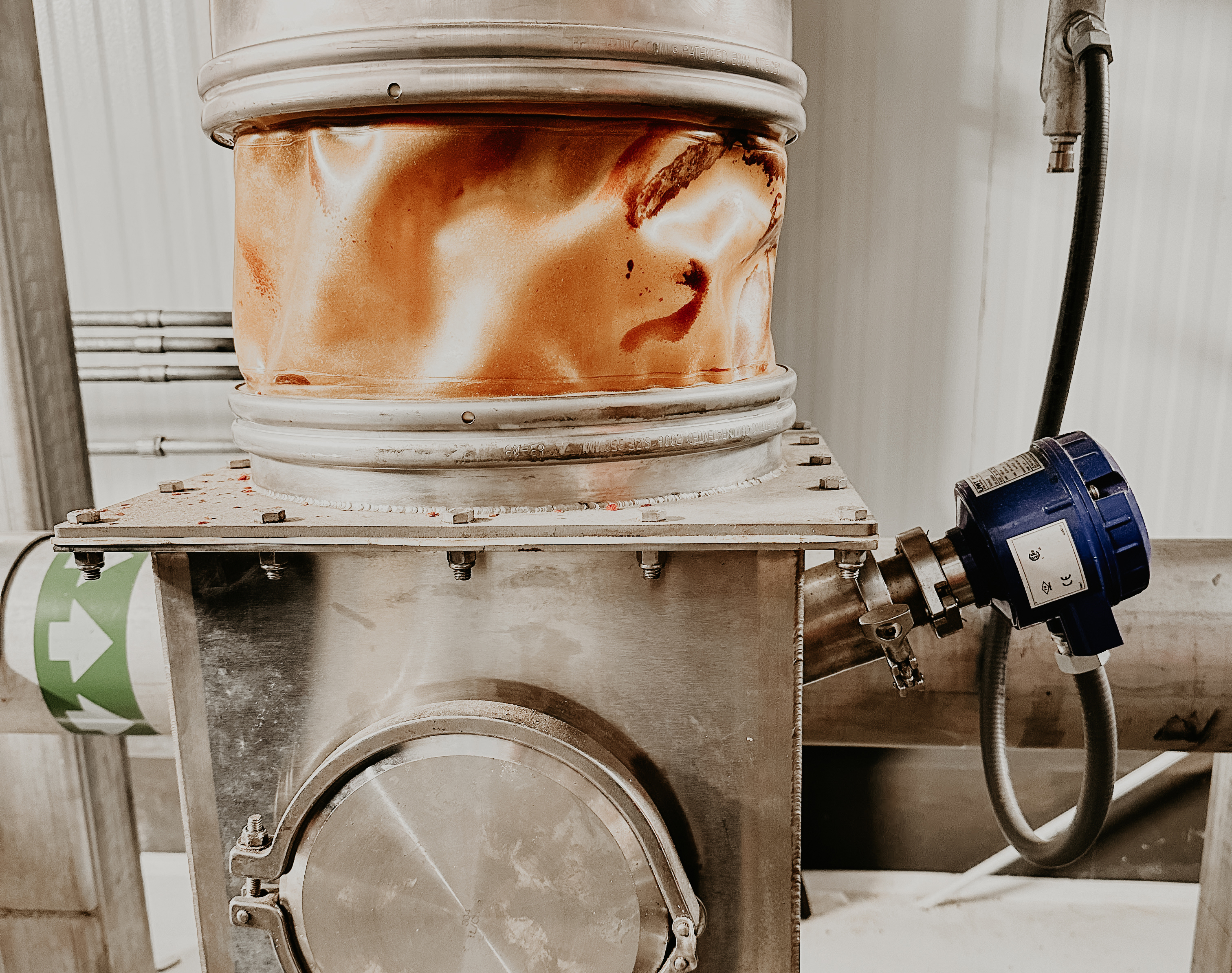
Optimum operating efficiency with the Rotonivo® rotary vane sensor
One of the world's largest peanut butter companies, with a production plant in Kentucky, was having issues with their level measurement sensors installed in the production area of their plant. To solve the problem, the Rotonivo® rotary paddle sensor was introduced, which significantly improved operational efficiency and reduced plant downtime. Once