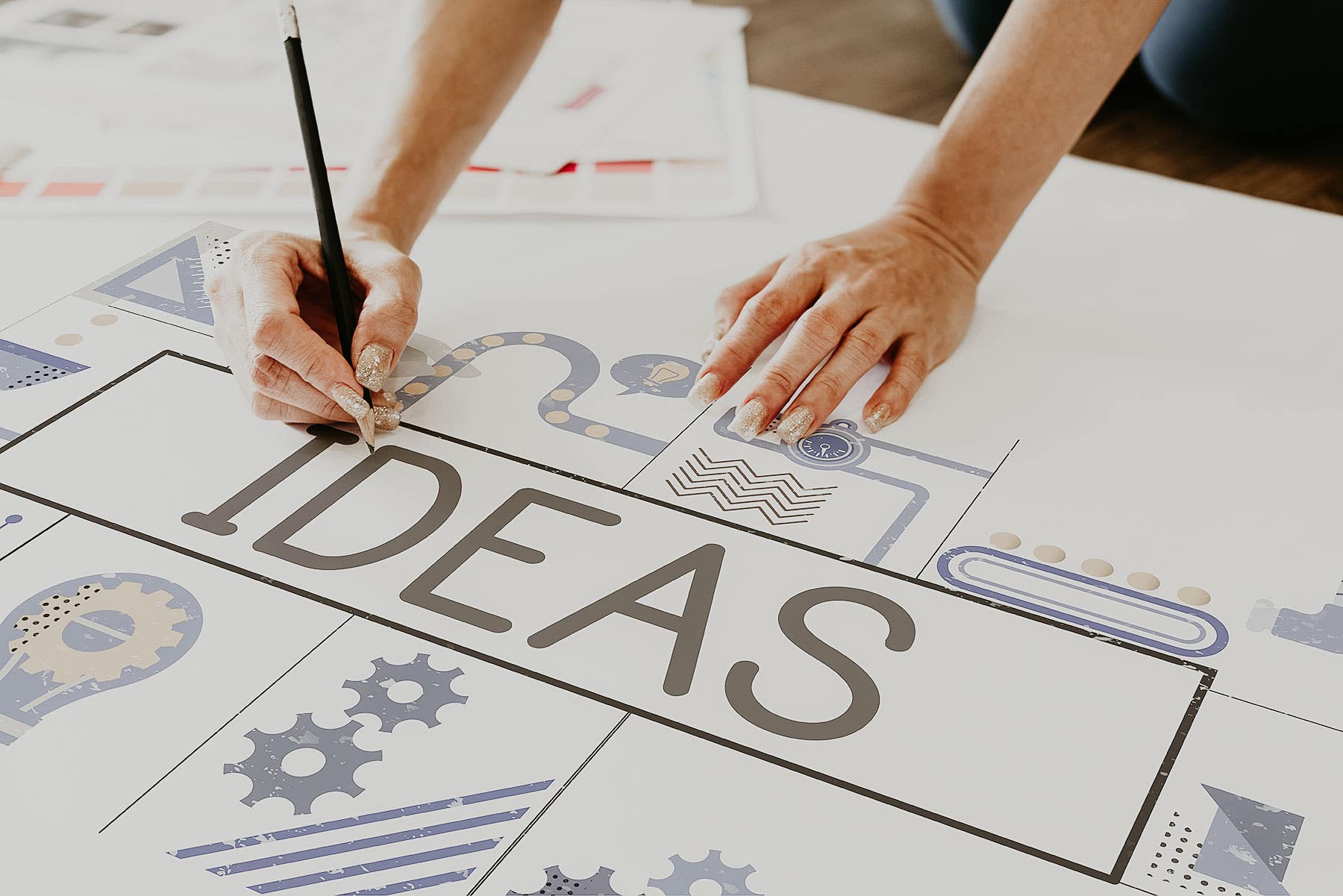
Mechanisch, berührungslos oder geführte Mikrowelle
Moderne, hochwertige Technologien gewährleisten einen kontinuierlichen stressfreien Herstellungsablauf in Anlagen. Bei der Detektion von Füllständen in Silos und materialverarbeitenden Prozessen bieten Sensoren mit hoher Kompatibilität für unterschiedliche Prozessbehälter die optimale Unterstützung. Das zu kontrollierende Material kann je nach Bearbeitungsstufe von ganz unterschiedlicher Beschaffenheit sein und unterschiedliche Anforderungen an die einzusetzende Messtechnik stellen. Das UWT Sortiment bietet für den Einsatz in Feststoffen und Flüssigkeiten kapazitive Messtechnik, Schwinger sowie mechanische Lösungen.
