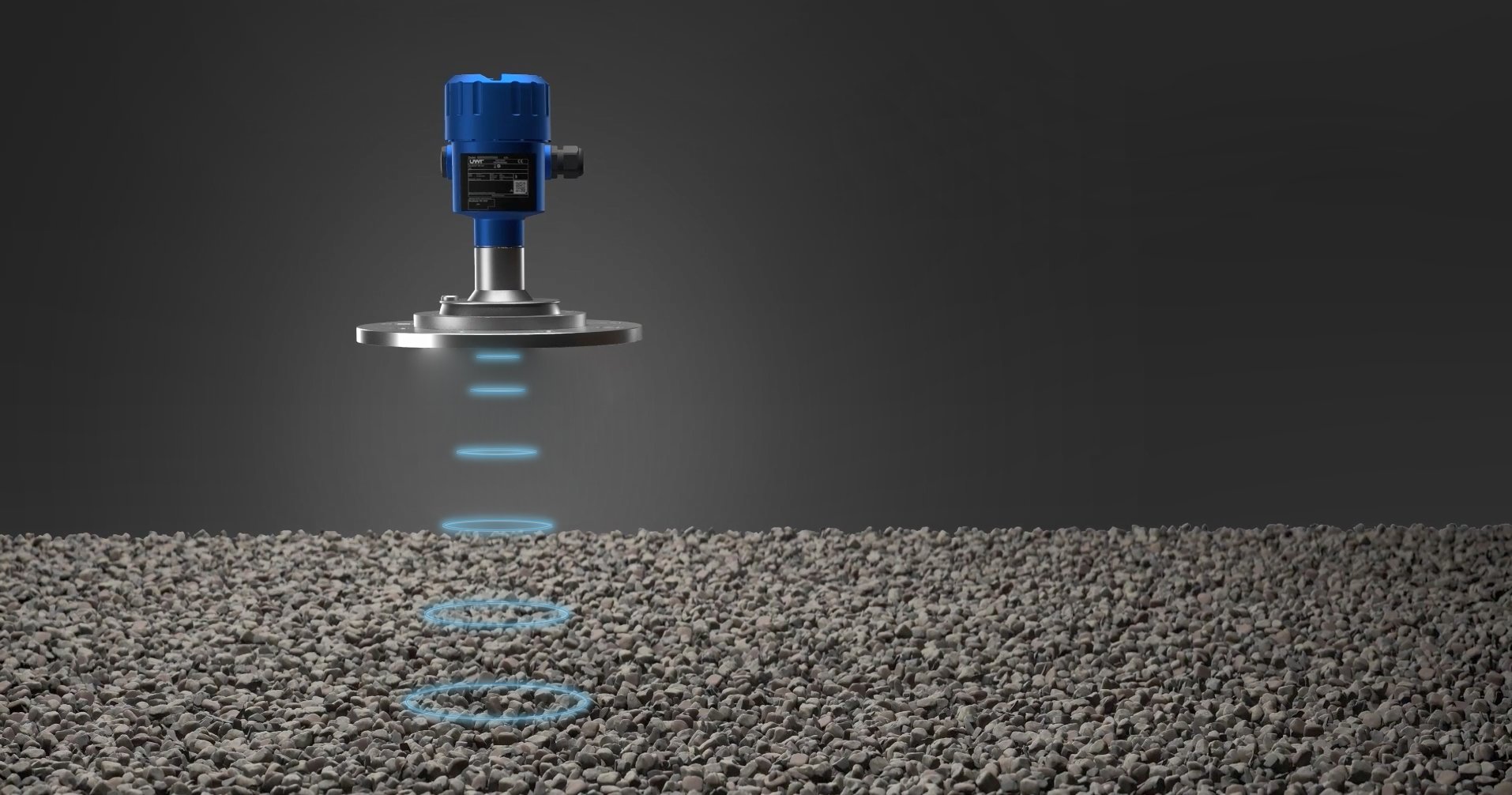
Efficient level measurement and monitoring:
Precision and safety combined
has become a crucial technology for many industries – from food and pharma to chemicals and energy. Why? Because it's precise, reliable, and functions well even in tough conditions. In this article, we explain how radar sensors work, what makes them so effective, and where they can deliver real benefits in practice.