again, UWT has demonstrated its experience and commitment to providing innovative solutions to the industry.
Rotonivo® eliminates frequent sensor failures
and reduces downtime and costs
At their production plant in Kentucky, the peanut butter manufacturer had been dealing with constant problems with their measurement sensors. The rotary paddle sensors by another brand that they had previously installed had a very short life span, often failing within a day.
The Challenge: Eliminating frequent sensor failures and high levels of downtime
The main problem that was causing the sensor to break down was salt and sugar build-up around the probe shaft, which the motor was unable to remove. At the same time, these materials were getting into the seals and bearings, causing the paddles to stop rotating. All of these sensor failures were causing extensive downtime and high replacement costs, which significantly affected the plant's production capability.
In order to resolve the frequent production disruptions, the operator requested assistance from the UWT Level Control LLC team based in the USA and led by David Spratlin, Managing Director, to replace the sensors.
In response, UWT offered the Rotonivo® - 6004. The rotary paddle sensor with a reinforced shaft and double stainless-steel bearings ensures high durability when in contact with dense materials. Additionally, the double stainless-steel bearings prevent materials such as salt and sugar from wearing out the sensor seals and entering the electronics. This had been a common problem with the previously used sensors, which had led to their failure.
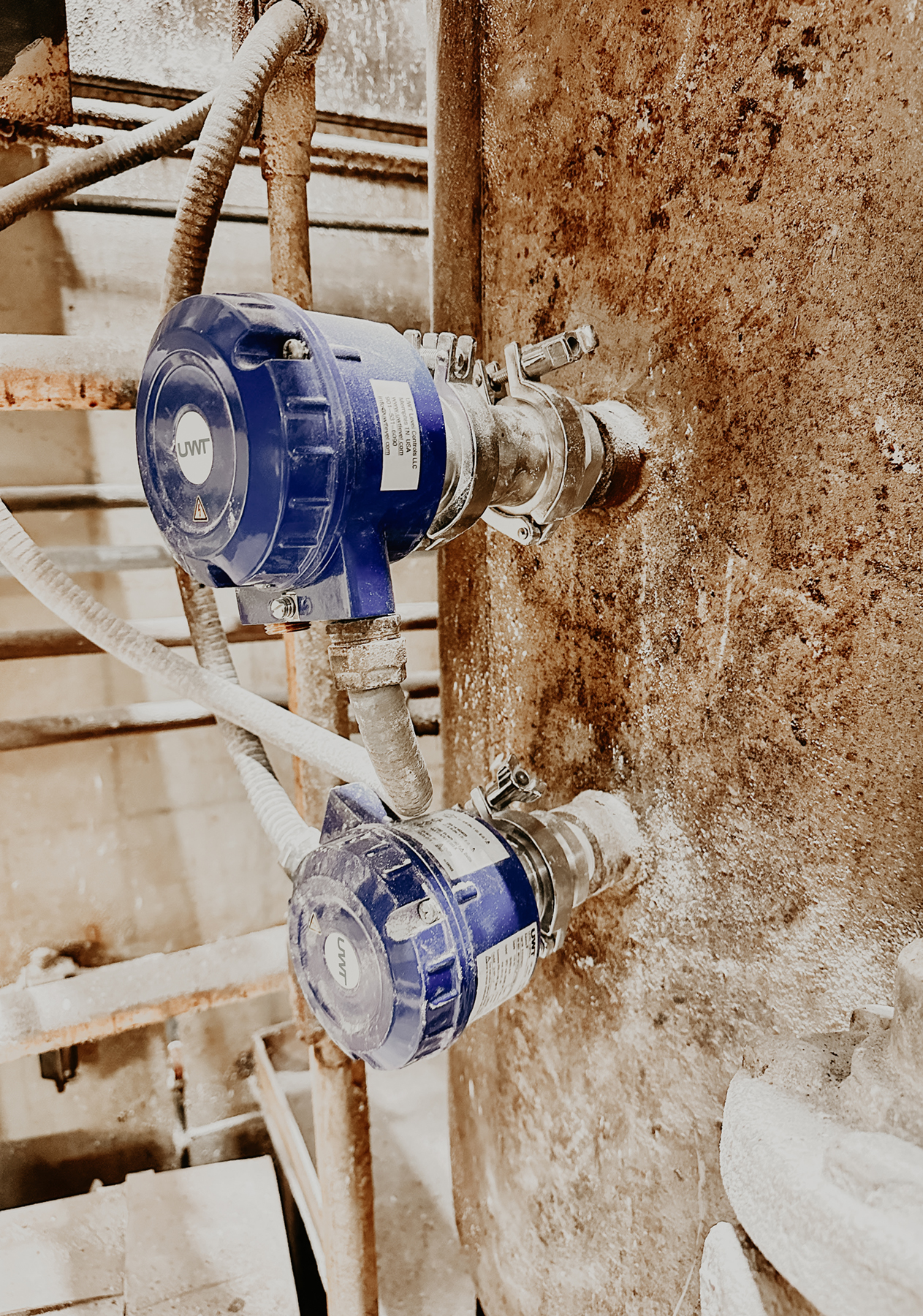
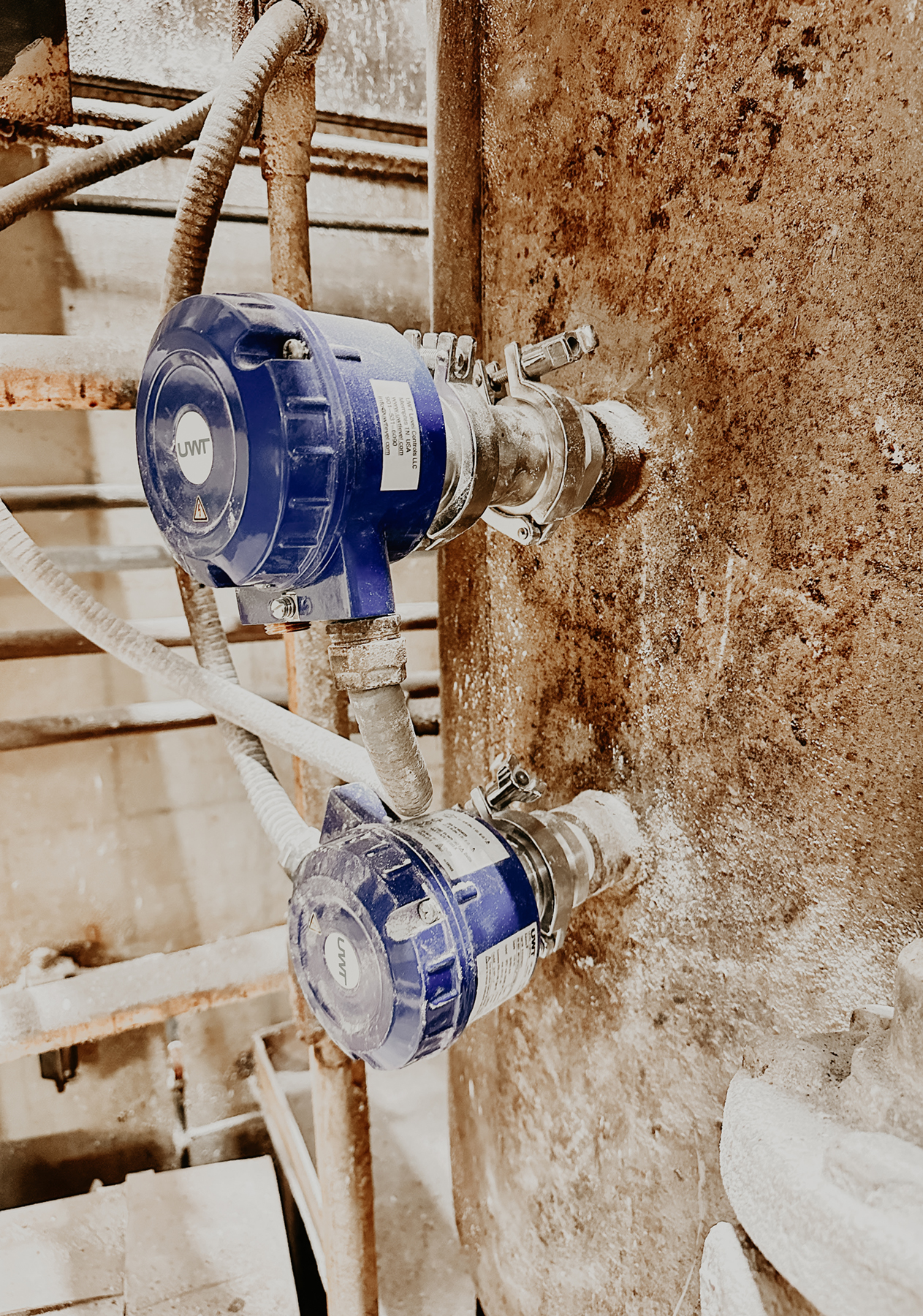
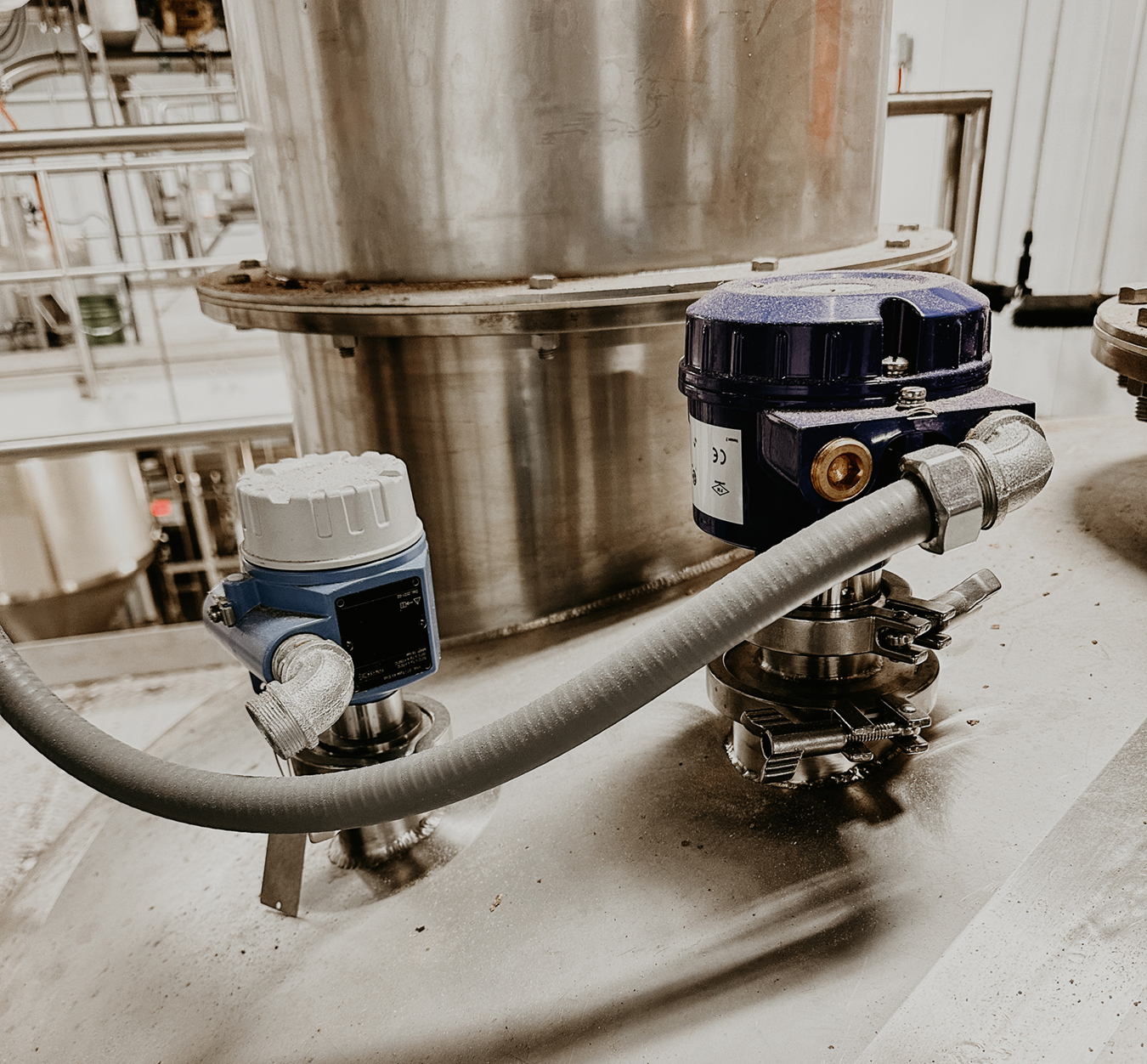
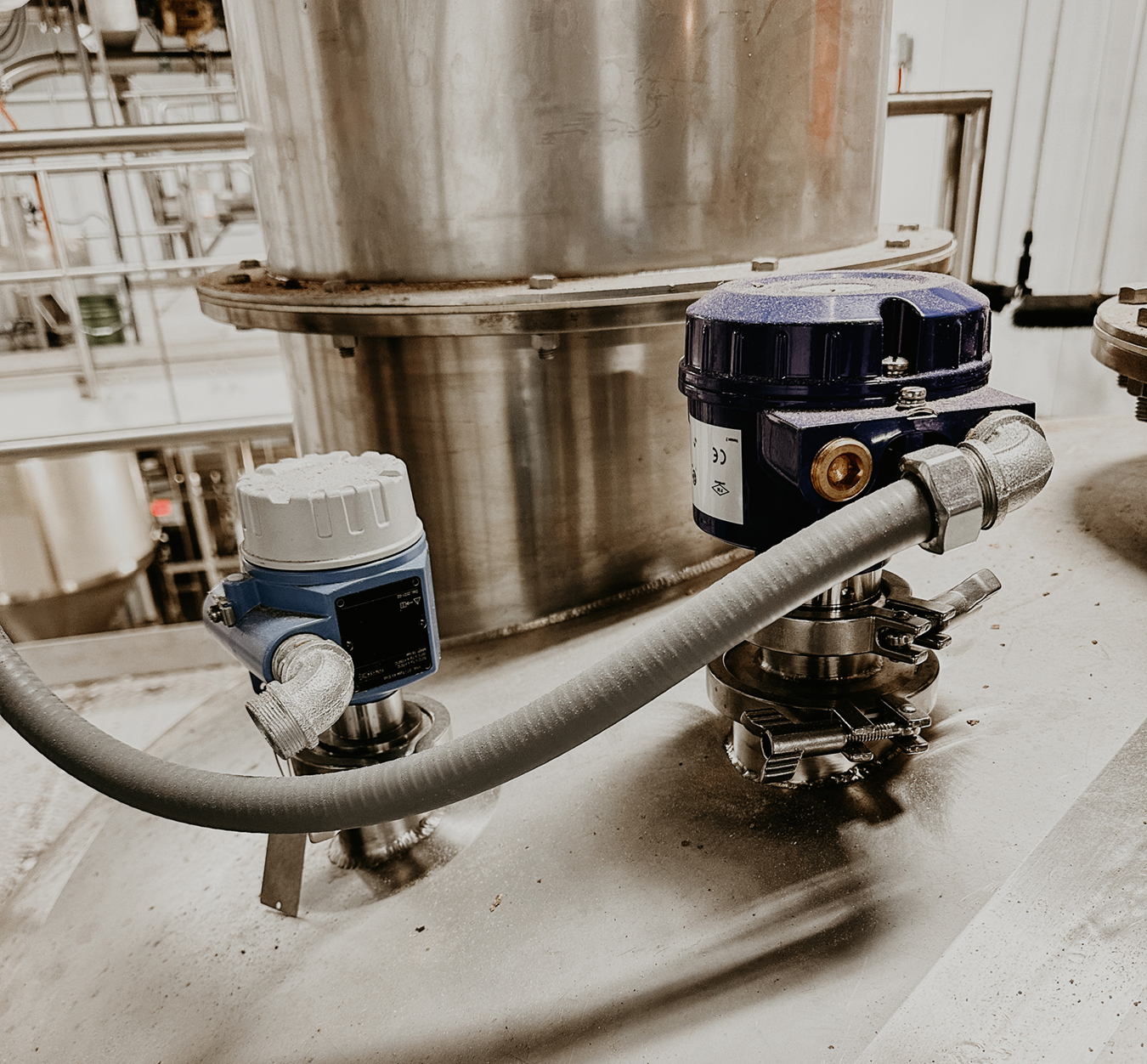
A Success Story: A Year Of Continuous Operation
