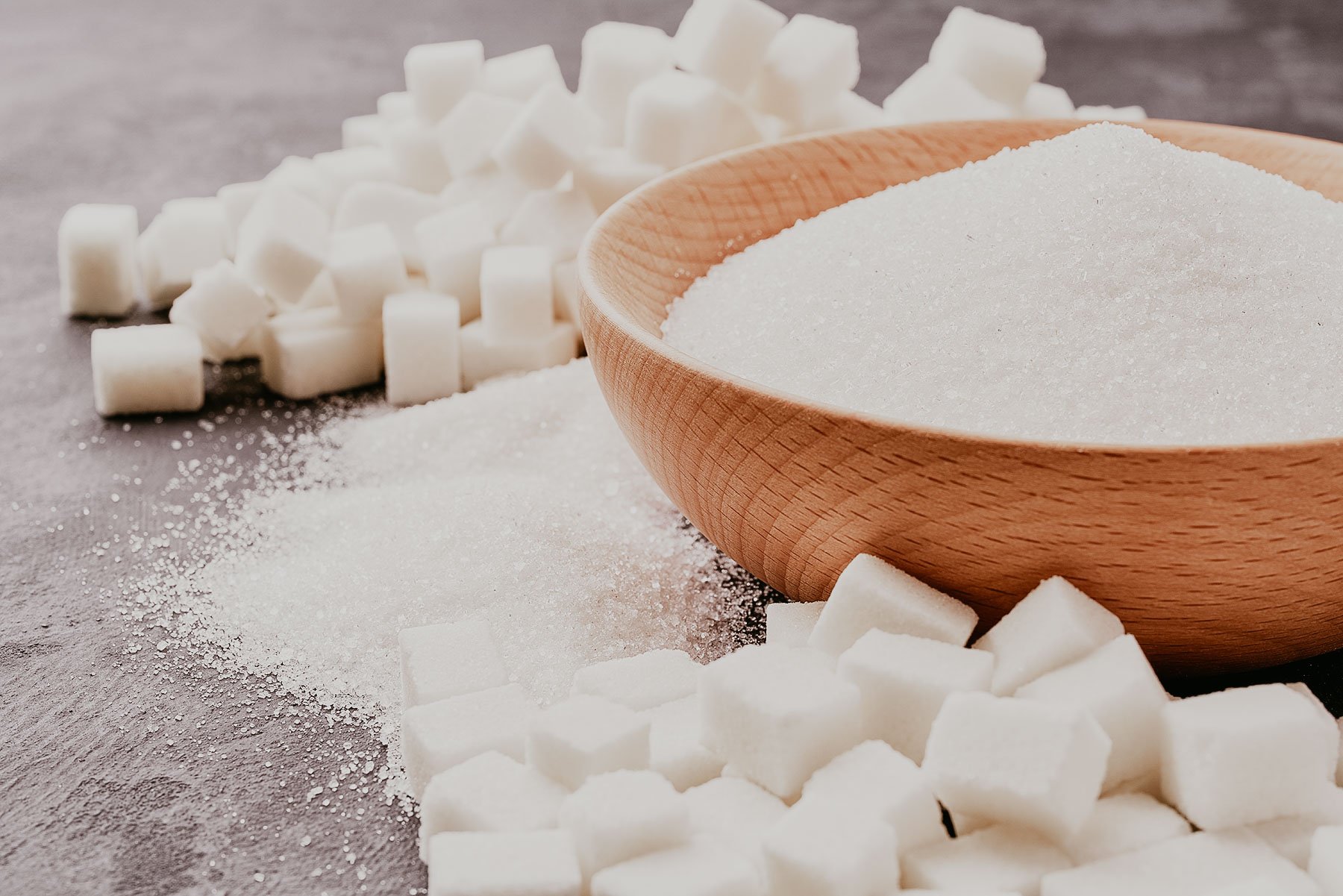
Optimize sugar production: level limit measurement with vibrating rod & continuous measurement with radar
To record stock levels and control recipes for batch and continuous blending, plants need reliable and accurate measurement data to ensure that everything runs smoothly in production. Every industry with its variety of complex applications and materials likes to surprise at this point with tricky tasks. In the food sector, high standards generally have to be met in terms of hygiene and process reliability. In the case of the application processes of a sugar manufacturer in Central American Guatemala, it becomes clear that reliable, durable and flexible solutions for batch measurement have a positive effect on the entire processing procedure.
Sugar in its sweet variety
To support the production of its various sugar end products, a sugar mill in Guatemala was looking for suitable measurement technology for determining limit levels as well as for content control in silos and process vessels at the beginning of 2017. The plant processes cane sugar mainly into household sugar including liquid sugar and granulated sugar or refined sugar in various grain sizes, as well as white sugar and muscovado.
Since the late 1980s, growth in world sugar production has been mainly attributable to cane sugar. In contrast, beet sugar production has remained virtually unchanged over the same period at around 33 million tons. In the 2016/17 marketing year, cane sugar accounted for around 78 percent of total sugar production and beet sugar for 22 percent. South America is one of the top world sugar producers, along with the Americas and Asia. In 2016/17, Guatemala was also among the countries with the highest sugar sales, along with Cuba, Brazil and Australia (according to WVZ (Wirtschaftliche Vereinigung Zucker e.V.) / VdZ (Verein der Zuckerindustrie e.V.). The sugar mill in Guatemala supplies the entire Latin and Central America region and also exports to the EU. For the local markets as well as in Honduras, El Salvador and Mexico, it is the main supplier of processed sugar end products.