In der kontinuierlichen Messung wurden die Lösungen ergänzend zu Lotsystem und berührungsloser Radartechnologie um eine innovative TDR Produktlinie erweitert. So kann für Anlagen je nach Prozessbedingung und zu messendem Medium die passende Sensorik aus einem umfangreichen Repertoire konfiguriert werden. Ein Futtermittelhersteller, der in Deutschland produziert, implementierte das geführte Radar bereits in einige Lagerprozesse.
Präzise Füllstandmessung im Lagerprozess
Um eine kontinuierliche Wertschöpfungskette sicherzustellen, müssen sowohl die Rohprodukte als auch das fertige Endprodukt fachgerecht und transparent gelagert werden. In einer Futtermittelanlage oder bei der Mehlherstellung innerhalb Getreidemühlen sind dies neben den fertigen Mehlsorten und Pellets verschiedene Rohprodukte wie Weizen, Dinkel, Soja, Raps, Mais, Gerste, Roggen, Kleie, Hafer, Hirse, Hülsenfrüchte und Grünmehl, welche auf dem Weg zum Endprodukt in der Anlage unterschiedliche Verarbeitungsstufen durchlaufen. Diverse Öle und Fette werden den jeweiligen Rezepturen ggf. beigemischt. In verschiedenen Phasen des Produktionsprozesses weisen insbesondere die Feststoffe unterschiedliche Dichten, verschiedene Korngrößen mit unterschiedlicher Staubentwicklung sowie einen differierenden Feuchtigkeitsgehalt auf. Die Lagerbehälter einer Futtermittelanlage in Deutschland variieren in ihrer Höhe sehr individuell und erreichen vereinzelt bis zu 100 Meter. Zu Beginn werden die Rohwaren nach der Anlieferung, Verwiegung und Reinigung in Rohstoffzellen (Silozellen) befördert und eingelagert. Sie bleiben dort bis zur weiteren Verarbeitung. Auch die Endprodukte sind in Fertigzellen bis zur Auslieferung zwischengelagert. Daneben sind innerhalb der Anlagen noch weitere Lagervorgänge integriert, wobei es sich hier meist um unterschiedliche Vorbehälter, Abstehzellen oder Nachdepots handelt, wo Zutaten vor ihrer Beimengung gelagert sind. Innerhalb unterschiedlicher Prozessstufen in getreideverarbeitenden Anlagen wird durch geeignete Füllstandbestimmung der Überfüllung von Silos, einem Produktionsstopp oder verminderter Produktivität vorgebeugt. Fehler, die während des Förderns, Wiegens und Mischens in der Anlage auftreten, können selten wieder ausgeglichen oder behoben werden. Daher war auch für die Ausstattung des Futterherstellers eine sichere und qualitativ hochwertige Messtechnik unerlässlich. Es kommt auf Funktionalität, einfache Handhabung und lange Lebensdauer der Produkte, in Übereinstimmung mit den hohen Anforderungen und Standards der Lebensmittelindustrie an. Innovative Technologien kombiniert mit umfassendem Branchenwissen ermöglichen der UWT GmbH der Getreide- und Futtermittelindustrie eine umfangreiche Palette an maßgeschneiderter Messtechnik bereitzustellen. UWT Lösungen für die Messung von Füllstand und Grenzstand werden in Siloanlagen und Prozessbehältern von Getreide- und Futtermittelwerken bereits seit vielen Jahren weltweit erfolgreich eingesetzt. In der Praxis hat sich mehrfach das einfache elektromechanische Messverfahren des Lots bewährt. Der Sensor gilt als ein Klassiker unter den Überfülldetektoren und kommt gerne bei extrem anhaftenden Materialien zum Einsatz sowie bei vorhandenen Verstrebungen im Prozessbehälter. Bisweilen kommt auch immer häufiger der FMCW-Radar-Füllstandmessumformer zum Einsatz. Insbesondere dort wo in speziellen Anwendungsfällen eine berührungslose Messtechnik gewünscht ist. Eine robuste Messung in festen sowie flüssigen Materialien bieten TDR Sensoren. Diese geführten Radargeräte werden zur konstant präzisen kontinuierlichen Füllstandmessung unter schwierigen variierenden Prozessgegebenheiten mit hohen Abzugskräften, Anbackungen oder Kondensatbildung eingesetzt. Eine zuverlässige Überfüllsicherung sowie Leermeldung ist gewährleitet.
