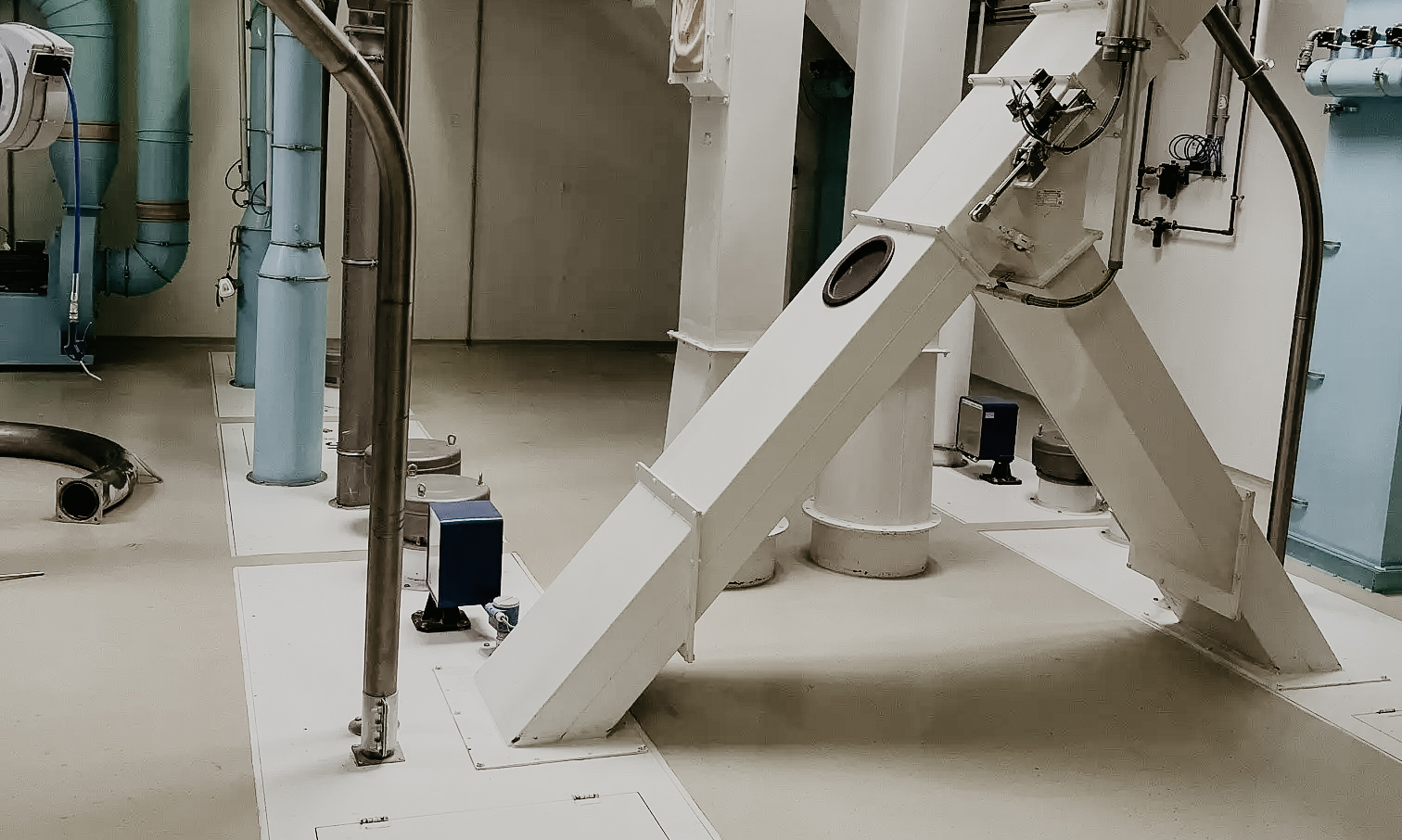
Visualization
There are different types for level indication, from simple LED digital displays for the evaluation of a 4-20 mA signal for installation in control cabinets or up to wall mounted to touch panels and web server modules with visualization software. The technologies can be configured on a project by project basis and adapted to customer requirements.
-
-
Networked production sites for optimum project visualisation
-
Easily accessible fill level indicator - the NivoTec® 9000
-
Level monitoring & visualisation overview
-
Level measurement overview
-
TDR solution for cement
-
Upgrade of level monitoring system in grain storage
-
Non-contact radar level measurement for fast running train tippler hopper
-
Radar technology for continuous level measurement in maceration
-
Interface level detection in stone reclaim slurry measurement
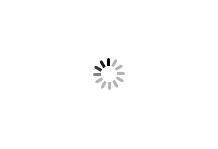
Categories
Application Stories
Application Stories
[73]
Case Studies Medium
Case Studies Measuring Task
Product Highlights
Product Highlights
[16]
Level Measurement Explained
Level Measurement Explained
[11]
How-to
How-to
[15]
UWT Behind The Scenes
Recent Posts
Tags
meet us
discover
projects
products live
overfill protection
inside uwt
silo/tank management
dry run protection
food compliant
min/max detector
chemical resistance
ex approvals
caking material
ehedg
contact-free
high temperature
manual
instructions
abrasive material
mechanical load
pps/pvdf
universal voltage
liquids
coax
active shield
sil
hygiene
whg
io-link
high pressure
master class
webinar
podcast
visualization
foam
uwt cares
boiler approval
remote
pfa/ceramic
touchpanel
Archive