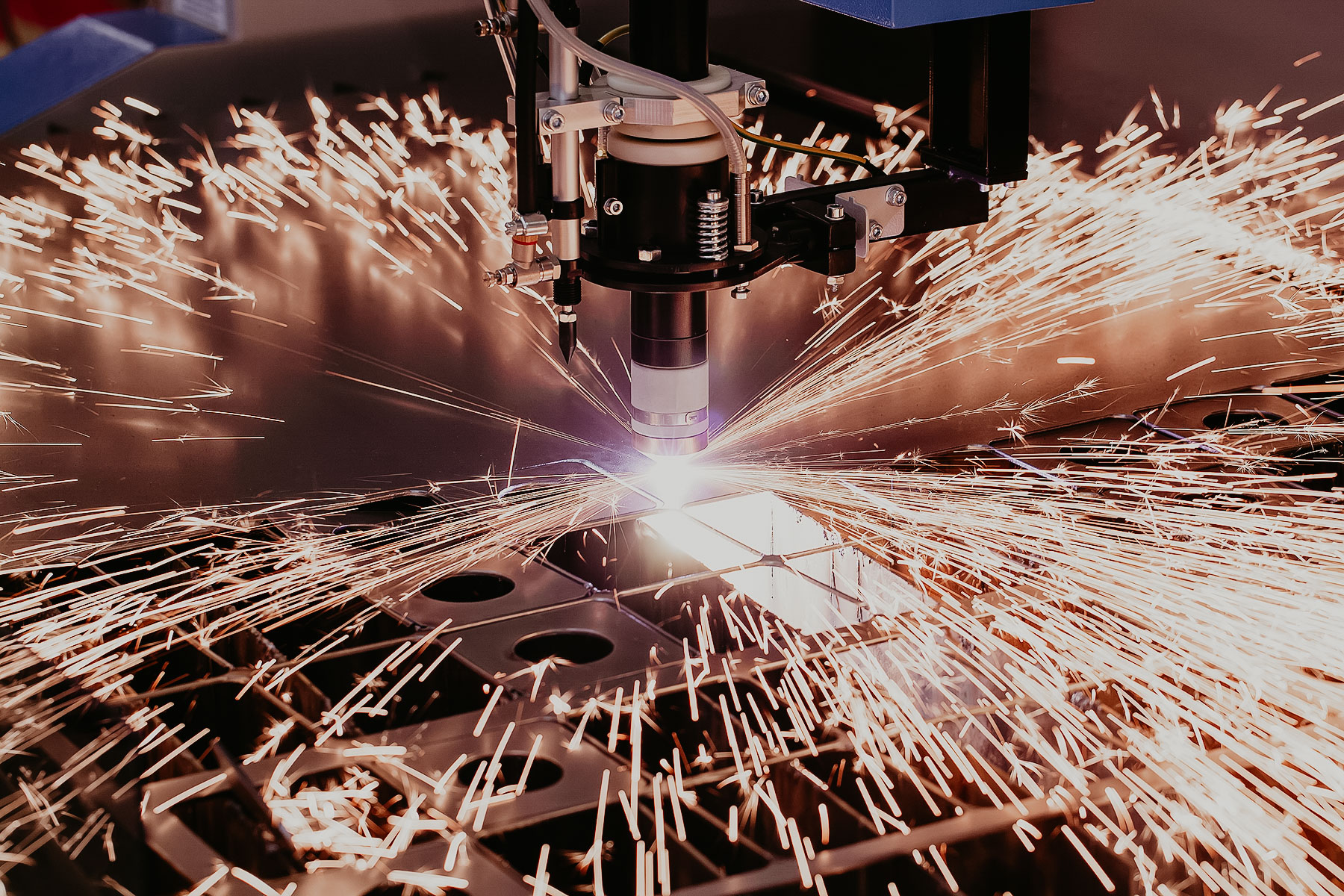
In the metallurgy and metal sector, conditions are often harsh, noisy and dusty. The level measuring devices must be robust and absolutely reliable as standard in order to ensure a continuous, stress-free production process. A modern solution for continuous level measurement with guided wave radar sensors was configured for a global steel producer near Santo Domingo. For precise results, the level measurement technology had to be unaffected by dust, abrasion and high process temperatures.
Guided wave radar sensors for continuous content measurement in iron ore
A globally acting steel producer was looking for a robust and at the same time very precise measuring technology for the equipment of several iron ore silos in the course of modernizing the plant in the Dominican Republic. The Company is engaged in the exploration, mining, processing and marketing of metals and mineral products with the principal products nickel, copper, cobalt and platinum being marketed globally.
For several 8 to 30 meters (26.2 to 98.4 ft.) high iron ore silos, the decision was made to install innovative radar technology with guided waves instead of the popular free-radiating radar sensor due to the heavy dust formation. Together with the local UWT partner Naniki Automation Solutions SRL, corresponding tests were carried out in the production plant under numerous significant process conditions with regard to temperature, pressure and corrosion.
The guided wave radar sensors of the NivoGuide® series are used for continuous level measurement in liquid and bulk solids applications. The measuring range of up to 75 meter (246 ft.) and its high sensitivity from a DK value of 1.5 enable versatile installation in silos, tanks and pipelines. The devices contain no moving parts in the process vessel. The microwaves are radiated at low frequencies so that no interference reflections occur even with high dust intensity. As a result, the energy content of the microwave can only be used to determine the specific filling level within the processes to be coordinated. The versions are each equipped with extensions that can be individually adapted to the application with rod and cable.