Einfach, universell und zuverlässig mit geführter Radarsensorik
Aufgrund der Vielseitigkeit seiner Prozessbedingungen sowie Materialvariationen entschied sich der Anlagenbetreiber für die Installation mehrerer geführter Radarsensoren innerhalb der Lagerprozesse. TDR Geräte zeichnen sich durch ihre hohe Präzision und zugleich einfache und effiziente Handhabung aus. Diese unempfindliche Technologie gilt als Multitalent in sämtlichen Materien und liefert durchgehend ein zuverlässiges Füllstandsignal. Hochfrequente Mikrowellenpulse werden auf ein Seil oder einen Stab gekoppelt und entlang der Sonde geführt. Der ausgesendete Impuls wird von der Produktoberfläche reflektiert. Die Zeitdifferenz zwischen dem gesendeten und reflektierten Impuls wird in einen Füllstand umgerechnet. Anders als beim Lot befinden sich mit dem geführten Radar keine mechanisch bewegten Teile innerhalb der Prozessbehälter. Im Gegensatz zum berührungslosen Radar werden Mikrowellen mit niedrigeren Frequenzen ausgesendet, wodurch auch bei hoher Staubintensität keine Störreflexion erzeugt wird. Dadurch kann der Energieanteil der Mikrowelle ausschließlich zur konkreten Füllstandbestimmung verwendet werden. Er eignet sich also optimal für den Einsatz in Lagerprozessen mit staubiger Umgebung, wie die der getreideverarbeitenden Industrie.
Daher hat UWT das Produktportfolio der kontinuierlichen Füllstandsensoren mit dem geführten Radar NivoGuide®, der für den Einsatz sowohl in Feststoffen als auch Flüssigkeiten geeignet ist, komplettiert. Er ist ATEX zertifiziert sowie stauexplosionsgeschützt und misst auch unter schwierigen Prozessbedingungen in Silos, Tanks und Rohren präzise auf +-2mm genau. Es wurden zwei Serien umgesetzt, der NivoGuide® NG 3000, der speziell auf die Bedürfnisse von Feststoffen ausgerichtet ist und der
für Anwendungen in Flüssigkeiten, Pasten, Schäumen, Schlämmen, Ölen sowie zur Trennschichtmessung. Die Geräteausführungen sind je mit individuell auf die Applikation anpassbaren Auslegern mit Stab- und Seilverlängerung ausgestattet.Der NivoGuide®
kam zunächst in den Getreidesilos und Mehlbunkern der Futtermittelanlage zum Einsatz. Neben hohen Sicherheitsstandards, die es in Getreideanwendungen zu erfüllen gilt, spielen einige weitere Faktoren eine entscheidende Rolle für den effizienten Einsatz der passenden Messtechnik. So kommt es insbesondere in Fertigwarensilos oder aufgrund von Kondenswasserbildung beim Netzen häufig zu Anhaftungen oder Brückenbildung am Ausleger, was zu Fehlschaltungen führen kann. In solchen Prozessbehältern ist die Seilausführung des geführten Radars zu wählen, denn dieses ist mit einer speziellen PA-Beschichtung versehen, um sowohl Anhaftung vorzubeugen als auch eine Lösung für abrasive Medien zu schaffen. Die PA-Beschichtung verbessert zudem die Abriebfestigkeit der Seile, da sich feinkörnige Schüttgüter nicht in den Maschen des Seils festsetzen können. Die Seilstärken sind je nach Silohöhe und mechanischer Belastung anzuwenden. Diese kann bei Schüttgütern mit entsprechenden Korngrößen und hohen Abzugskräften eine Rolle spielen, was die Überlegung für die speziell für den getreideverarbeitenden Bereich ausgelegte Sondendurchführung des TDR rechtfertigt. Und zwar ist eine auf den Schüttgutbereich optimierte Einkopplung verbaut die sich durch eine axiale Abstützung der Sonde im inneren des Prozessanschlusses auszeichnet und sich konstruktiv zu gängigen geführten Radarsensoren unterscheidet. Dadurch werden die auf die Sonde wirkenden Zugkräfte optimal verteilt, was eine Belastung von bis zu 30kN (Kilonewton) ermöglicht. Unterschiedliche Seildurchmesser von 4 und 6mm sind optimal auf die herrschenden Zugkräfte ausgelegt. Das Seil reist also auch unter hoher Belastung nicht und unterstützt die Langlebigkeit des Sensors. Generell sollte bei hohen Silos ein dickeres Seil verwendet werden. In ihrem konstruktiven Aufbau sind die Seile des