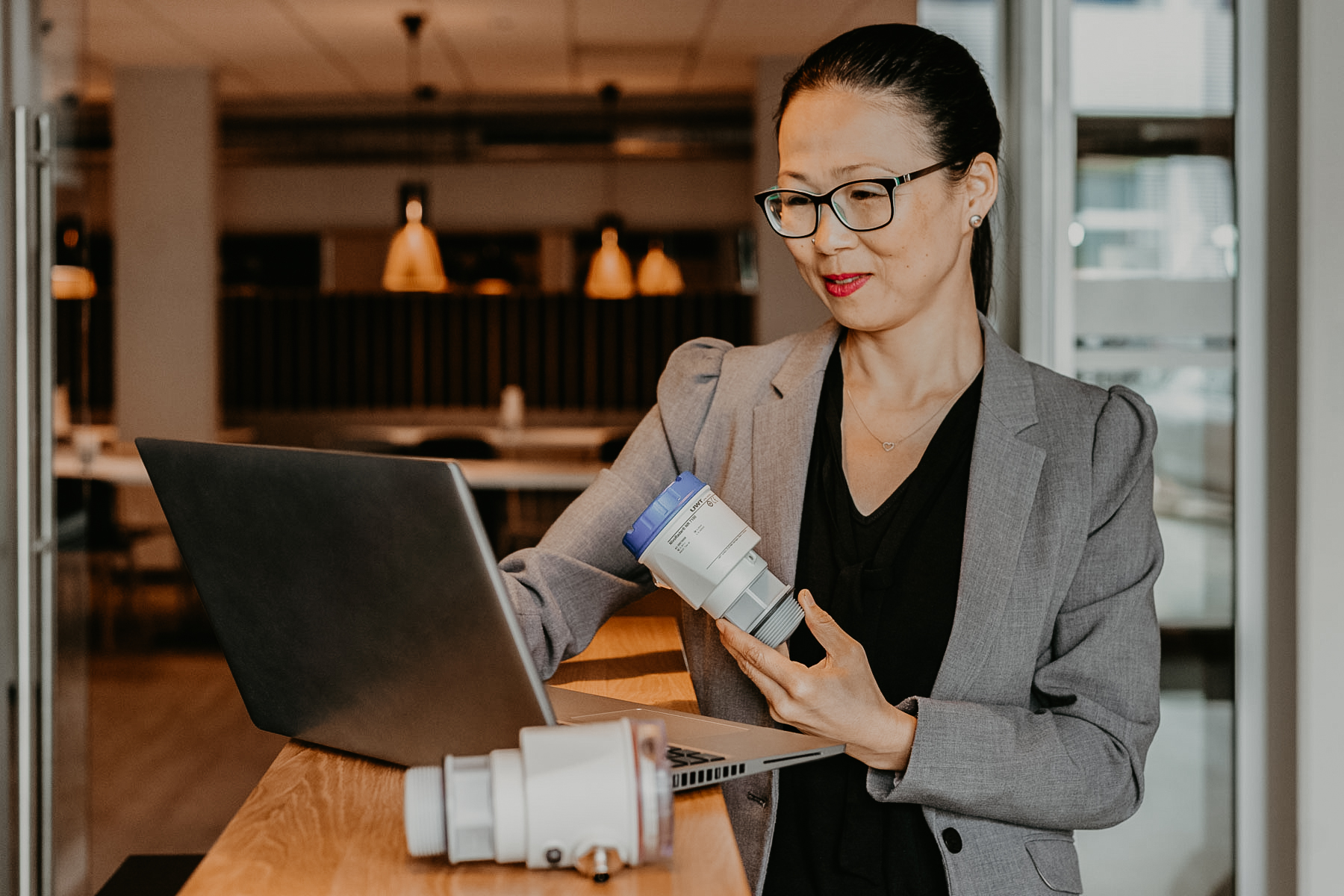
Continuous level measurement overview
Continuous level measurement refers to a method for continuously monitoring the level of a medium in a container or industrial plant. The level of the medium, whether liquid or solid, is measured in real time and updated at regular intervals. In contrast to Point level measurement, which is used to recognise specific conditions or threshold values and trigger actions when these are reached, continuous level measurement is used to precisely monitor the level during operation. This is also used during interface measurement. The continuous level measurement can easily be equipped with level monitoring and visualisation, to provide additional safety and control.