How Radar Sensors Measure –
Basic Principles Made Simple
Radar, short for „radio detection and ranging“, works by transmitting and reflecting electromagnetic waves. A radar sensor emits a focused electromagnetic wave, which bounces back from objects as an echo and is then analysed by the sensor. This principle allows for precise measurement of distances, levels, or positions. The radar category includes both free-radiating radar sensors and sensors based on guided microwave technology, commonly referred to as guided radar, TDR (Time Domain Reflectometry), or GWR (Guided Wave Radar) sensors.
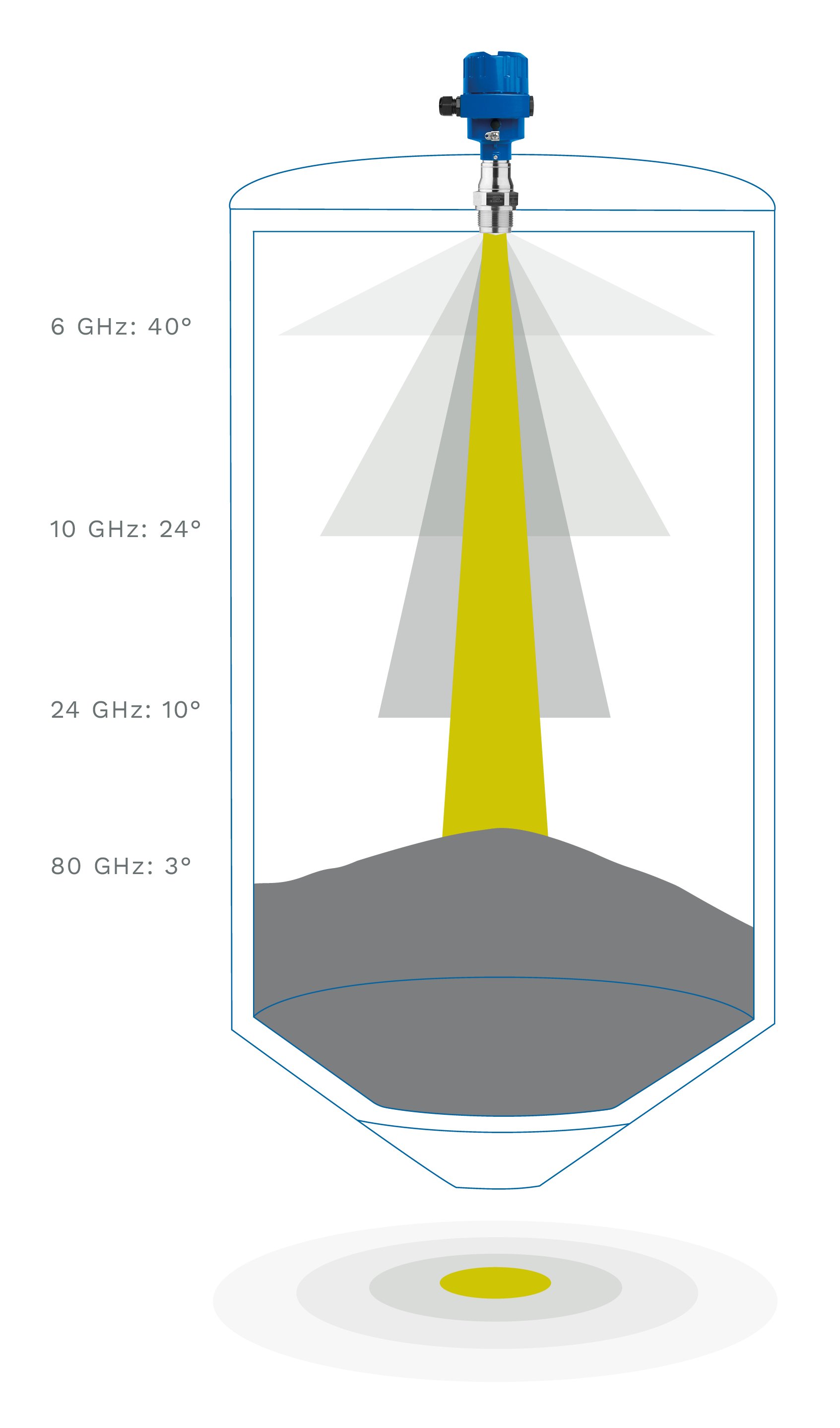
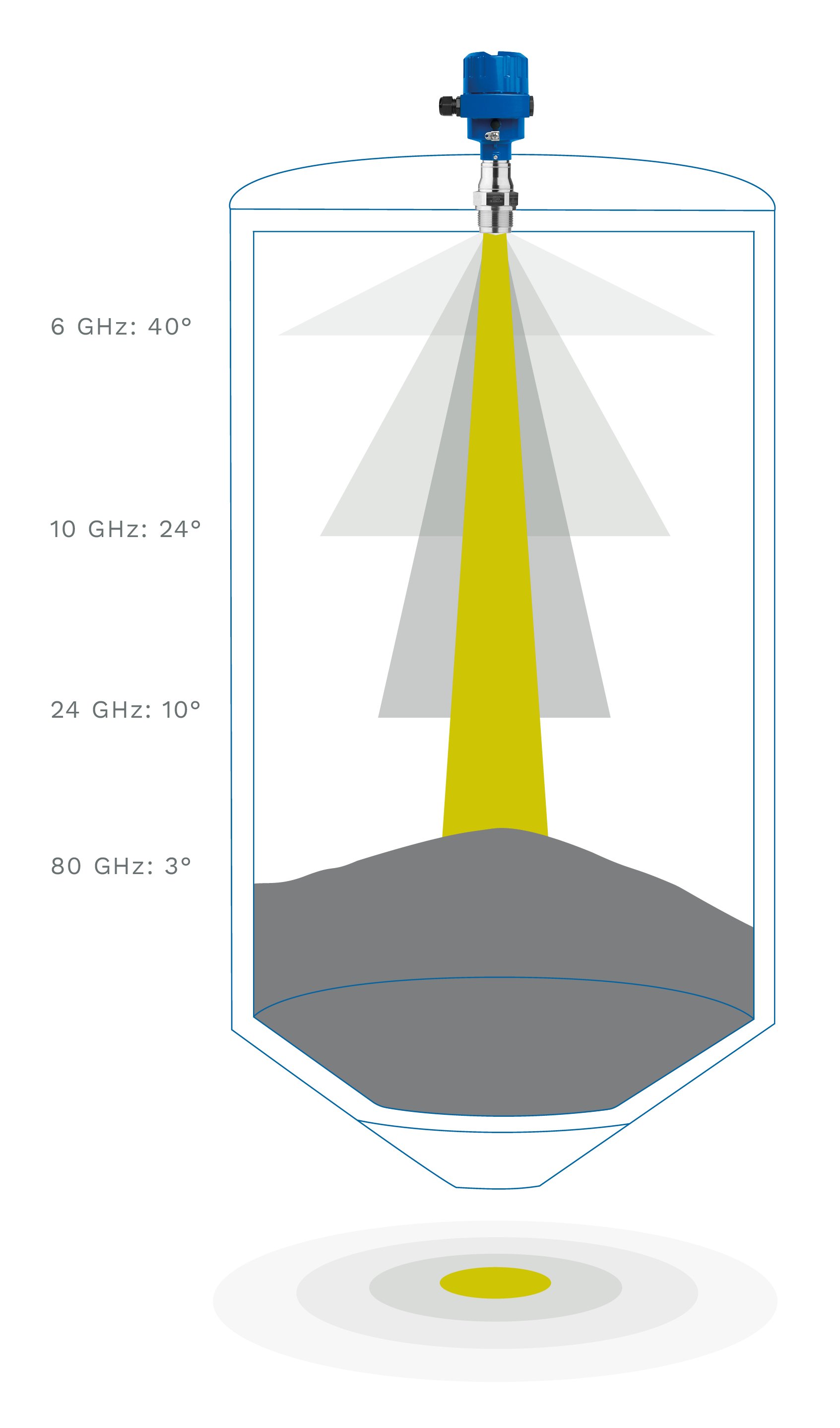
Illustrative example - bulk solids measurement with pouring cone: The beam angle increases significantly as the frequency decreases – the 80 GHz technology offers the highest precision with just 3°
Non-contact radar sensors
They operate without physical contact sending electromagnetic waves that are directed toward the medium using specialised antenna designs. The frequency greatly impacts performance – it determines how accurately and reliably the fill level can be measured in process or storage vessels.