The rotating paddle sensor from the UWT
was installed in the plant more than a year ago, and since then has demonstrated no failures.This is a significant improvement over the previous sensors from another brand, which required frequent repairs, resulting in time-consuming and costly maintenance. The successful implementation of the RN 6004 at the Lexington peanut butter plant underscores UWT’s commitment to providing reliable solutions tailored to customer needs, consistently exceeding expectations through innovation.
Discover more applications in the food industry
Whether in the processing of fruits, vegetables, nuts, flour, sugar, milk powder, spices or other food industry products – UWT offers reliable sensor solutions for a wide range of processes along the entire food and beverage value chain.
You can find all solutions at a glance in our industry brochure:
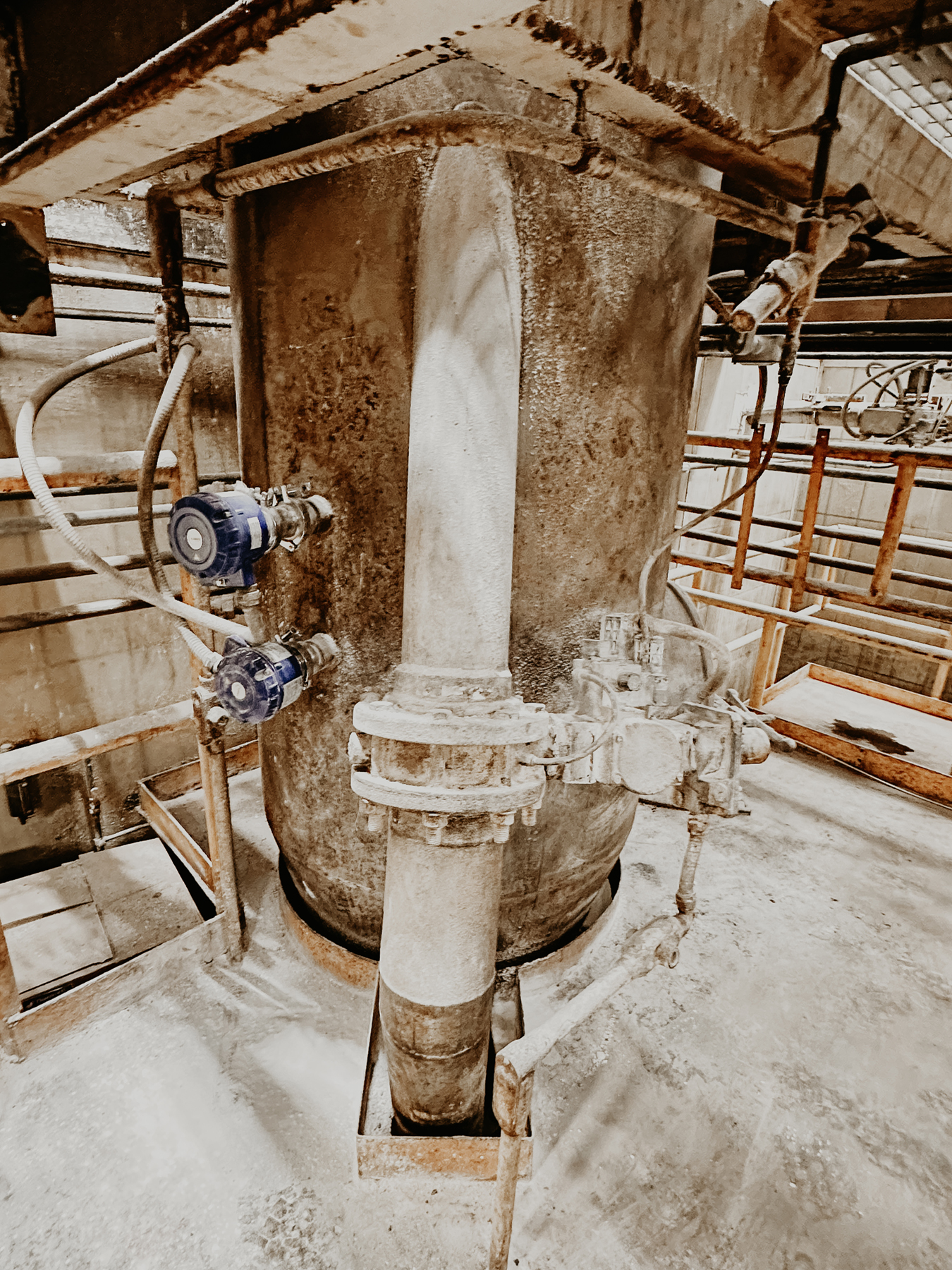