Measuring method for continuous level measurement
There are various methods for continuous level measurement that can be used depending on the requirements and properties of the medium and the container. UWT's repertoire includes the following measuring principles:
Electromechanical level measurement with lot sensors
Electromechanical level measurement is based on the principle of mechanical movement or deformation of an element that is influenced by the level of the medium. A mechanical device is used to detect the level and convert it into an electrical signal. The electrical signal can then be further processed to display the level or transmit it to a control or monitoring system. The signal is often scaled to a corresponding measuring range using a voltage divider circuit.
Level measurement with an electromechanical plumb bob sensor is based on the principle of sounding. This involves inserting a flexible cable or a strap extension with a sensing weight at the end into the container or tank. This can be a float switch, a parachute or a claw, for example. The plumb bob is lowered into the container until it reaches the bottom or the surface of the liquid. The level is determined by moving the sensing weight along the rope or tape.
Exemplary applications of electromechanical level measurement with lot sensors:
Disposition Stocks Plastic granulate
Everything in balance in cement production processes
Solutions for the storage of raw coal
Capacitive measurement
Capacitive level measurement is based on the change in electrical capacitance between electrodes in the container and the medium. The fill level can be determined by changing the capacitance. The sensor measures the electrical capacitance of the product, which is proportional to the fill level in the container. The integrated "Active Shield" technology guarantees high functional reliability even with products that tend to stick..
Exemplary applications of capacitive level measurement:
Level measurement of acetone with melted rosemary
Capacitive level measurement in tanks for gas cooling
With the right level of security
Level measurement with contactless radar
Radar-based level measurement uses electromagnetic waves to detect the fill level. A radar sensor emits high-frequency electromagnetic pulses and measures the time it takes to reach the medium and return. The fill level is calculated based on this transit time.
In non-contact radar level measurement, a radar sensor emits electromagnetic waves that propagate in the container. Some of the emitted waves are reflected by the surface of the medium and detected by the sensor.
The returned waves are analysed and the level is calculated based on the transit time and intensity of the reflected signals. As the speed of the electromagnetic waves is known, the transit time between sending and receiving the signal can be converted into a distance. This distance is then converted into the fill level of the container.
Non-contact radar level sensors can use different frequency ranges to cover different applications and measuring ranges:
- With the 78 GHz technology, a greater range and penetration capability is realised.
- The high-frequency 80 GHz radar sensors offer high accuracy and resolution:
- devices are suitable for bulk material applications thanks to their high degree of protection. They can also be installed outdoors on stockpiles.
- sensors are ideal for use in water treatment tanks and are also suitable for acids and alkalis due to their design. Measurement through the top of plastic tanks is also possible.
The advantages of non-contact radar level measurement lie in its ability to perform a precise measurement regardless of the properties of the medium (e.g. density, dielectric constant). It also works in adverse environments with high temperatures, pressures, vibrations or dust. Non-contact radar level measurement is suitable for various applications, including tanks, vessels, silos or storage tanks in various industries such as chemical, oil and gas, food and beverage, wastewater treatment and more.
Exemplary applications of contactless level measurement with radar:
Radar measurement under high process temperatures
Radar measurement in fruit juice production
Free-radiation radar measurement in animal feed production
Contact-free radar solution for water treatment slurry
Contactless radar sensors at the highest level
Level measurement with guided radar wave | TDR
High-frequency microwave pulses are coupled to a cable or rod and guided along the probe. The emitted pulse is reflected by the product surface. The time difference between the emitted and reflected pulse is converted into a fill level. Level measurement with TDR (Time-Domain Reflectometry) or guided radar wave therefore requires no direct contact with the medium. There is no need to interrupt or influence the filling process. By measuring the transit time of the electromagnetic signal, the fill level can be determined with high accuracy.