High-Frequency Technology
Radar sensors with high frequencies, such as 80 GHz technology, can be designed compactly, feature narrow beam angles of up to 3°, and offer excellent reflection properties. This enables them to deliver precise and reliable measurement results, even in complex tank geometries or confined shafts and pipes.
Typical Applications
They are ideal for liquids and bulk solids in silos, tanks, and open containers, especially when non-contact measurement is preferred due to hygiene or process requirements.
Guided radar sensors
Here, the high-frequency signal is transmitted directly to the medium via a guided probe – either as a rod or cable. Known as TDR (Time Domain Reflectometry) or GWR (Guided Wave Radar), the technology uses the probe as a waveguide for the microwave signal. The direct contact with the medium offers key advantages in complex applications: even with foam, vapours or weak reflections, the measurement remains stable and precise – making it ideal for demanding process conditions.
Low-Frequency Technology
Guided radar sensors often operate at very low frequencies (e.g., 1 GHz), making them particularly resistant to dust, build-up, foam, or steam. This makes them ideal for applications involving moving surfaces or interface measurements.
Customisable Probe Types
Various options, such as rod probes, cable probes, or coated probes (e.g., PA), allow flexible adaptation to specific process requirements.
Typical Applications
They are especially effective in challenging process conditions, such as highly dusty environments within silos or tanks containing aggressive media.
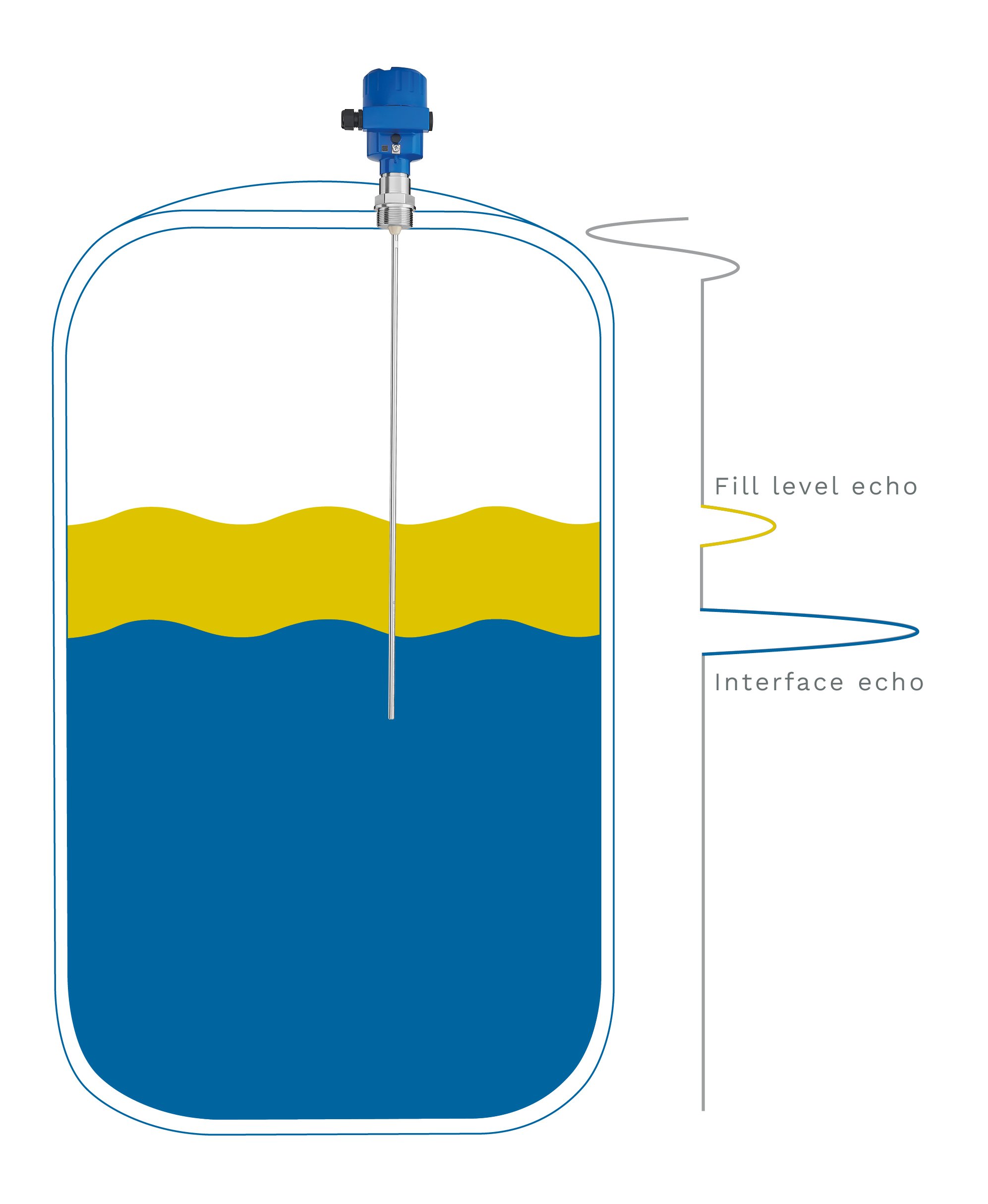
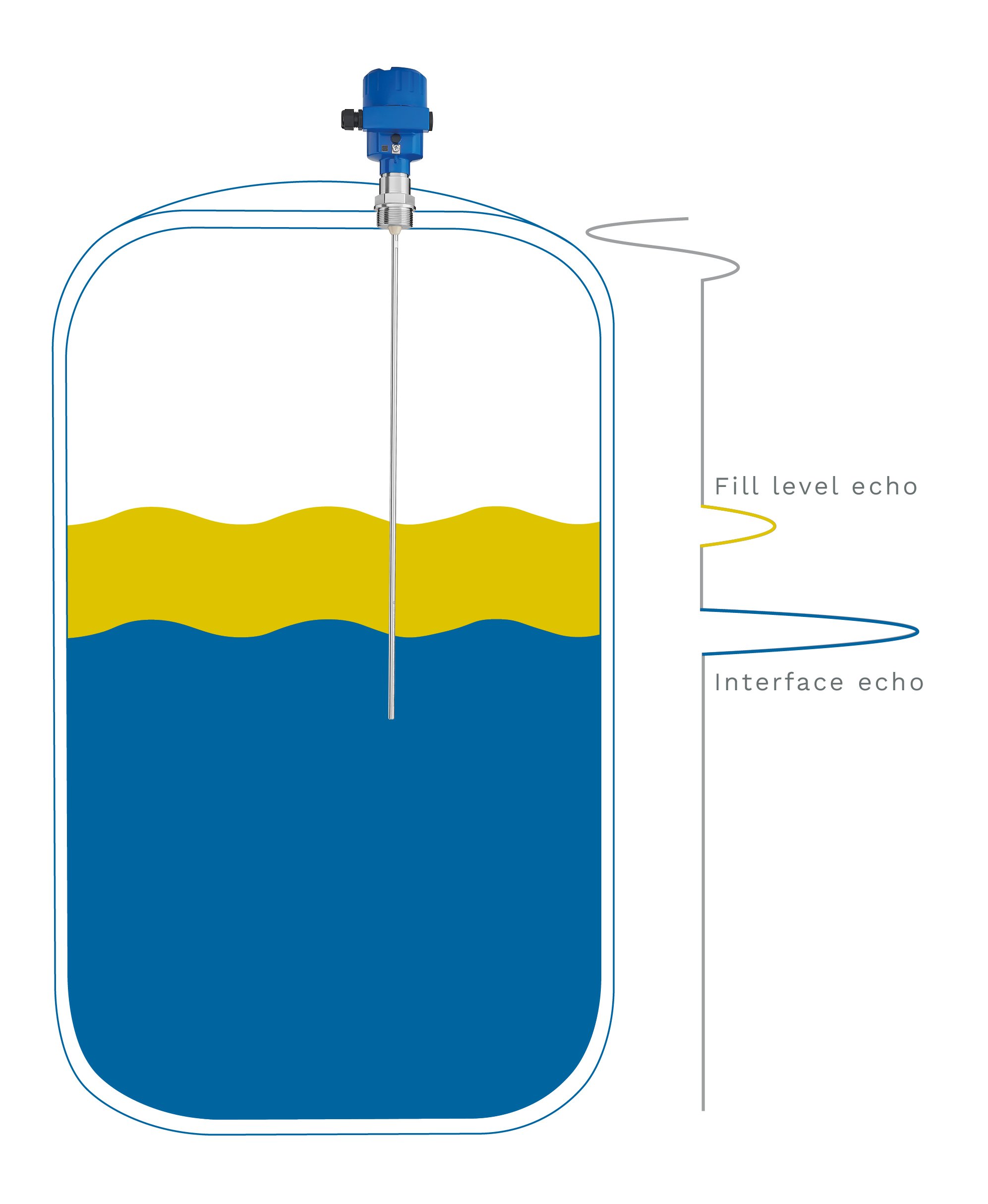
Interface measurement of liquids with different DK values:
The microwave pulse reflects off the upper layer (e.g., oil),
penetrates it, and is reflected at the lower layer (e.g., water)
back to the sensor
Adapting to Different Media
In addition to the measurement principles, distinctions are also made based on the various properties of the measured media:
Liquids
80 GHz radar technology offers versatile solutions for precise level measurement of liquids. Smooth surfaces and high reflectivity produce clear signals and straightforward measurement. The narrow beam angle of high-frequency radar sensors enables accurate detection, even in narrow tanks or turbulent surfaces.
