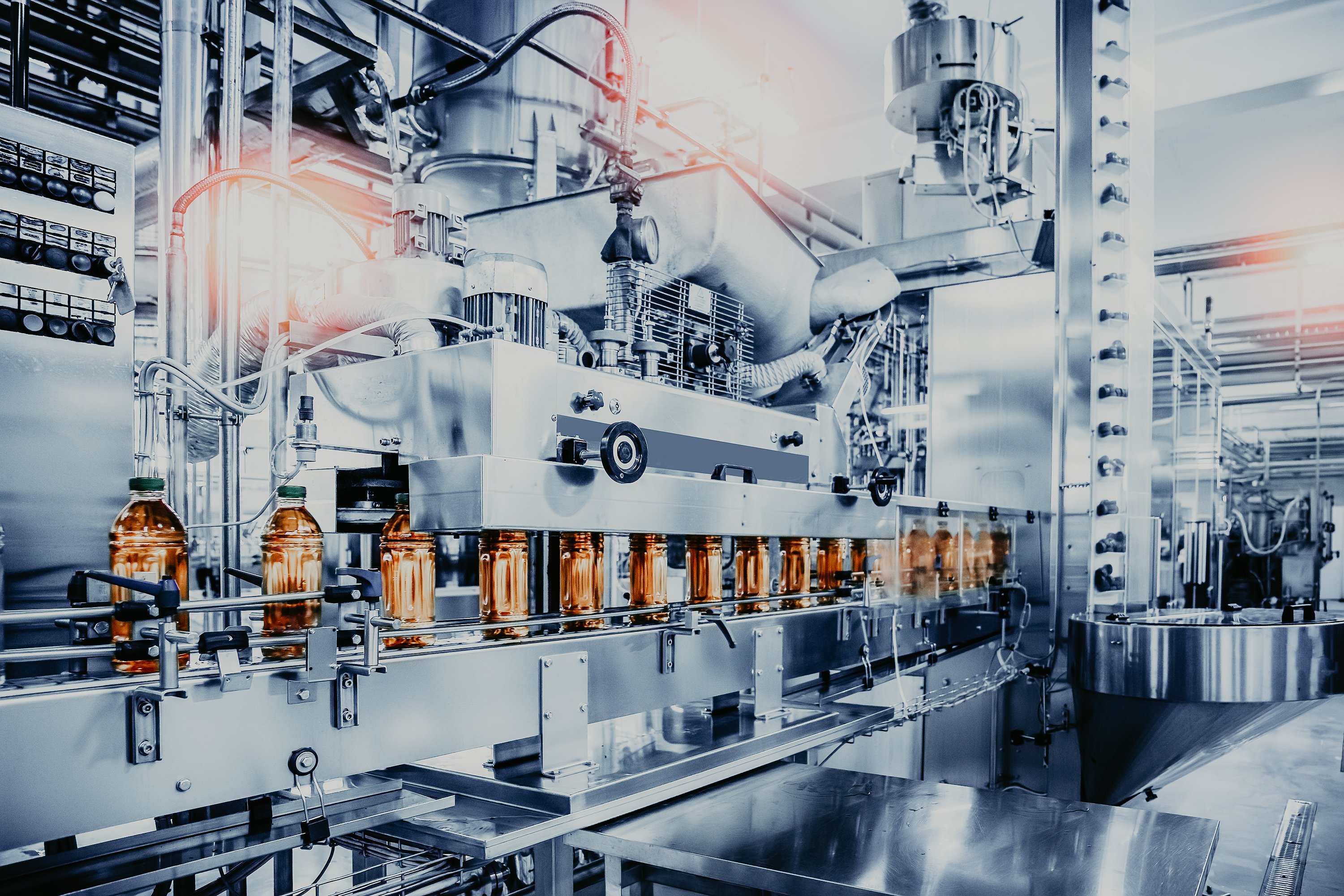
abrasive material
Abrasives are hard grains that are used for grinding, i.e. for material removal by machining with bound grain.
-
-
Reliable Point Level Detection for Coffee Filling
-
Precise Asphalt Mixture Thanks to Accurate Dosing
-
Tailored Solutions for the Synthetics Industry
-
Stay cool! Radar measurement under high process temperatures
-
Reliable level measurement of sterile injection products
-
Manage dust & corrosion with measurement technology as hard as steel
-
Capacitance point level detection of silicon metal rock
-
TDR Solutions for tricky level measurement applications
-
Non-contact radar level measurement for fast running train tippler hopper
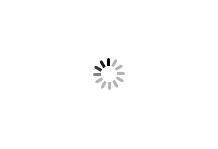
Categories
Application Stories
Application Stories
[73]
Case Studies Medium
Case Studies Measuring Task
Product Highlights
Product Highlights
[16]
Level Measurement Explained
Level Measurement Explained
[11]
How-to
How-to
[15]
UWT Behind The Scenes
Recent Posts
Tags
meet us
discover
projects
products live
overfill protection
inside uwt
silo/tank management
dry run protection
food compliant
min/max detector
chemical resistance
ex approvals
caking material
ehedg
contact-free
high temperature
manual
instructions
abrasive material
mechanical load
pps/pvdf
universal voltage
liquids
coax
active shield
sil
hygiene
whg
io-link
high pressure
master class
webinar
podcast
visualization
foam
uwt cares
boiler approval
remote
pfa/ceramic
touchpanel
Archive