Keeping an eye on silo contents with non-contact sensor technology
In addition to plumb bobs, radar sensors are often used for continuous level measurement in storage silos. They measure distances of up to 100 meters and, thanks to their high sensitivity, can be used not only in coarse-grained bulk solids but also in very fine bulk solids in particular. To provide the sugar plant in Guatemala with an innovative solution for the storage tanks for the produced granulated sugar or refined sugar, the non-contact
with adjustable flange was installed. With a height of 15 meters, the sugar silos hold 86,000 kilograms of material. The sugar level sometimes changes quickly and must be reliably detected in a full as well as empty message.
The device operates at 78 GHz high frequency. The high-frequency signal is emitted with a very narrow beam lobe of only 4°, reflected by the crystal sugar and received again by the sensor. The frequency difference, which is directly proportional to the distance, is then further processed and output as a level signal. UWT has equipped the radar sensor with an extra narrow beam lobe, as this allows the sensor to be used in narrow high silos and facilitates installation and placement. The radar was optimally aligned via the adjustment flange and the beam lobe was fixed to the desired point, the silo discharge.
Due to the robust stainless steel housing, the NR 3000 holds its own in various industrial applications, even in the detection of difficult media. Sugar is sometimes a rather difficult medium, as it can adhere to measuring sensors, depending on the consistency of the variety, and thus falsify the measurement result. This, in turn, can have an impact on the entire downstream processing operation if silo overflows or clogging of the filters at the top of the silo roof occurs. Of course, the use of non-contact technology is advantageous here. In addition, the integrated air purge connection for cleaning the lens antenna meant that it could be used here without any problems. Even in the case of condensate formation, the flushing connection ensures a functionally reliable measurement. The instrument uses two-wire technology and is easily commissioned via a local programming unit with display and a quick-start wizard. The free-radiating radar sensor has a completely dust-tight housing and provides reliable measurement results at process temperatures up to +200°C.
In warehouse processes, the NivoRadar® can be easily connected to the visualization system and offers a good combination option as an element for level determination. The data visualization provides the detected levels in height, percentage, weight or volume. Trends are stored, e-mails about fill levels or silo full messages can be activated. Remote retrieval of the acquired data can also be done via a GSM modem. There, the current measured values can be called up via the NivoTec® visualization software on any Ethernet PC using an Internet browser. Data access is particularly timely because the visualization controllers are directly integrated in the company Ethernet. System installation is uncomplicated and can be carried out by the company's own service personnel. The fact that all detected levels are available at any time ensures a certain degree of planning reliability for the plant operator.
Whether coarse or fine - the vibrating rod detects limit levels cleverly with its 4-step adjustable sensitivity
In recent years, there has been an increasing call for more compact level switches that offer a high degree of compatibility worldwide and can be used in a wide range of applications without major configuration effort thanks to common technical features. A design that has established itself on international markets features very small connection threads and operates according to the vibration principle.
Accordingly, UWT GmbH expanded the product family with the
For some process vessels within the sugar mill, the Mononivo® rod detector is ideally suited as a full, demand and empty detector, as it has connection threads from 1" and thus provides reliable measurement results even in limited space conditions. White sugar of different grain sizes (hail, semolina, powdered sugar) - with a DK value between 1.6 - 2.0 or a bulk density of approx. 490 g/l - is temporarily stored here.
The compact version of the MN 4020 with a boom length of only 160 mm was used as an empty detector in the lower quarter of the process bins. The vibrating rod was installed with an absolutely dust-tight housing as well as a robust sensor system which at the same time reacted sensitively enough at the boom to reliably detect material "presence" and "absence".
The version of the MN 4030 with a tube extension at the boom of 400 mm was installed from the silo roof for full detection. Here, the switching point could be flexibly adjusted by mechanical height adjustment.
The high surface quality of the probe booms made a wide range of applications possible in the various grained sugar types, even with more dust-intensive materials that tend to adhere. Particularly in the case of the very fine-grained products, the atmosphere was definitely very dusty. Due to the 4-stage adjustable sensitivity, very light, powdery types from 20g/l were reliably detected. At the same time, the robust shoring also allowed measurement in very coarse-grained sugar granules.
Inside the steel vessels, a process pressure of up to 0.8bar (11.6psi) prevailed, which was easily manageable for the single rod (pressure-resistant versions go up to 16bar). The process-contacting material of the unit is all stainless steel and food-grade. International approvals mean that it can be used without any problems, especially in areas where there is a risk of dust explosion. What particularly appealed to the sugar mill plant operator was that the Mononivo® vibrating probe is an uncomplicated solution for level detection, as even the standard version is highly compatible with the most common applications worldwide. It is robust, easy to put into operation without calibration and can already be configured exactly to the application during sensor selection through the different device series. For example, the rod probe is available with different flanges as well as variable boom lengths with tube extensions. KIT solutions with application-specific product design are easy to implement, which means individually quickly adaptable device designs and more flexibility for plant operators.