Guided radar sensors can be used in various applications:
- sensors are used for level measurement of bulk solids in silos or flow measurement in pipes.
- is ideal for monitoring liquid levels in tanks, storage facilities or containers.
Exemplary applications of level measurement with guided radar:
TDR solutions for challenging level measurement
Guided radar as solution in cement
Radar technology for continuous level measurement in maceration
Level measurement with ultrasonic
There are also other measuring principles such as ultrasonic measurement: This method uses an ultrasonic sensor that emits sound waves and measures the reflected waves. The fill level is determined based on the transit time measurement or the change in amplitude of the reflected sound waves.
Radar versus ultrasonic - when to choose radar?
Radar is now both the cheaper and more reliable choice for continuous level measurement in a wide range of industrial applications. Unlike ultrasonic sensors, build-up does not affect the precision or continuity of the measurement results with radar. Also, the blocking distance is not increased in such scenarios. The non-contact radar devices are completely resistant to contamination and do not require cleaning. Interference factors caused by build-up on the antenna system can be suppressed by optimised signal processing of the sensors. Overall, compact 78 - 80 GHz radar sensors work more accurately, are less susceptible to environmental influences and are a real alternative to ultrasonic technology in terms of price. Switching to radar is therefore worth considering.
What should you look out for when choosing
the right continuous level measurement system?
The respective measuring principles offer different advantages and disadvantages in terms of their accuracy, range, reliability and areas of application. The selection of the appropriate method depends on the specific requirements of the application, such as the type of medium, the container material, the environment including temperature, pressure and dust intensity, the safety requirements and international certifications. It also depends on the requirements for measuring accuracy and durability.
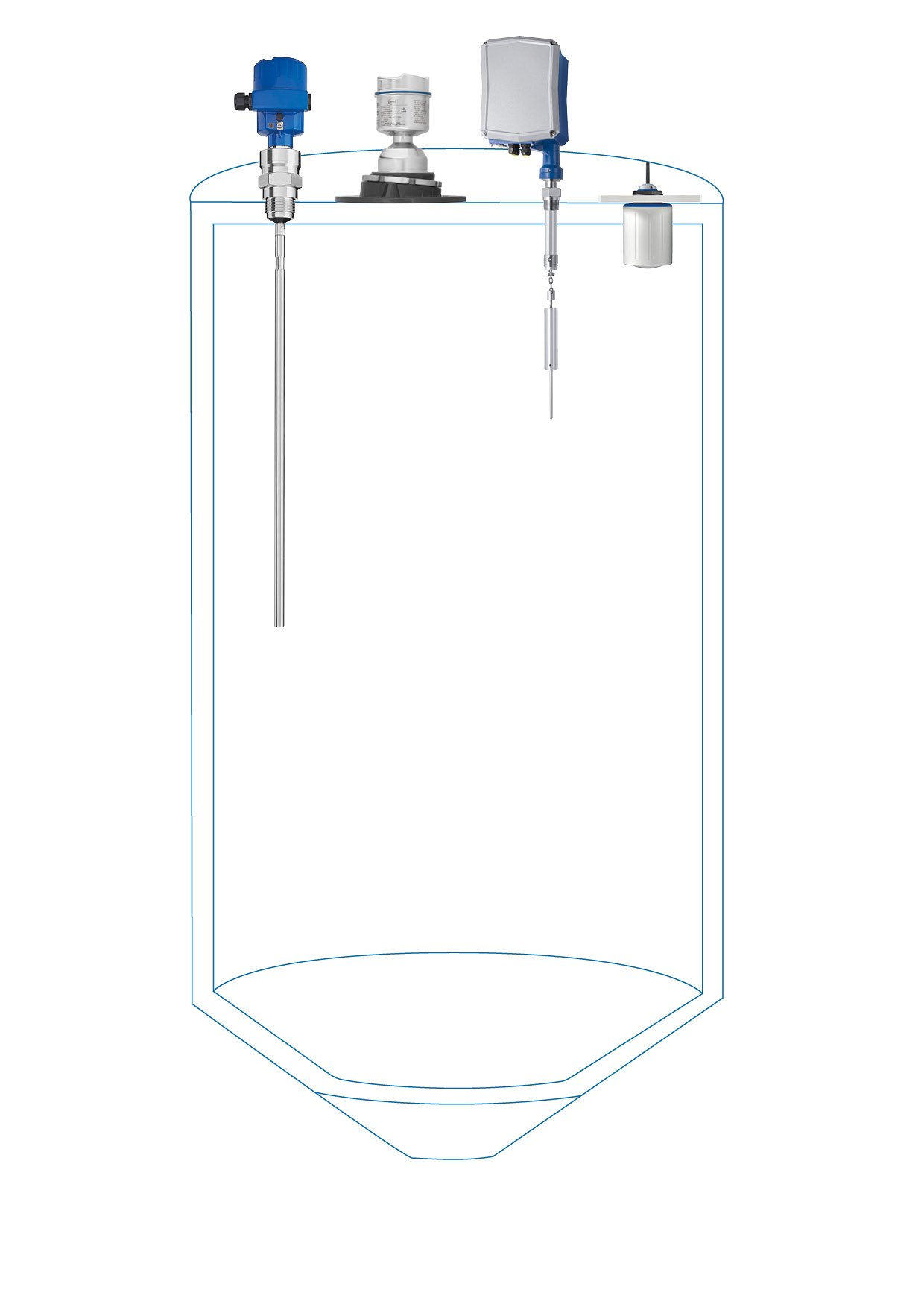
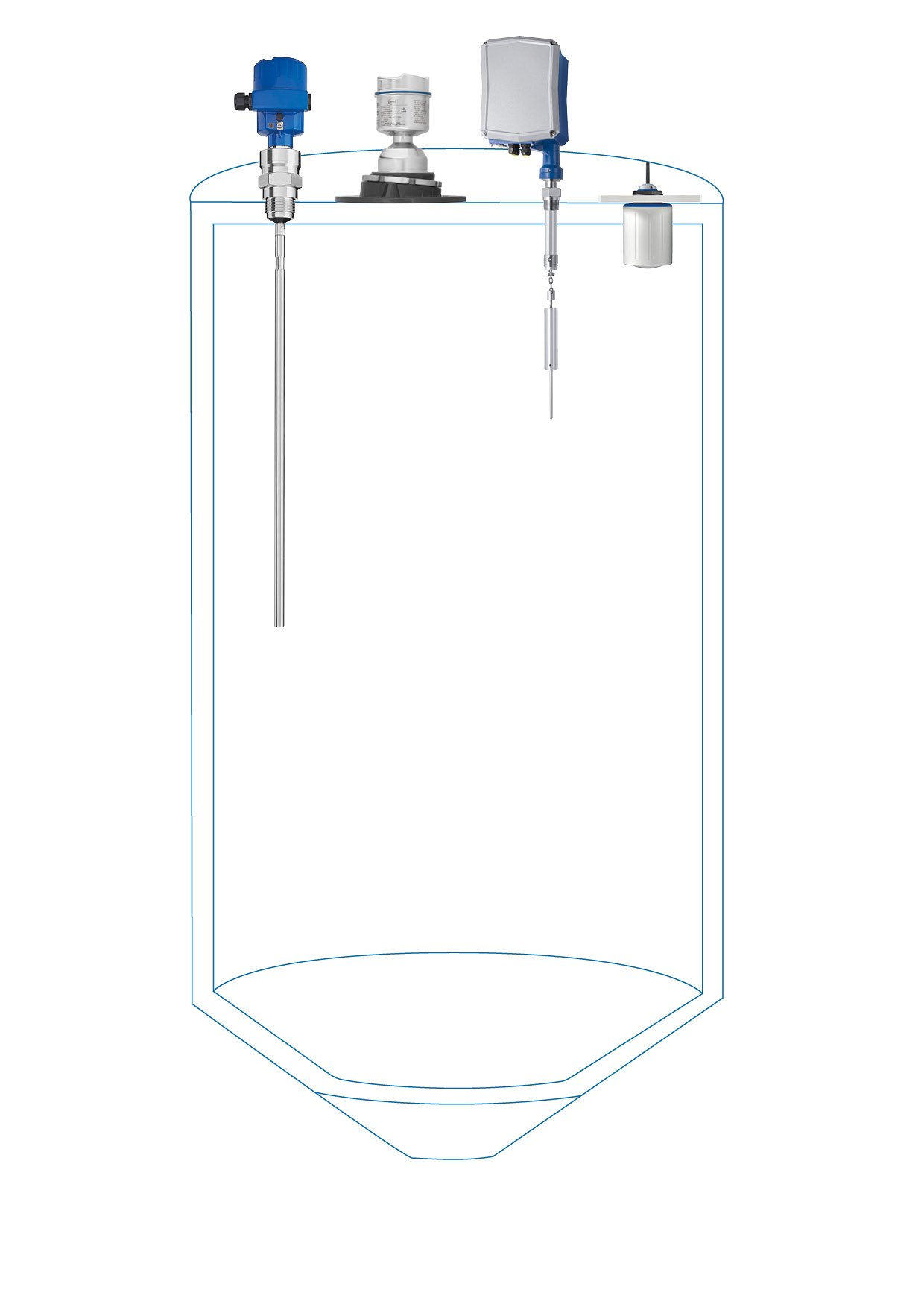
Sensors for continuous level measurement of bulk solids


Sensors for continuous level measurement of liquids
Checklist for selecting the right
continuous level measurement system:
- Type of medium to be measured: Different media require different measuring principles and sensors. It is important to know whether the medium is liquid, powdery or solid, whether it is aggressive or corrosive and whether it has special properties that could influence the measurement.
- Measuring range: Check the desired measuring range of the fill level. Make sure that the selected sensor covers the entire range in which you want to carry out measurements. Also take into account potential fluctuations in the fill level.
- Ambient conditions: Observe the ambient conditions under which the measurement will take place. Check factors such as temperature, pressure, humidity and potential vibrations. Make sure that the selected sensor is suitable for these conditions.
- Measuring principle: There are various measuring principles for level measurement, such as hydrostatic, capacitive, ultrasonic or radar-based measurements. Each principle has its own advantages and disadvantages, depending on the specific requirements of your application. Consider the accuracy, measurement precision, reliability and maintenance requirements of the different principles.
- Installation requirements: Consider how the sensor is to be installed. Some sensors require special mounting or a specific installation position. Make sure that the installation is possible in your application.
- Output signal and communication: Check which output signal the sensor provides and whether it is compatible with your existing control or monitoring systems. Ensure that communication between the sensor and other devices functions smoothly.
- Costs: Consider the cost of the sensor and the associated installation. Compare different options to achieve the best price-performance ratio.
- Maintenance requirements: Investigate the maintenance requirements of the selected sensor. Some sensors require regular calibration, cleaning or other types of maintenance. Make sure you have the necessary resources for this.
Continuous level measurement enables constant monitoring of the fill level in containers or tanks in order to control processes efficiently and ensure that the fill level remains within defined limits. With the right choice of level measurement method, process control and safety in industrial applications can be optimised and operating procedures made more efficient.