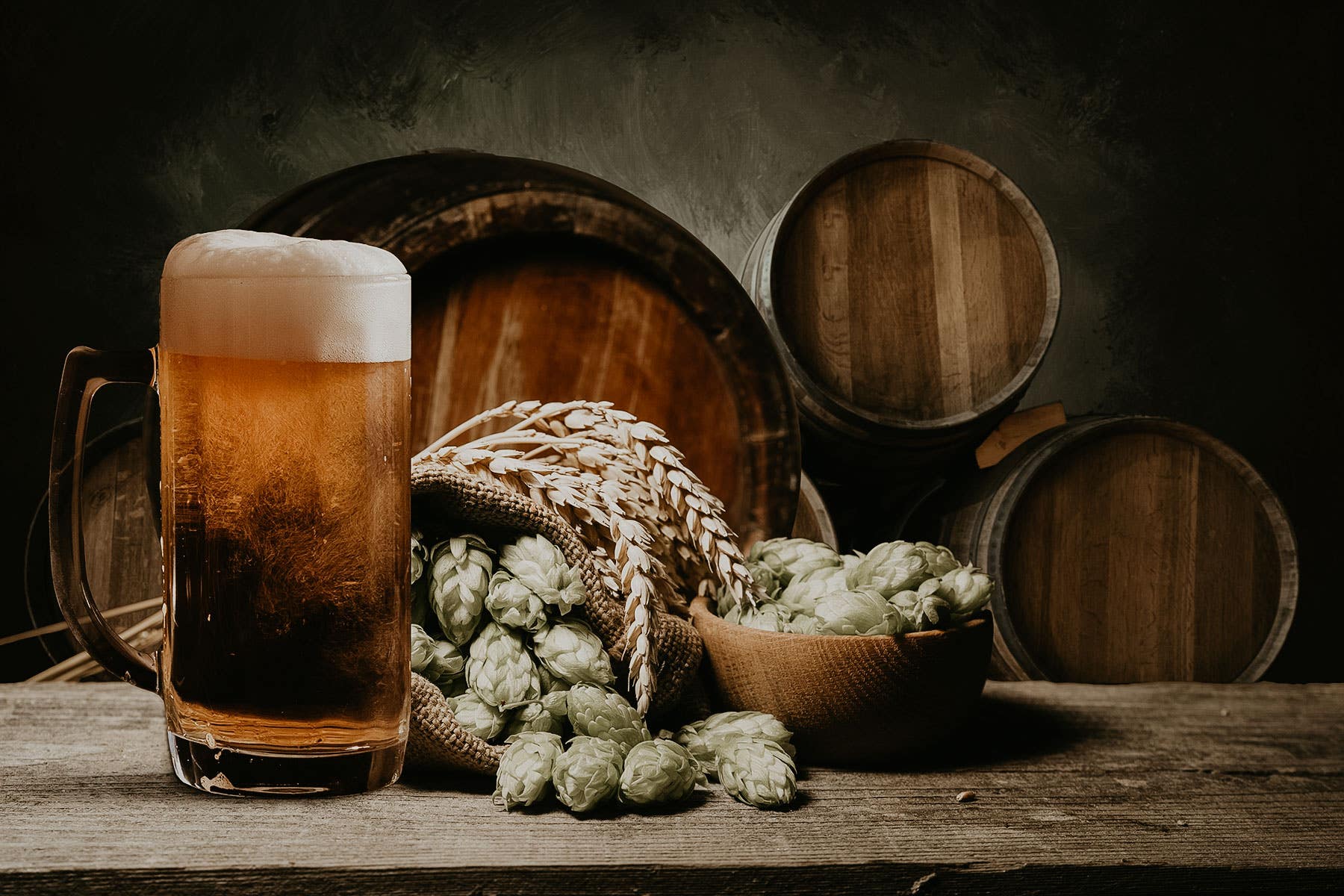
Active batch compensation & food conformity & CIP suitability
In the food industry, absolute hygiene is among other things of upmost importance, whereby high demands are placed on the measuring technology to be installed in terms of design, functionality and reliability. Especially in the beverage industry, these demands can be very specific. A Peruvian beer producer was looking for suitable solutions for the overfill protection as well as the idling protection of its process vessels holding different solid and liquid raw materials required for the various production processes. To equip the malt addition process the innovative RF technology was chosen. UWT capacitive limit switches which have been designed to cope with high temperatures as well as applications with highly caking materials such as the viscous liquid of the malt mixture, were installed.
