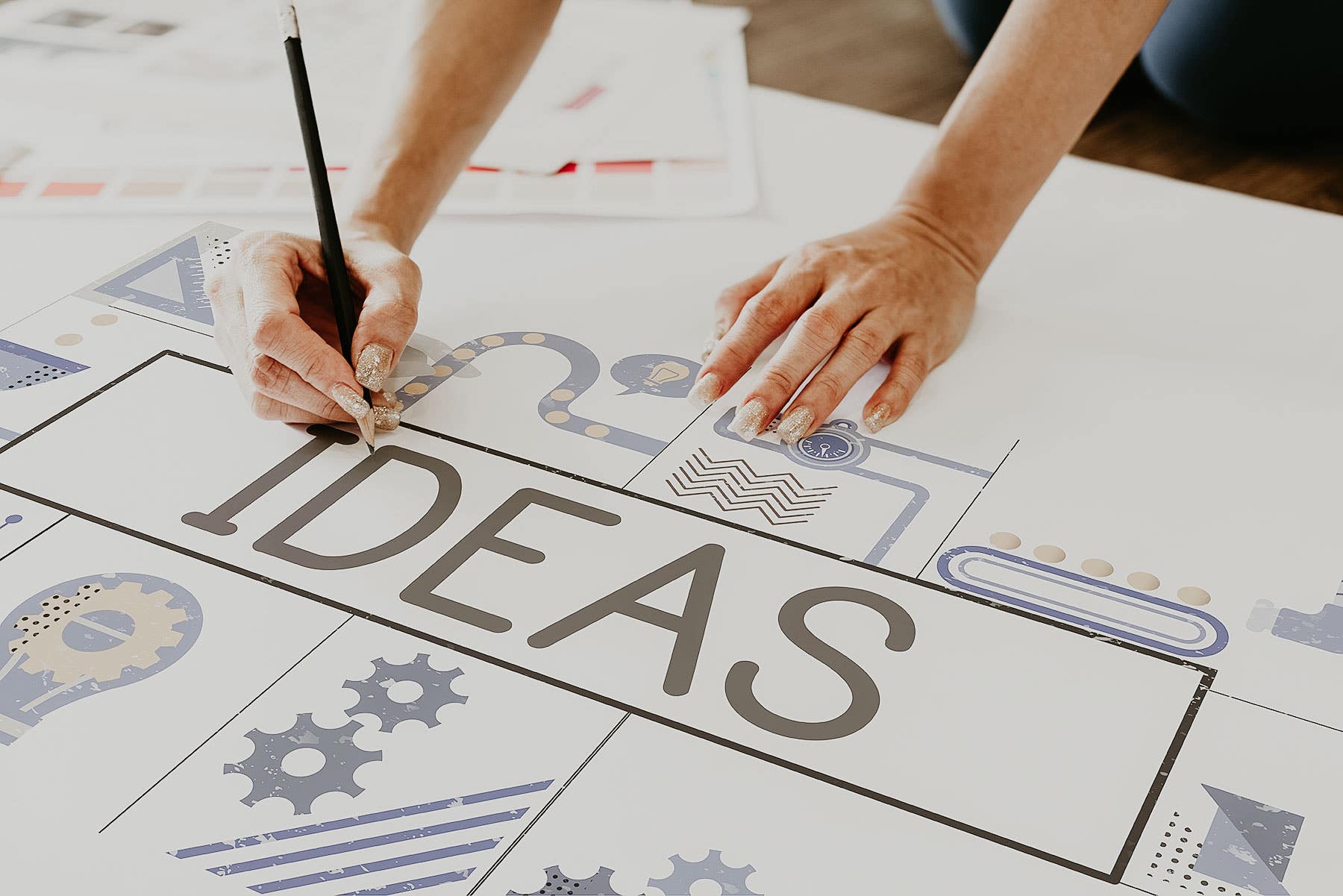
Mechanical, non-contact or guided microwave
Modern, high-quality technologies ensure a continuous stress-free manufacturing process in plants. When it comes to detecting fill levels in silos and material processing operations, sensors with a high degree of compatibility for different process containers provide the optimum support. Depending on the processing stage, the material to be controlled can be of very different nature and place different demands on the measurement technology to be used. The UWT range offers capacitive measurement technology, transducers as well as mechanical solutions for use in solids and liquids.