Solids
Bulk solids are more challenging due to irregular surfaces, dust generation, and material cones. Modern radar systems excel in these conditions with robust signal processing that provides precise measurements even in demanding circumstances. The combination of high temperature and pressure resistance, minimal dead zones, and measurement accuracy of up to ±2 mm makes this technology the ideal choice for dusty environments within silos or complex bulk material processes.
Advantages of Radar Technology
Radar measurement offers many benefits, making it particularly suited for demanding applications:
High Measurement Accuracy: Radar sensors yield precise results, even under challenging conditions such as extreme temperatures, high pressure, or aggressive media. This ensures reliable process control and quality assurance.
Radar Measurement: Radar technology is characterised by exceptionally high measurement accuracy and delivers precise results without requiring physical contact with the medium.
Maintenance-Free Operation: Because measurement is either non-contact or conducted via a guided wave, wear and mechanical failures are virtually eliminated. This extends system lifespan and reduces maintenance costs.
Resistance to Contamination: Radar sensors operate reliably even when dirt or build-up occurs. Optimised signal processing filters out interference, eliminating the need for cleaning.
Independence from Process and Environmental Influences: Conditions like temperature, pressure, vacuum, fog, wind, or rain do not affect measurement accuracy. These sensors provide reliable results under all environmental conditions.
User-Friendly Operation: Easy setup and optional sensor configuration, such as via UWT LevelApp, save time and enable quick commissioning and diagnostics.
Functionality in Flooding Conditions: Radar sensors can measure reliably up to the sensor antenna, even in flooding situations. They have no dead zone, require no protective covers, and remain operational even in extreme conditions.
Precise Signal Focusing: The 80 GHz technology allows for precise alignment of the radar beam on the medium to be measured, simplifying the separation of measurement and interference signals – and providing easy and accurate measurement even in narrow shafts or with installations such as pipes and pumps.
Versatility: Radar technology is highly versatile, suitable for a wide range of applications—from silos containing solids and liquid tanks to complex process systems or open-air applications such as outdoor stockpiles – streamlining system design by minimizing the need for multiple sensor types.
Radar Sensors for a Broad Range of Industries
In summary, radar measurement has become an essential technology for modern process industries. It combines precision, reliability, and versatility – proving invaluable across a wide range of sectors:
In the food and beverage industry, for hygienic measurement of milk, juices, sauces, or powders,
in the chemical sector, for aggressive media such as acids or solvents,
in the pharmaceutical industry, for sterile processes like fermentation or active ingredient monitoring,
in the energy and utilities sector, for materials such as coal, ash, biomass, or sludge,
in the environmental and recycling sectors, for level detection in silos containing residual or recycled materials,
in the construction and cement industry, for level control of cement, lime, or gypsum,
in plastics processing, for granules and bulk solids in dryers or mixing tanks,
in metal and glass industries, under high temperatures or dusty conditions,
and in many other sectors that require robust, maintenance-free, and precise level measurement – from the wood and paper sector to animal feed production and water and wastewater management.
Thanks to their wide range of designs, radar sensors can be easily tailored to various process conditions and applications.
With ongoing technological advancements, radar continues to play a key role in optimising processes, improving operational safety, and boosting efficiency across industries.