It tastes better when you know your limits
In 11,000 B.C., agriculture and grain farming are born, and the history of beer begins. Archaeological findings report on beer consumption in Babylon and Egypt. Different production techniques develop throughout Europe and later worldwide. In 1824, the British Navy produces a gallon (4.5 liters) of beer as part of the sailors' daily diet, and Pasteur begins his studies on the fermentation of wine and beer. Today, the long tradition of brewing can be found in the more than 22,000 breweries around the globe, often implementing it with cutting-edge technology.
One of the leading producers of lager and ale on the Peruvian beer market, with several decentralized beer production facilities in Lima, Motupe and Pucallpa, among others, was looking for flexible and reliable measurement technology as part of the modernization of its facilities. The equipment for the maceration processes for must production proved to be somewhat tricky. The difficulty was to control the correct dosage of the malt when it was dissolved in water. This was because the grain became very sticky after wetting and thus caused false alarms in all test sensors. Together with the local UWT partner SIERRA Servicios Industriales SAC. a suitable level switch was configured to solve this problem. The
sensor, rod version with "Active Shield" technology on board proved to be the right choice. The active shield compensation, which is integrated in the capacitive measuring principle of the RF sensor, ensures that the probe switches reliably without being influenced by material buildup. With an additional guard electrode the probe can reliably measure even when highly conductive buildup is present ignoring debris and buildup.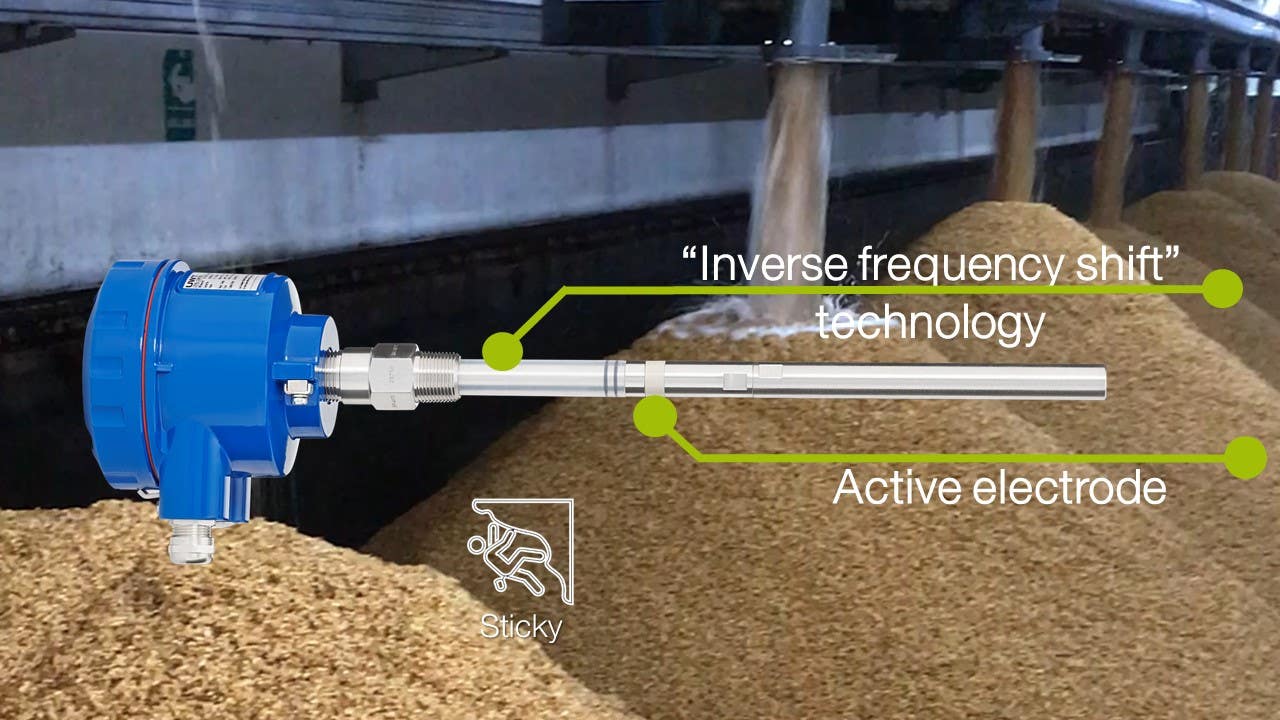
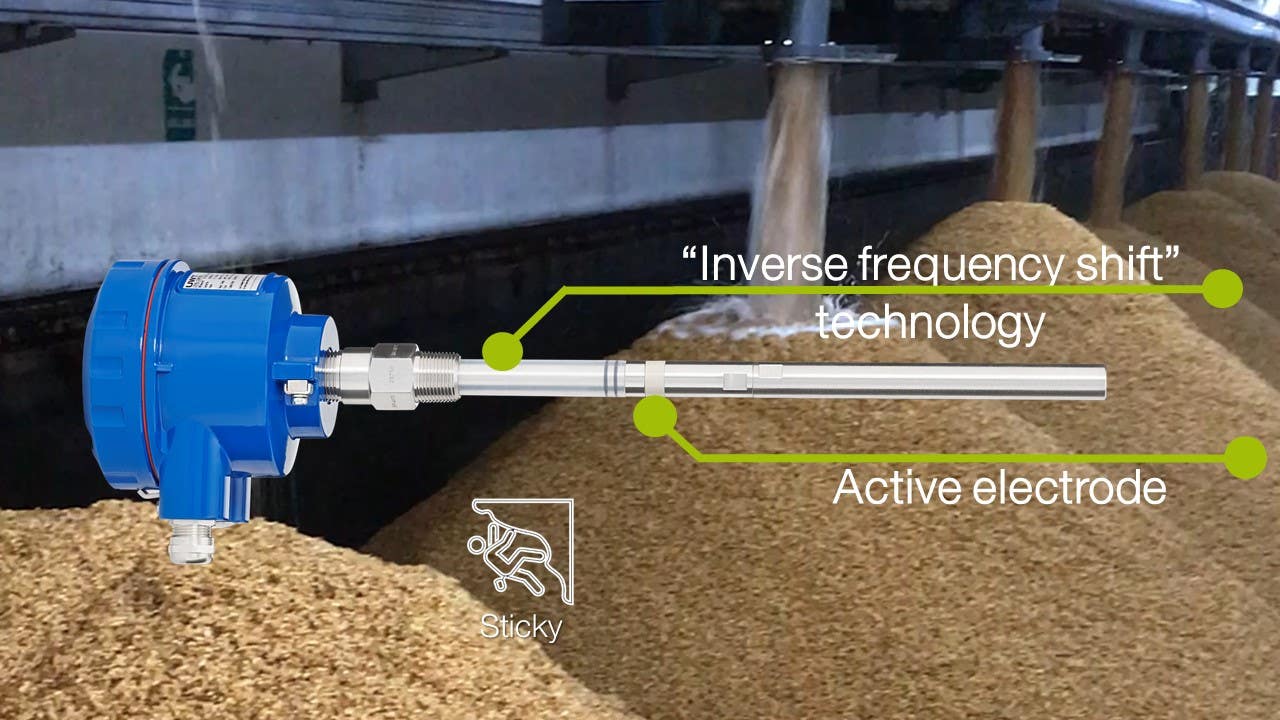