In continuous measurement, the solutions have been expanded to include an innovative TDR product line in addition to plumb bob and non-contact radar technology. This means that the appropriate sensor technology can be configured from an extensive repertoire for plants, depending on the process conditions and the medium to be measured. A feed manufacturer producing in Germany already implemented guided radar in some warehouse processes.
Precise level measurement in the storage process
To ensure a continuous value chain, both the raw products and the finished end product must be stored properly and transparently. In a feed plant or in flour production within grain mills, these include not only the finished flours and pellets but also various raw products such as wheat, spelt, soybeans, rapeseed, corn, barley, rye, bran, oats, millet, pulses and green flour, which pass through various processing stages in the plant on their way to becoming the end product. Various oils and fats are added to the respective recipes, if necessary. At different stages of the production process, the solids in particular have different densities, different particle sizes with different dust generation, and different moisture contents. The storage bins of a feed plant in Germany vary very individually in height, in some cases reaching up to 100 meters. Initially, the raw materials are transported and stored in raw material cells (silo cells) after delivery, weighing and cleaning. They remain there until further processing. The end products are also temporarily stored in finished cells until delivery. In addition, further storage processes are integrated within the plants. These are usually different pre-containers, storage cells or post-depositories, where ingredients are stored before they are added. Within different process stages in grain processing plants, overfilling of silos, a production stop or reduced productivity are prevented by suitable level determination. Errors that occur during conveying, weighing, and mixing in the plant can rarely be compensated for or corrected. Therefore, reliable and high-quality measuring technology was also essential for the equipment of the feed manufacturer. Functionality, ease of use and long product life, in accordance with the high requirements and standards of the food industry, are essential. Innovative technologies combined with extensive industry knowledge enable UWT GmbH to provide the grain and feed industry with a comprehensive range of customized measurement technology. UWT solutions for level and point level measurement have been successfully used in silo systems and process vessels of grain and feed mills worldwide for many years. In practice, the simple electromechanical measuring method of the plumb bob has proven itself many times over. The sensor is considered a classic among overfill detectors and is often used for extremely adhesive materials as well as for existing struts in the process vessel. Occasionally, the FMCW radar level transmitter is also used more and more frequently. Especially where non-contact measurement technology is desired in special applications. A robust measurement in solid as well as liquid materials is offered by TDR sensors. These guided radar devices are used for consistently precise continuous level measurement under difficult varying process conditions with high pull-off forces, caking or condensate formation. Reliable overfill protection and empty detection are guaranteed.
Simple, universal and reliable with guided radar sensors
Due to the versatility of its process conditions as well as material variations, the plant operator decided to install several guided radar sensors within the warehouse processes. TDR devices are characterized by their high precision and at the same time simple and efficient handling. This insensitive technology is considered multi-talented in all materials and consistently provides a reliable level signal. High frequency microwave pulses are coupled to a cable or rod and guided along the probe. The emitted pulse is reflected by the product surface. The time difference between the transmitted and reflected pulse is converted into a level. Unlike plumb bob, with guided radar there are no mechanically moving parts inside the process vessels. In contrast to non-contact radar, microwaves are emitted at lower frequencies, which means that no interfering reflections are generated even at high dust intensities. As a result, the energy component of the microwave can be used exclusively for specific level determination. It is therefore ideally suited for use in storage processes with dusty environments, such as those in the grain processing industry.