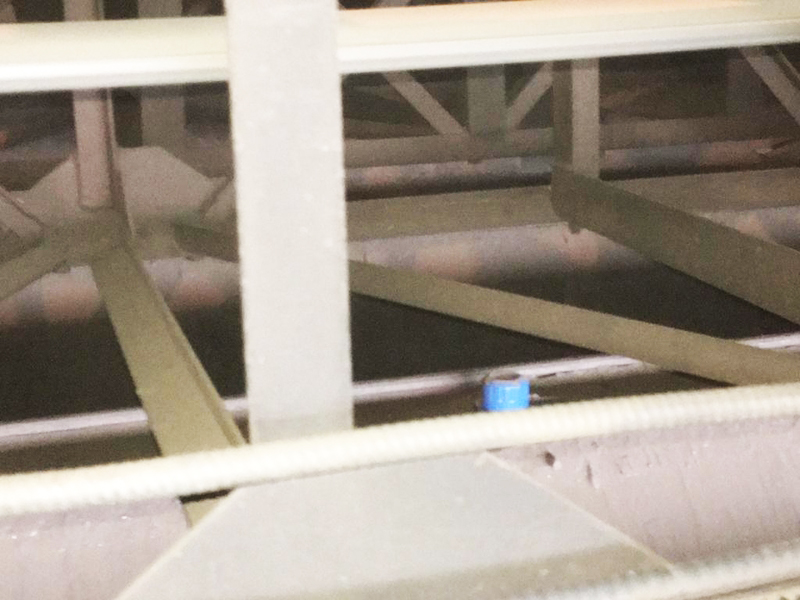
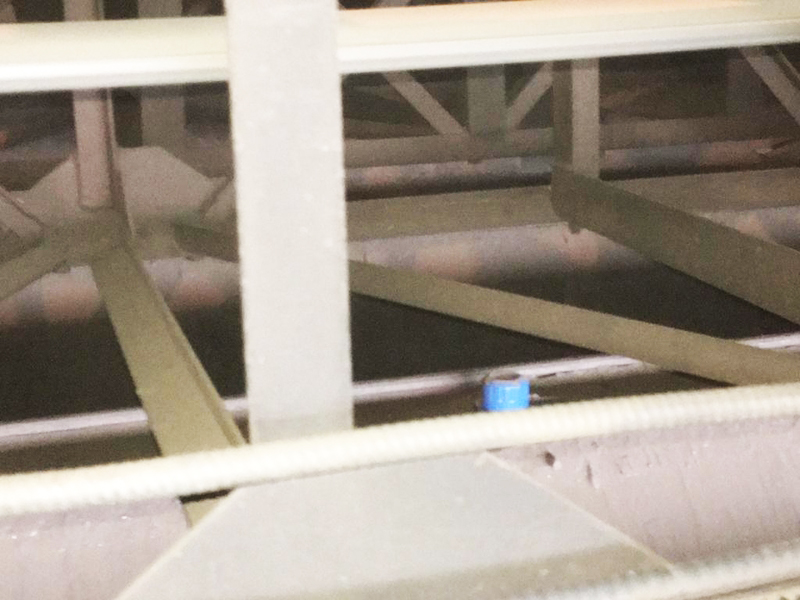
Robust design with high measuring accuracy
The
series of guided wave radar cable version was the perfect solution for the steel mill processes. With a reinforced coupling for high pull-off forces and a dust-proof construction, these TDRs are specially designed for the detection of solids measurements. In addition, the NG sensor is very flexible and does not need to be recalibrated when the material is changed. The measurement signal is "guided" along the cable and reflected by the medium, received again at the sensor and converted into a level signal. This makes it possible to measure reliably even in narrow and high containers, regardless of dust formation or buildup.
In addition, the cable of the radar device has been given a special PA coating, which also improves its abrasion resistance and makes it more resistant. Fine-grained bulk materials cannot settle in the mesh of the installed rope. It has an outer diameter of 11 mm (0.036 ft.) and can be fixed to the bottom so that it does not touch the silo walls during filling and emptying. The design of the coupling, optimized for solids applications, enables a tensile load on the cable of up to 30 kN, which is of particular importance for the longevity of the sensor, especially in the case of heavy solids such as iron ore. The materials used (FKM seals, PPS insulation) inside the coupling enable the use of the sensor at process temperatures of up to 80 °C (176 °F).
The short transmission time of the 2-wire HART electronics and the high measuring accuracy (+/- 2 mm (0.0065 ft.)) contributed to the increase in efficiency. A total of 15 measuring points were equipped with the TDR sensors in this project, which work without any problems.
The user-friendly implementation of the sensors resembled a smart "plug-and-play" installation, and consistent level determination could be guaranteed right from the start. NivoGuide® NG 3000 series are also designed according to the normative requirements of functional safety in order to guarantee safety functions with a risk reduction according to SIL2.
A menu-driven quick start wizard made commissioning easy, safe and efficient. The integrated display now enables practical checking of measurements and echo curves in real time. Furthermore, the TDR sensor is "capable of learning" and recognizes which signals are changed. The processes of steel production in the Dominican Republic are thus constantly optimized.