Based on sodium hypochlorite used, process temperatures can reach up to 80°C (176°F) during cleaning in place (CIP) processes. The 250 mm long probe arm was therefore equipped with PFA-coated stainless steel, PEEK insulation parts as well as FKM seals, ideal to withstand the aggressive high temperature within the cleaning process. In addition to the standard Ex approvals, the RF 8000 series is certified according to Lloyd's Register and WHG. It was also essential to use only food-grade materials for all instrumentation parts that come into contact with the product. The DK value of the viscous liquid is approx. 4.0 whereby the process atmosphere inside the stainless steel tanks is very vaporous. The robust level switches were installed on the side of the process tanks for demand indication and control the appropriate malt addition within a measuring range of 10 meters by means of a rapid and precise material detection.
A small change in capacitance results
in a relatively large change in frequency
Because this capacitive measurement technology uses the "frequency shift" technology, instead of measuring the capacitance directly, the change in frequency can be determined. For example, in an empty container the probe is not covered, the frequency is high but the capacitance is low. When the container fills, the probe is covered with the material and thus the frequency drops and the capacity increases.
What can be clearly seen is that a small change in capacitance results in a relatively large change in frequency. Because the frequency can be evaluated, even small changes in the level can be detected. A very high measuring accuracy is a given as the sensor with its high sensitivity can be adjusted as required. As the capacitive RFnivo® level switches are all-rounders and function reliably in bulk solids, granulates, powders as well as liquids, pastes and highly viscous oils, further silos, tanks and process vessels of the brewery plants were equipped with the level switches for full, demand and empty detection. Even in hoppers, pipelines and downpipes, the various device designs could be used flexibly.
With the installation of the corrosion-resistant min/max detectors, the process sequences of the beer production plants could be optimized quickly and easily with regard to overfill protection and empty protection, not only in the malt addition process. Certified UWT sensor technology is your beneficial ingredient for beverage production.