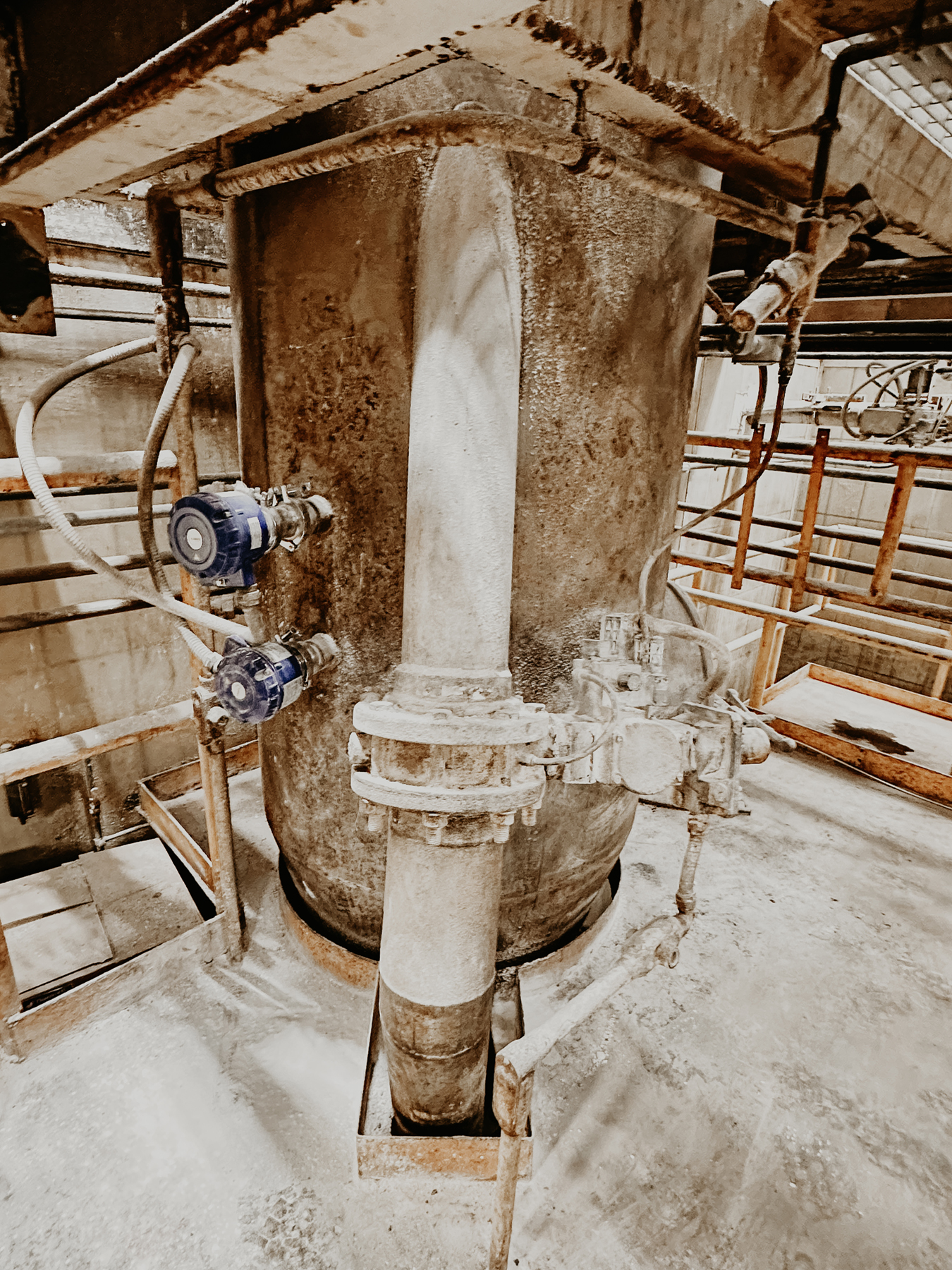
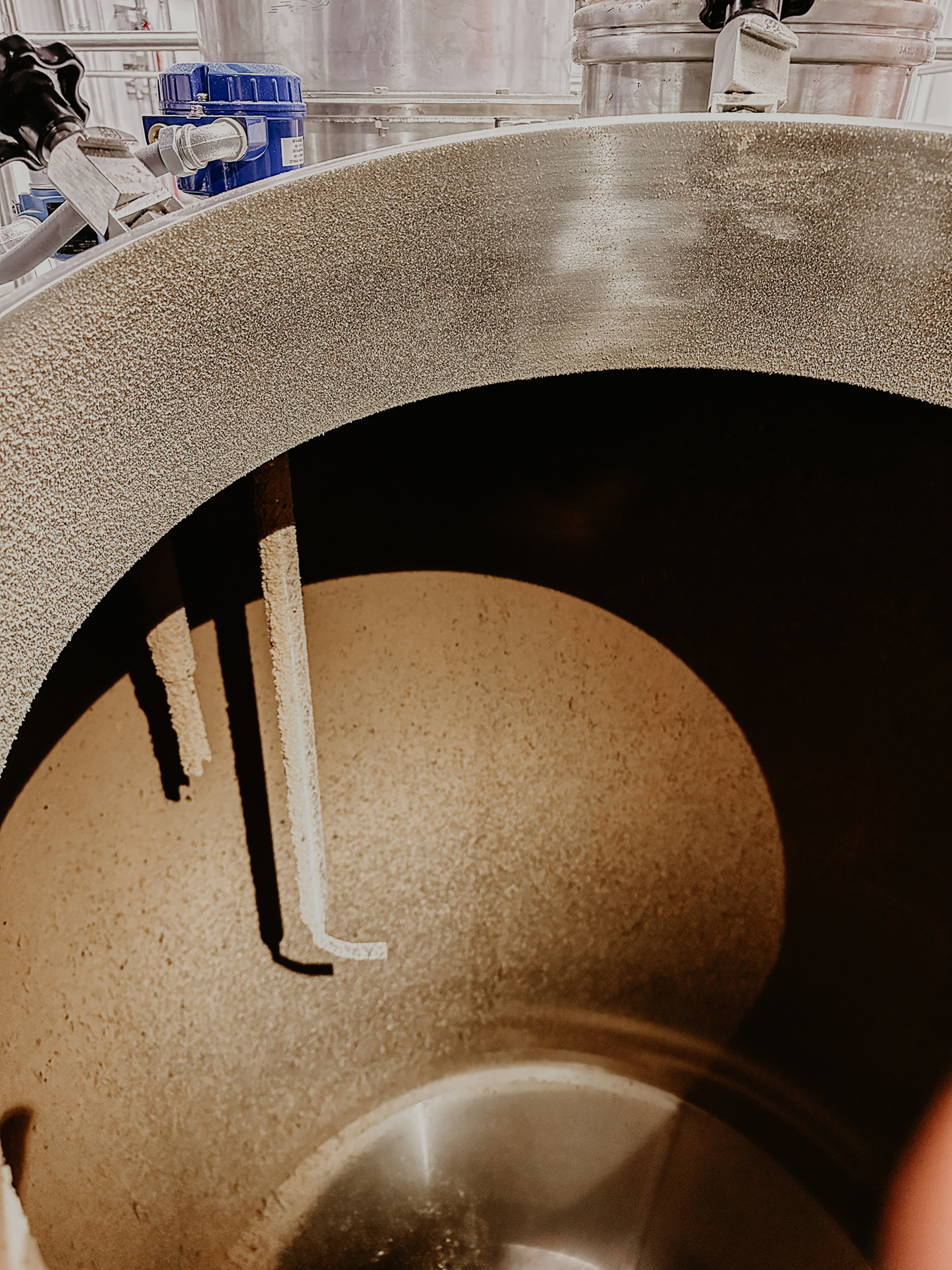
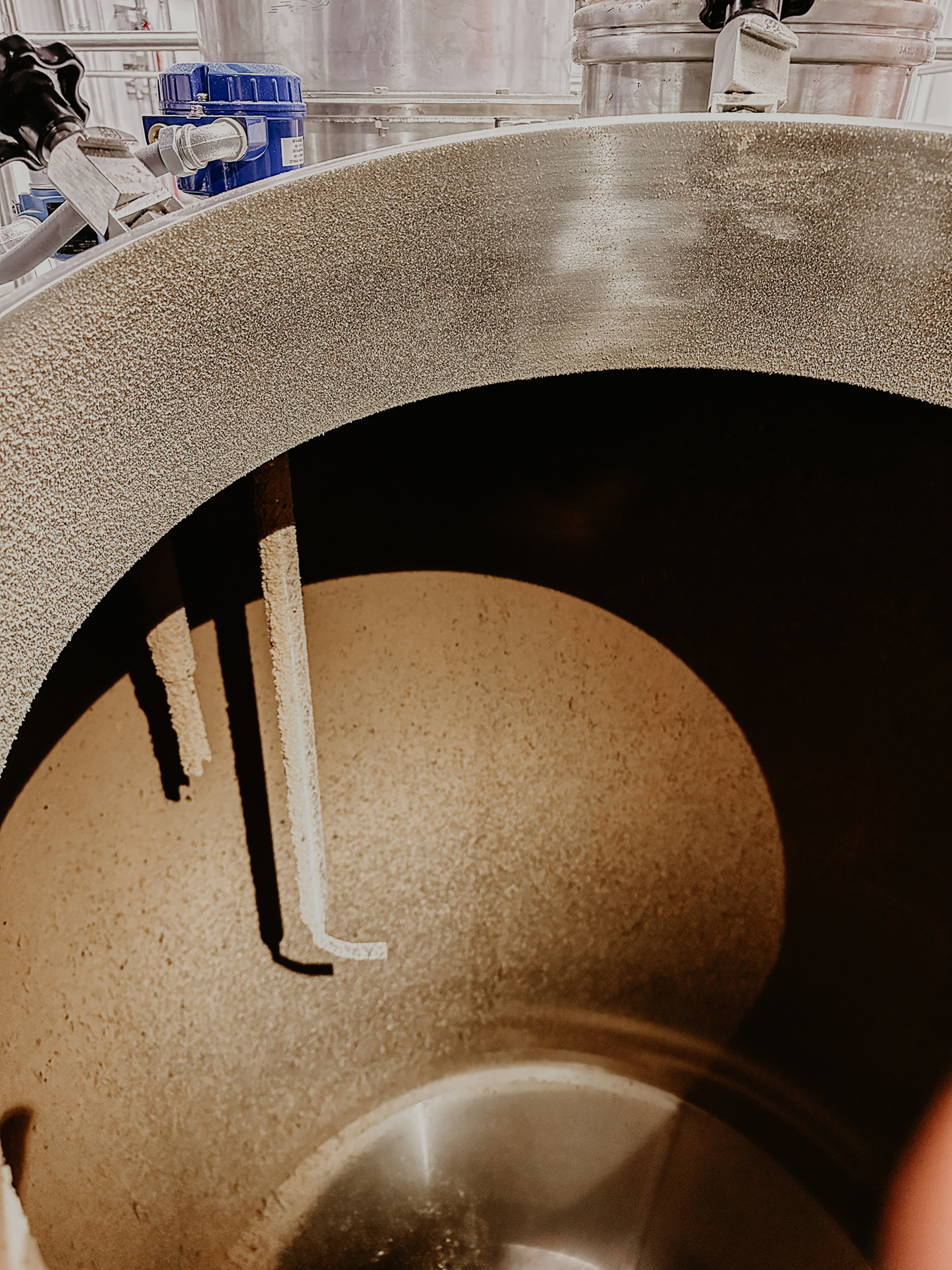
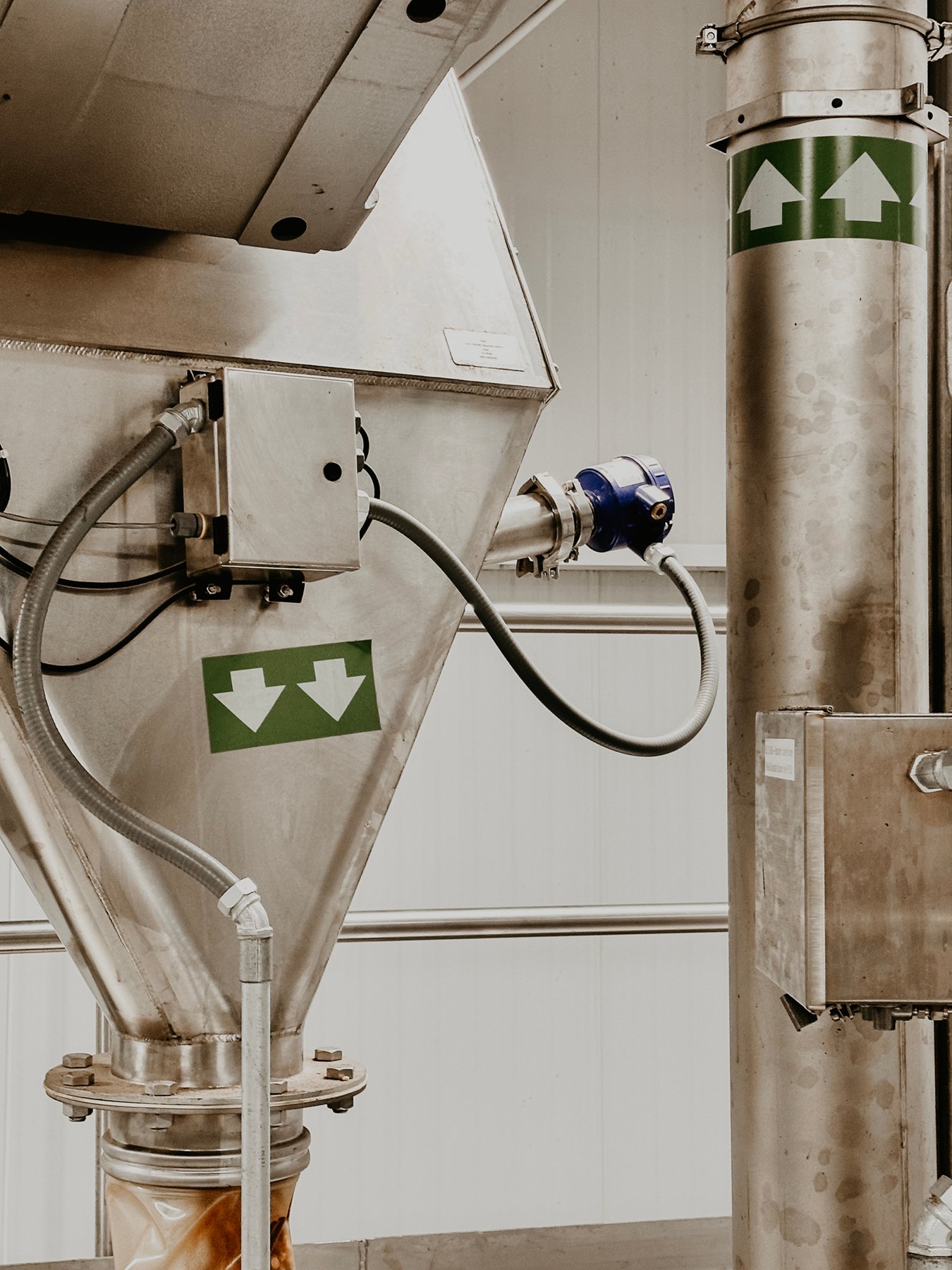
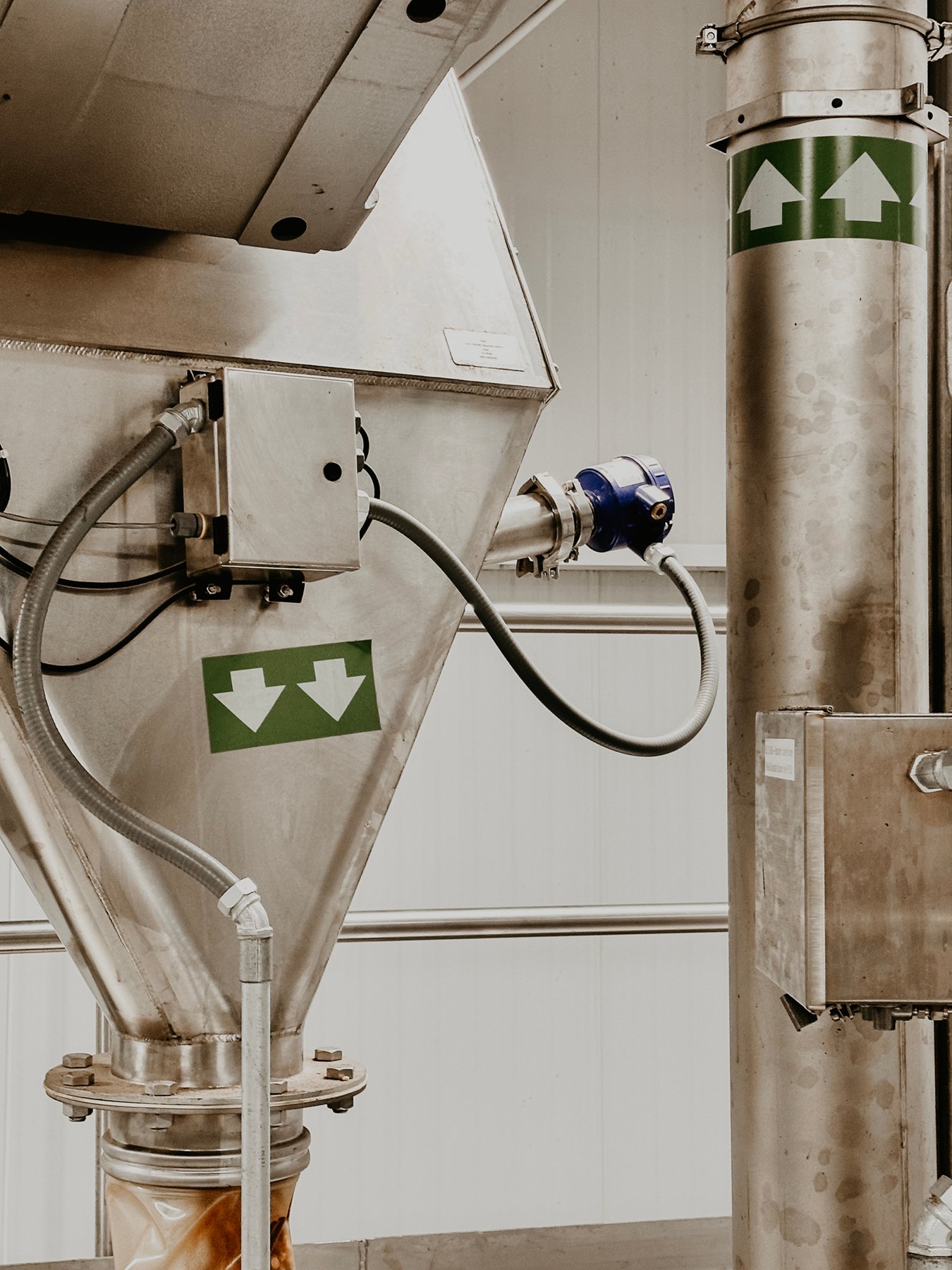
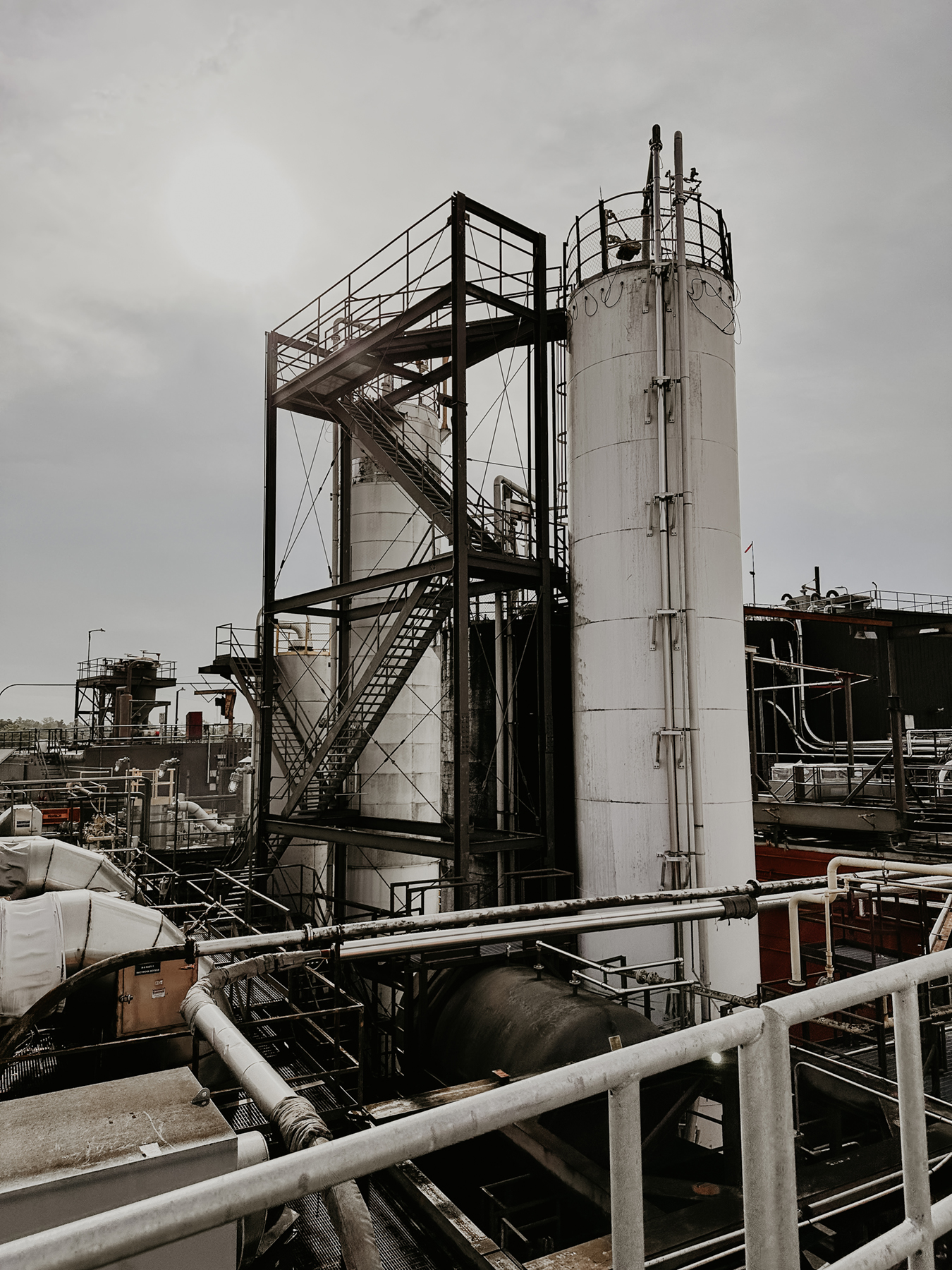
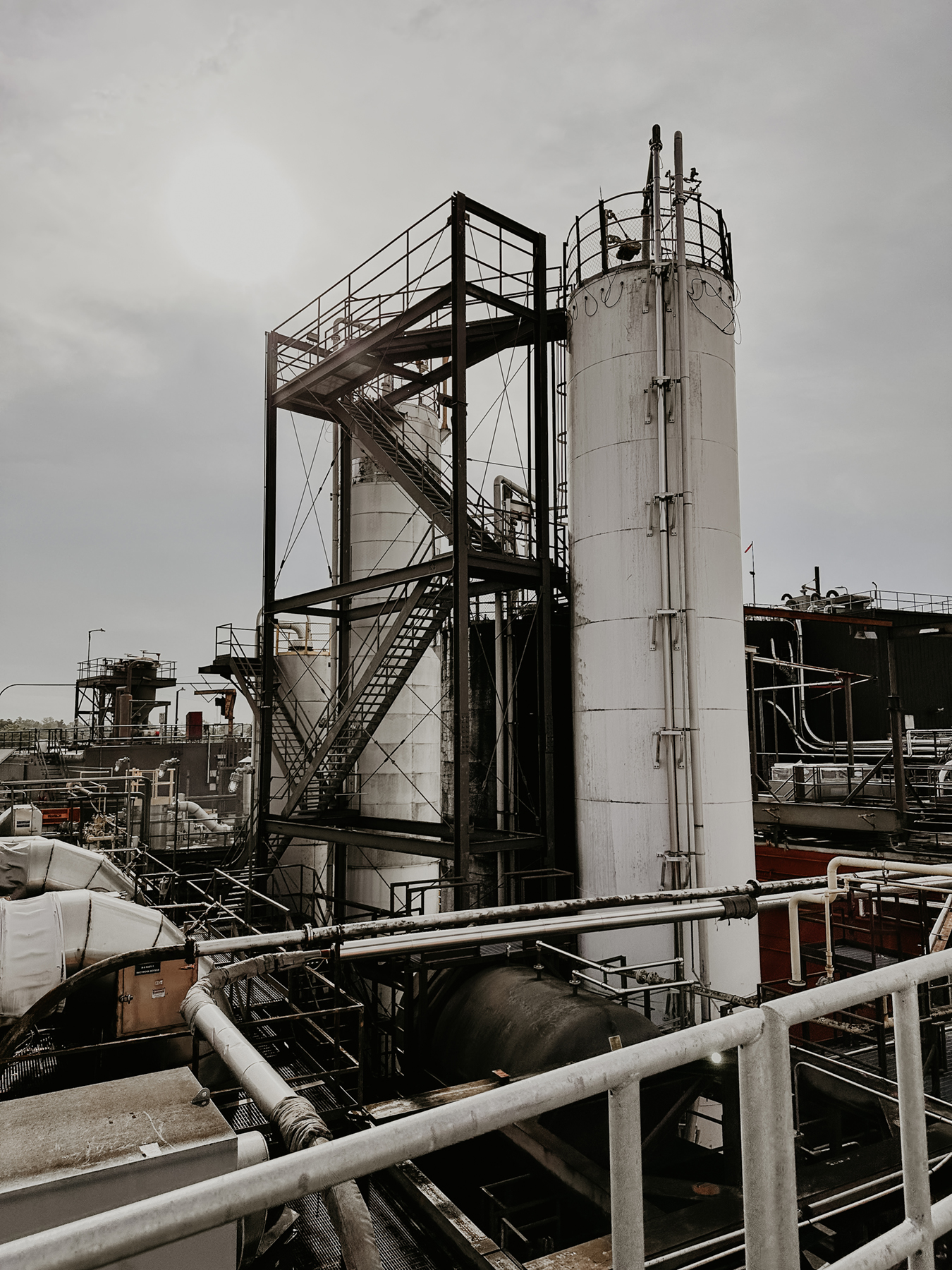
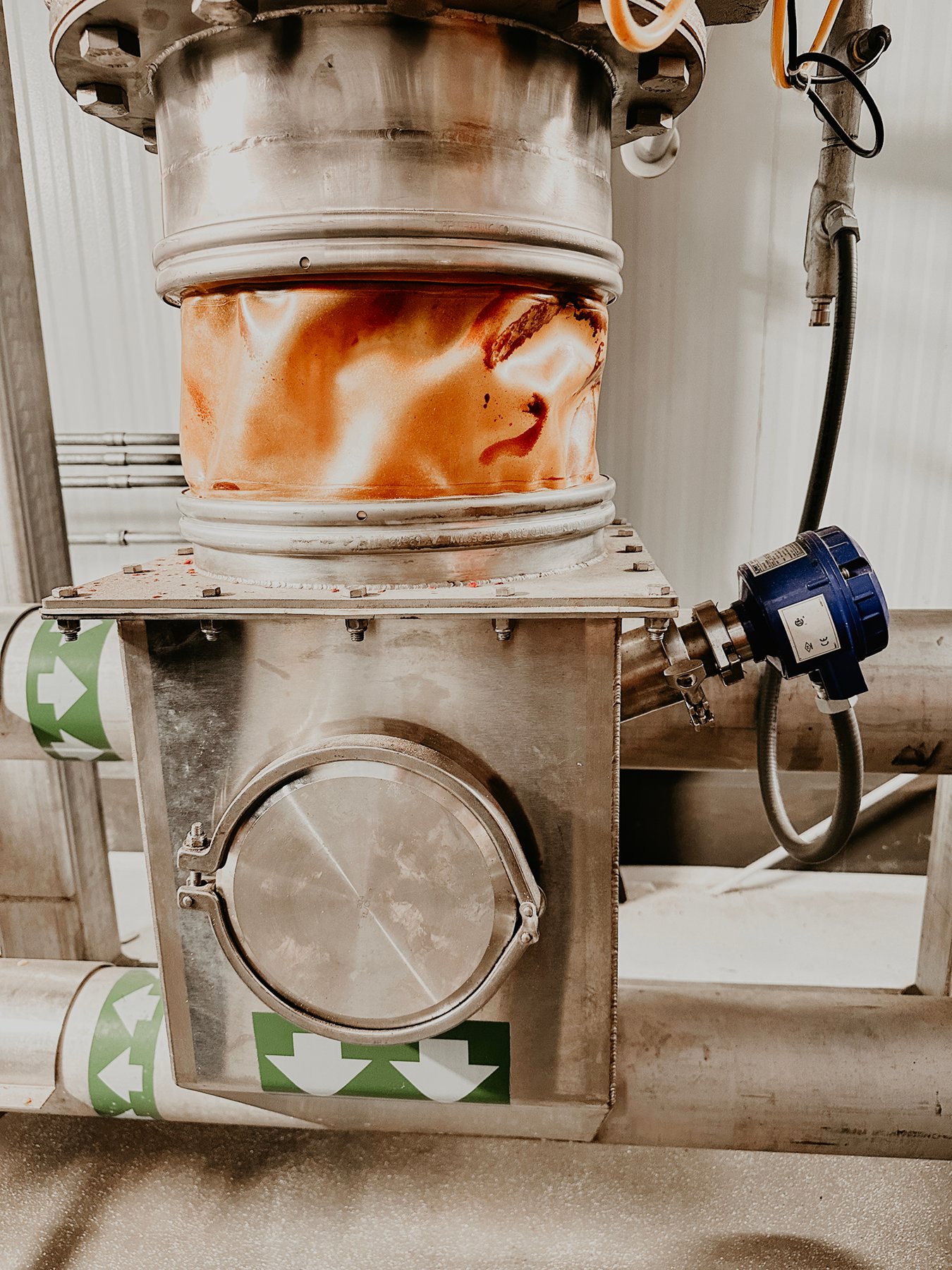
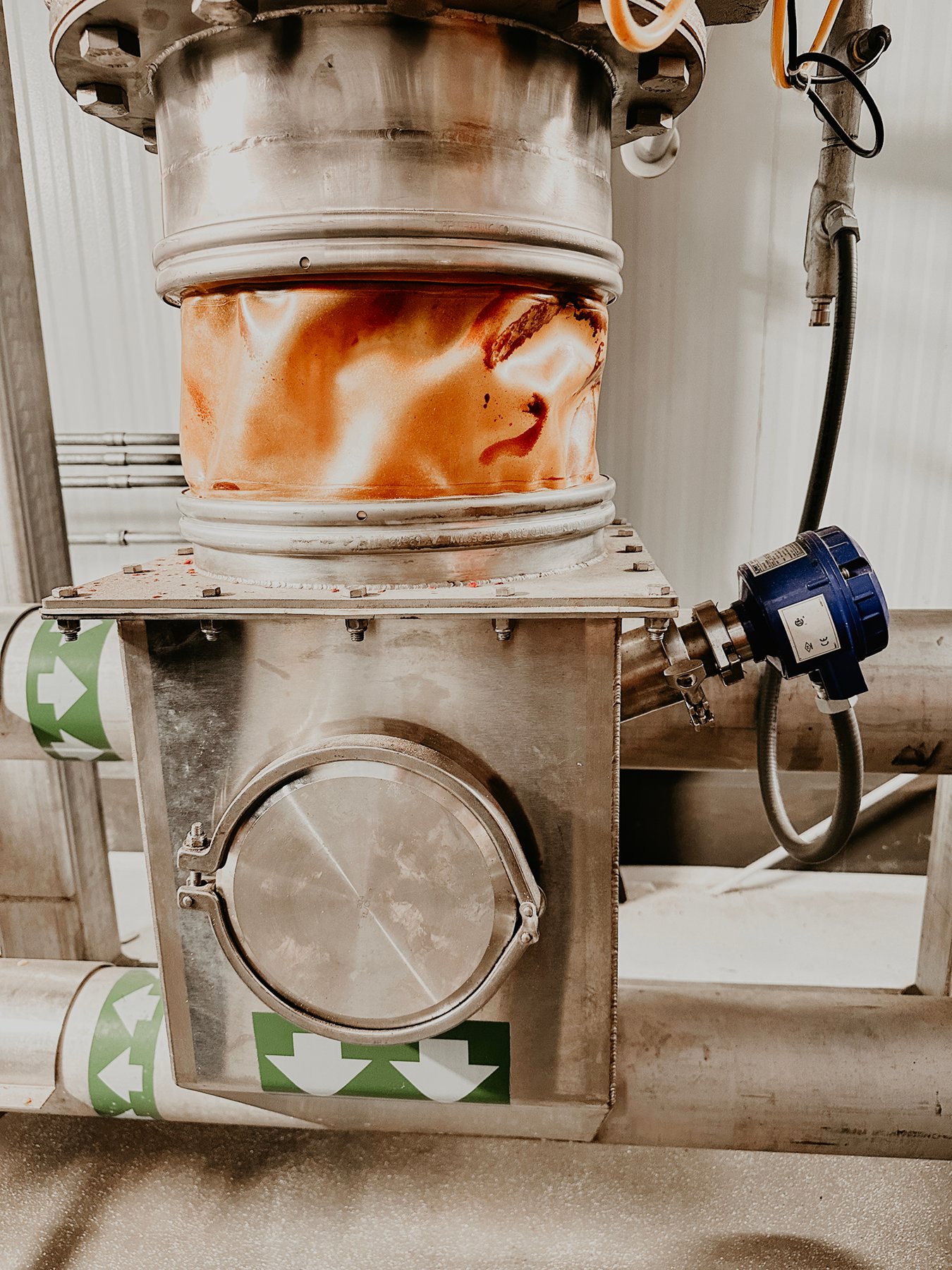
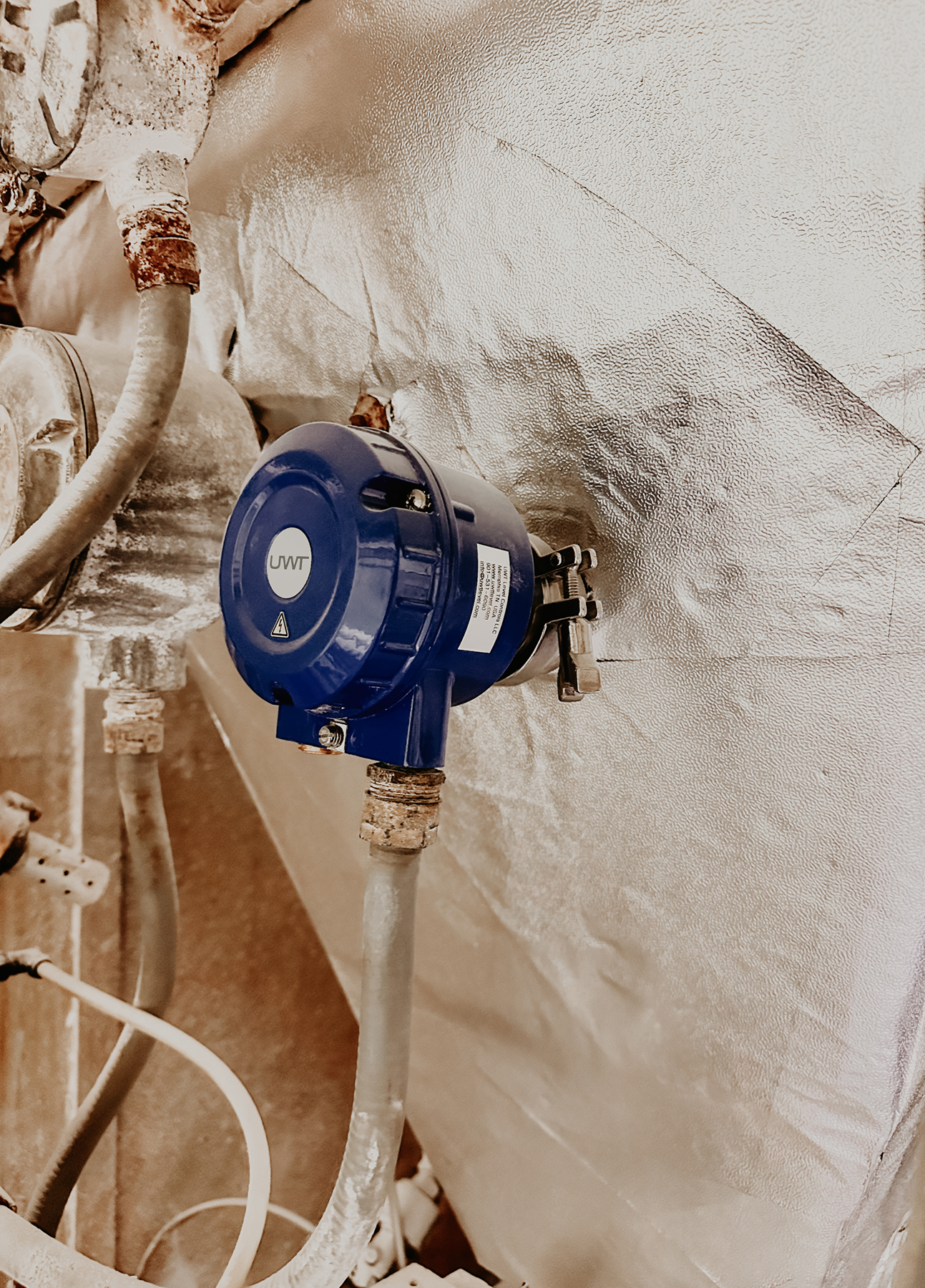
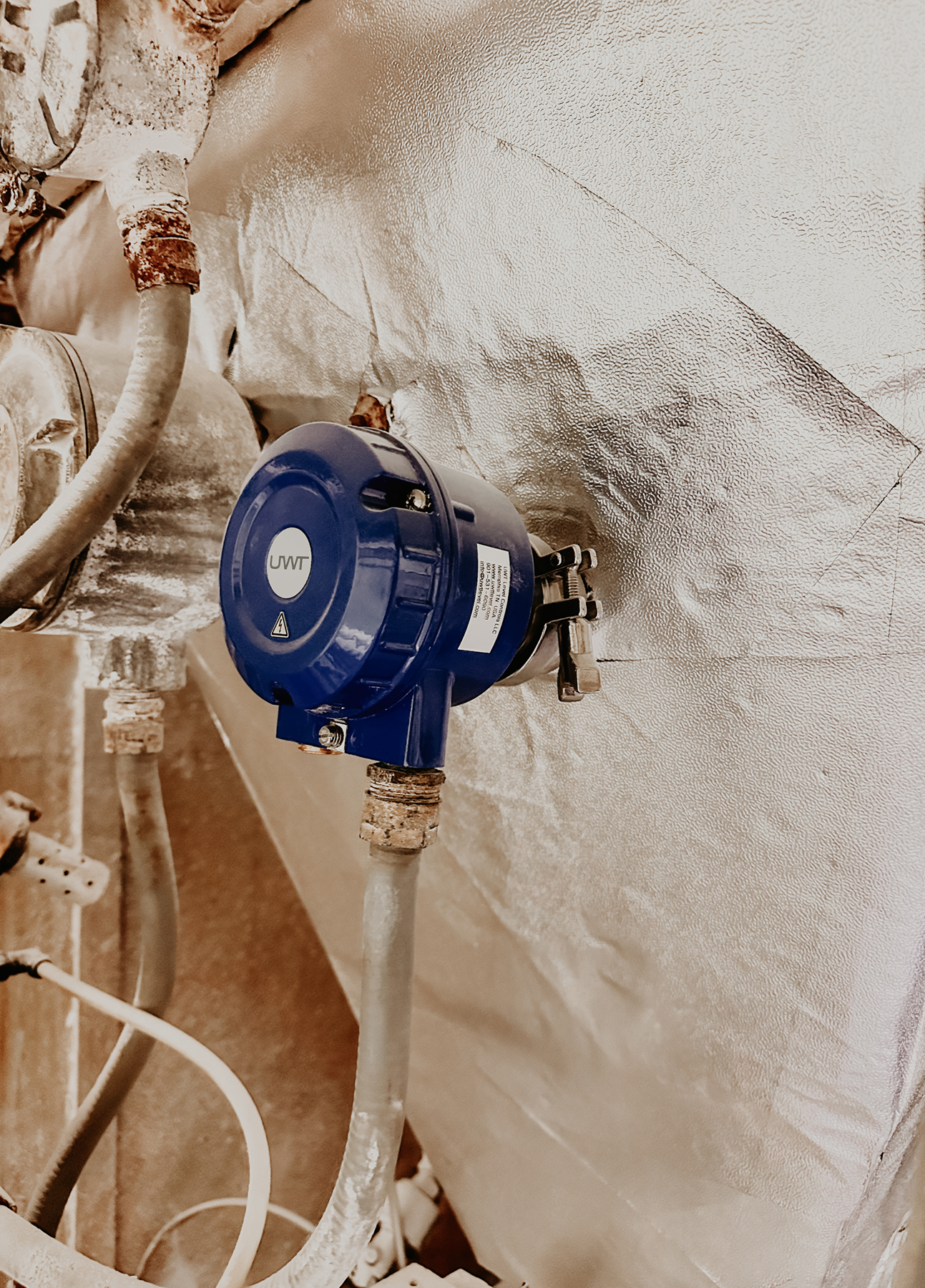