Feststoff TDR im Unterschied zum geführten Radar für Flüssigkeiten mit verdrehten dickeren Litzen ausgestattet. Zudem ist die Webart der Seile so, dass in Flüssigkeiten ein flexibles Seil und für Feststoffe ein eher starres Seil, das straff im Silo hängt, verwendet wird. Bei der Stabausführung der NivoGuide® Serie wird mit einem 16mm Stabdurchmesser der Widerstand gegen Biegung bei Oberflächenbewegung des Schüttguts beim Befüllen oder Entleeren erhöht. Die Aufnahme des Stab- und Seilauslegers unterscheidet sich ebenfalls je nach Medium, diese ist bei Flüssigkeitsgeräten konisch, um ein Abtropfen zu ermöglichen.Der Einsatz in den engen, hohen Silobehältern der Fertigwarensilos zur Endlagerung unterschiedlicher Getreideprodukte des Futtermittelherstellers war mit der Seilausführung des NG 3 mit großen Messdistanzen bis zu 75 Meter ohne Performanceverlust realisierbar. Die Montageposition erforderte hierbei einen Wandabstand von lediglich 30 cm. Typische Füllguteigenschaften wie Feuchtegehalt, Mischverhältnis oder Korngröße spielten keine Rolle und machten die Projektierung einfach. Auch bei sich ändernden Prozessbedingungen von Temperatur, Druck oder Getreide DK Werten wird die Genauigkeit des Messergebnisses nicht beeinflusst, da kein Abgleich auf das jeweilige Medium notwendig ist. Ein reibungsloser Einsatz in den Universalsilos der Anlage war somit ebenfalls problemlos umsetzbar.
Intelligenter TDR mit hilfreichen Diagnosemöglichkeiten
Die intelligente Software der geführten Radarsensorik ermöglicht eine hohe Anlagenverfügbarkeit. Echokurven werden aufgezeichnet und gespeichert und im Laufe der Zeit lernt der Sensor sozusagen dazu und weiß zu unterscheiden welche Signale sich verändern und welche sich konstant an einer Stelle befinden. Störende Einbauten können so identifiziert werden und Einsätze von Servicetechnikern aufgrund fehlerhafter Füllstandsignale werden vermieden. Das Programmierelement mit einem aufsteckbaren Anzeige- und Bedienmodul sowie einem Deckel mit Sichtfester ermöglicht ein sehr nutzerfreundliches Bedienen des TDR NivoGuide®. Umfangreiche Diagnosefunktionen sorgen für ein rasches und sicheres Handling. Es werden beispielsweise aktuelle Messwerte sowie Inbetriebnahme Parameter angezeigt. Die parametrierten Daten können gespeichert und auf andere geführte Radargeräte übertragen werden, was eine erhebliche Zeitersparnis des Installationsvorgangs zur Folge hat. Die geführte Schnellinbetriebnahme in 5 einfachen Schritten erfolgt intuitiv auf die Anwendung mit optimaler Anpassung des Sensors. Für den Anlagenbetreiber war es somit ein Leichtes die NivoGuide® Sensoren rasch in Betrieb zu nehmen.
Transparenz und Planungssicherheit durch Visualisierung
Anwender mit einer Reihe an gestreut platzierten Lagersilos erachten es außerdem für ihre Anlagen als immer notwendiger, diese zusätzlich zur kontinuierlichen Messung der Füllstände, bevorzugt mit einer automatisierten Visualisierung und Überwachung der Daten auszustatten. Detektierte Messergebnisse der Sensoren werden schnell und einfach mit einer Software dargestellt und sind jederzeit bequem vom Bildschirm aus abrufbar. Durch effektive Silologistik erhöht sich dann auch Transparenz und Planungssicherheit für den Anlagenbetreiber. Die TDR Reihe des NivoGuide® wurde daher mit einer entsprechenden Ausstattung versehen, die ein analoges 4-20mA Signal sowie eine Modbus RTU oder Profibus DP Schnittstelle für die Auswertesysteme beinhaltet.
Die Datenvisualisierung
liefert dem Anlagenbetreiber für eine transparente Futtermittelherstellung Füllstände in Höhe, Prozent, Gewicht oder Volumen. Es werden Trends gespeichert, E-Mails über Füllstände oder Silovollmeldungen können aktiviert werden, sogar die einzelnen Füllstandsensoren lassen sich parametrieren. Saubere Routenplanung und gezielte Bevorratung für die Kostenoptimierung in der Materialauslieferung können so erleichtert werden.