Therefore, UWT has completed its product portfolio of continuous level sensors with the guided wave radar NivoGuide®, which is suitable for use in both solids and liquids. It is ATEX certified as well as dust explosion proof and measures precisely to +/-2 mm even under difficult process conditions in silos, tanks and pipes. Two series have been implemented, the NivoGuide® NG 3000, which is specifically designed for the needs of solids, and the
The NivoGuide®
was initially used in the grain silos and flour bunkers of the feed plant. In addition to high safety standards that must be met in grain applications, several other factors play a decisive role in the efficient use of the appropriate measurement technology. For example, especially in finished product silos or due to condensation during netting, sticking or bridging often occurs at the delivery, which can lead to faulty switching. In such process vessels, the rope version of the guided radar should be selected because it is provided with a special PA coating to both prevent sticking and provide a solution for abrasive media. The PA coating also improves the abrasion resistance of the ropes, as fine-grained bulk materials cannot get stuck in the meshes of the rope. The rope thicknesses are to be applied depending on the silo height and mechanical load. This can play a role for bulk materials with corresponding grain sizes and high pull-off forces, which justifies the consideration for the TDR's probe passage specially designed for the grain-processing sector. In fact, a coupling optimized for bulk solids is installed, which is characterized by an axial support of the probe inside the process connection and differs constructively from common guided radar sensors. As a result, the tensile forces acting on the probe are optimally distributed, allowing a load of up to 30 kN (kilonewtons). Different rope diameters of 4 and 6 mm are optimally designed for the prevailing tensile forces. Thus, the rope does not travel even under high loads and supports the longevity of the sensor. Generally, a thicker rope should be used for high silos. In their constructional design, the ropes of the solid TDR are equipped with twisted thicker strands, unlike the guided radar for liquids. In addition, the weave of the ropes is such that a flexible rope is used in liquids and a more rigid rope that hangs tightly in the silo is used for solids. In the rod design of the NivoGuide® series, a 16 mm rod diameter is used to increase resistance to bending during surface movement of the bulk material when filling or discharging. The rod and cable boom receptacle also differs depending on the media, this is tapered for liquid units to allow for dripping.
The use in the narrow, high silo containers of the finished goods silos for the final storage of different grain products of the feed manufacturer was feasible with the rope version of the NG 3 with large measuring distances of up to 75 meters without loss of performance. The installation position required a wall distance of only 30 cm. Typical product properties such as moisture content, mixing ratio or particle size did not play a role and made project planning simple. Even with changing process conditions of temperature, pressure or grain DK values, the accuracy of the measurement result is not affected, since no adjustment to the respective medium is necessary. Smooth use in the plant's universal silos was thus also easy to implement.
Intelligent TDR with helpful diagnostic options
The intelligent software of the guided radar sensor system enables high plant availability. Echo curves are recorded and stored, and over time the sensor learns, so to speak, and knows how to distinguish which signals are changing and which are constantly in one place. Interfering installations can thus be identified and service technician call-outs due to faulty level signals are avoided. The programming element with a plug-on display and operating module and a cover with a viewing window makes the TDR NivoGuide® very user-friendly to operate. Extensive diagnostic functions ensure fast and safe handling. For example, current measured values and commissioning parameters are displayed. The parameterized data can be stored and transferred to other guided radar units, which results in a considerable time saving of the installation procedure. The guided quick commissioning in 5 simple steps is intuitively applied to the application with optimal adaptation of the sensor. This made it easy for the plant operator to quickly put the NivoGuide® sensors into operation.
Transparency and planning reliability through visualization
Users with a number of scattered storage silos are also finding it increasingly necessary to equip their plants with automated visualization and monitoring of the data in addition to continuous level measurement. Detected measurement results from the sensors are quickly and easily displayed using software and can be conveniently called up from the screen at any time. Effective silo logistics then also increase transparency and planning reliability for the plant operator. The TDR series of the NivoGuide® has therefore been provided with the appropriate equipment, which includes an analog 4-20mA signal as well as a Modbus RTU or Profibus DP interface for the evaluation systems.
The
data visualization provides the plant operator with fill levels in height, percentage, weight or volume for transparent feed production. Trends are stored, e-mails about fill levels or silo full messages can be activated, even the individual fill level sensors can be parameterized. Clean route planning and targeted stockpiling for cost optimization in material delivery can thus be facilitated.